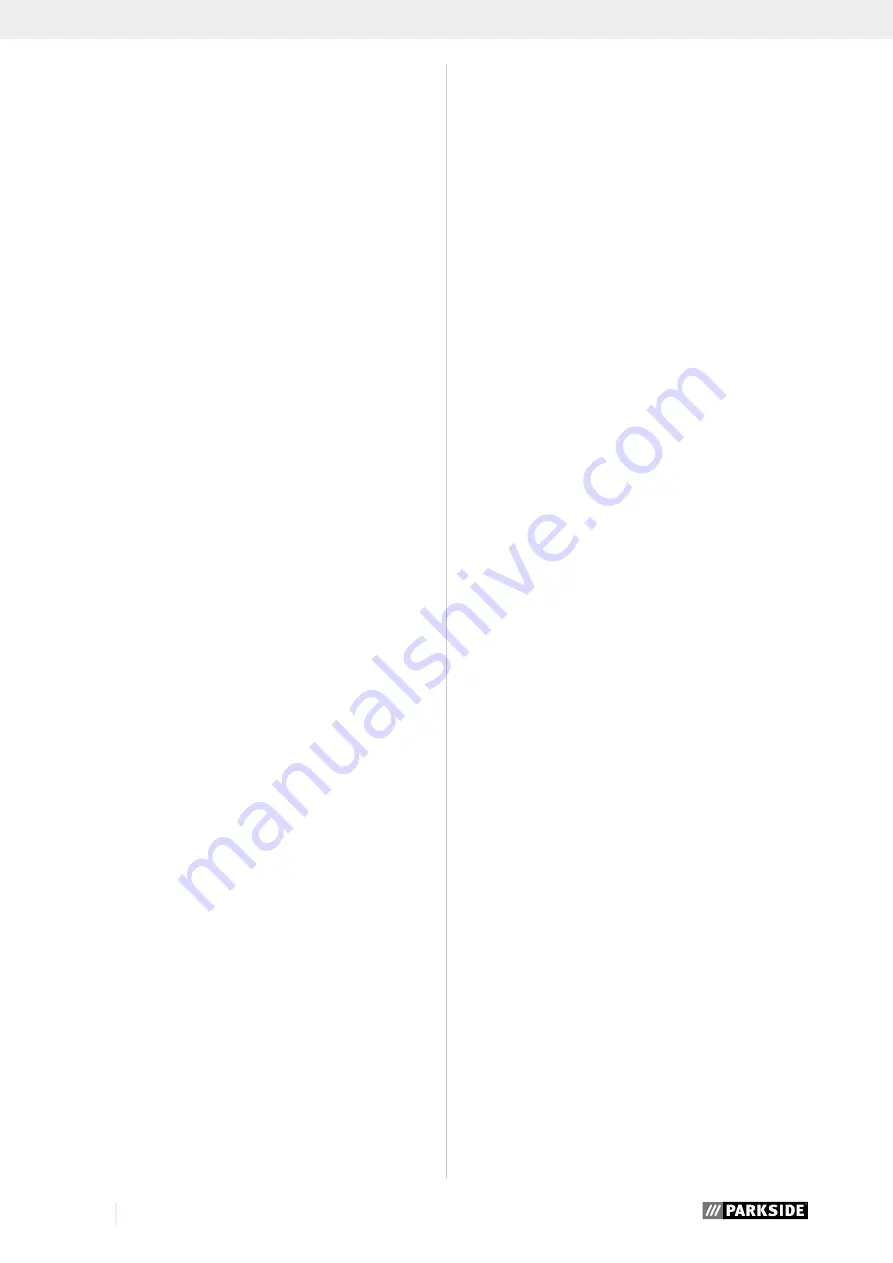
60
GB
8.6 Fitting/replacing the saw blade (fig. 11, 12)
m
WARNING:
Pull out the mains plug and wear protective
gloves.
1. Remove the saw blade guard (4) (see 8.3).
2. Unscrew the screws (34) on the bottom saw blade cover
(35) and open it out.
3. Loosen the nut by applying the 19 mm ring spanner (21) to
the nut and holding the motor shaft in place with an 8 mm
ring spanner (20) (see fig. 12).
ATTENTION:
Turn the nut in the direction of rotation of
the saw blade.
4. Take off the outer flange and pull the old saw blade down
and off the inner flange at an angle.
5. Clean the saw blade flange carefully with a wire brush
before installing the new saw blade.
6. Insert the new saw blade in the reverse sequence and
tighten.
m
WARNING:
Pay attention to the running direction.
The cutting angle of the teeth must point in the running di-
rection, i.e. forwards (see arrow on the saw blade guard
(4)).
7. Close the bottom saw blade cover (35) and tighten the
screws (34) again.
8. Refit the saw blade guard (4) and adjust it (see 8.3).
m
WARNING:
Check the protective devices before working
with the saw again.
8.7 Fitting the parallel stop (fig, 2, 15)
1. Fasten the holder (16) to the table with the help of the lock-
ing knobs (15) and the clamping plates (15a).
2. Make sure that the holder (16) is aligned parallel to the
saw blade (5). If necessary, readjust it with the aid of the
scale (38).
3. Slide the sliding block along the groove (37) in the stop
rail (17).
4. Fasten the stop rail (17) to the holder (16) with the help of
the screws (16a).
8.8 Fitting the transverse stop (fig. 18)
1. Slide the transverse stop (2) in the groove (40) of the saw
table (1).
2. Loosen the turning handle (19).
3. Turn the transverse stop (2) until the arrow points to the
desired angle.
4. Retighten the turning handle (19).
8.9 Chip extraction (fig. 13)
ATTENTION:
Only operate the device with an extraction
system.
Connect a suitable chip extraction system (not included in the
scope of delivery) to the suction port (36).
ATTENTION:
Check and clean the suction channels at regu-
lar intervals.
8.10 Stable fastening (fig. 25)
The machine must be securely installed, i.e. bolted down on a
workbench, machine stand or similar, as shown in fig. 25.
Use the bracket for workbench mounting (42), the screws (43)
and the washers (44) to do so.
9. Handling the equipment
9.1 Switches (fig. 1)
9.1.1 On/off switch (11)
• It is possible to switch the saw on by pressing the green “I”
button. Before starting sawing, wait until the saw blade has
reached its maximum speed.
• In order to switch the saw off again, it is necessary to press
the red “0” button.
9.1.2 Overload switch (10)
The device motor is protected against overload with an over-
load switch (10).
In the event of the nominal current being exceeded, the over-
load switch (10) switches the device off.
If this happens, proceed as follows:
• Let the device cool down for several minutes.
• Press the overload switch (10).
• Switch the device on by pressing the green “I” button.
9.2 Setting the cutting depth (fig. 1)
The saw blade (5) can be adjusted to the required cutting
depth by turning the hand wheel (8).
• Counter-clockwise:
Greater cutting depth
• Clockwise:
Smaller cutting depth
Check the setting with a test cut.
9.3 Setting the angle (fig. 14)
Angled cuts of 0°-45° to the left of the parallel stop (7) can be
carried out with the circular table saw.
m
Before making every cut, check that no collision can occur
between the stop rail (17), transverse stop (2) and the saw
blade (5).
1. Loosen the locking handle (9).
2. Set the desired angle on the scale by turning the hand wheel
(8).
3. Lock the locking handle (9) at the desired angle setting.
9.4 Using the parallel stop (fig. 2, 15-17)
9.4.1 Stop heights (fig. 15, 16)
• The stop rail (17) of the parallel stop (7) has two guide sur-
faces at different heights.
• Depending on the thickness of the material to be cut, the stop
rail (17) must be used as shown in Fig. 15 for thick material
(workpiece thickness exceeding 25 mm) and as shown in
Fig. 16 for thin material (workpiece thickness below 25 mm).