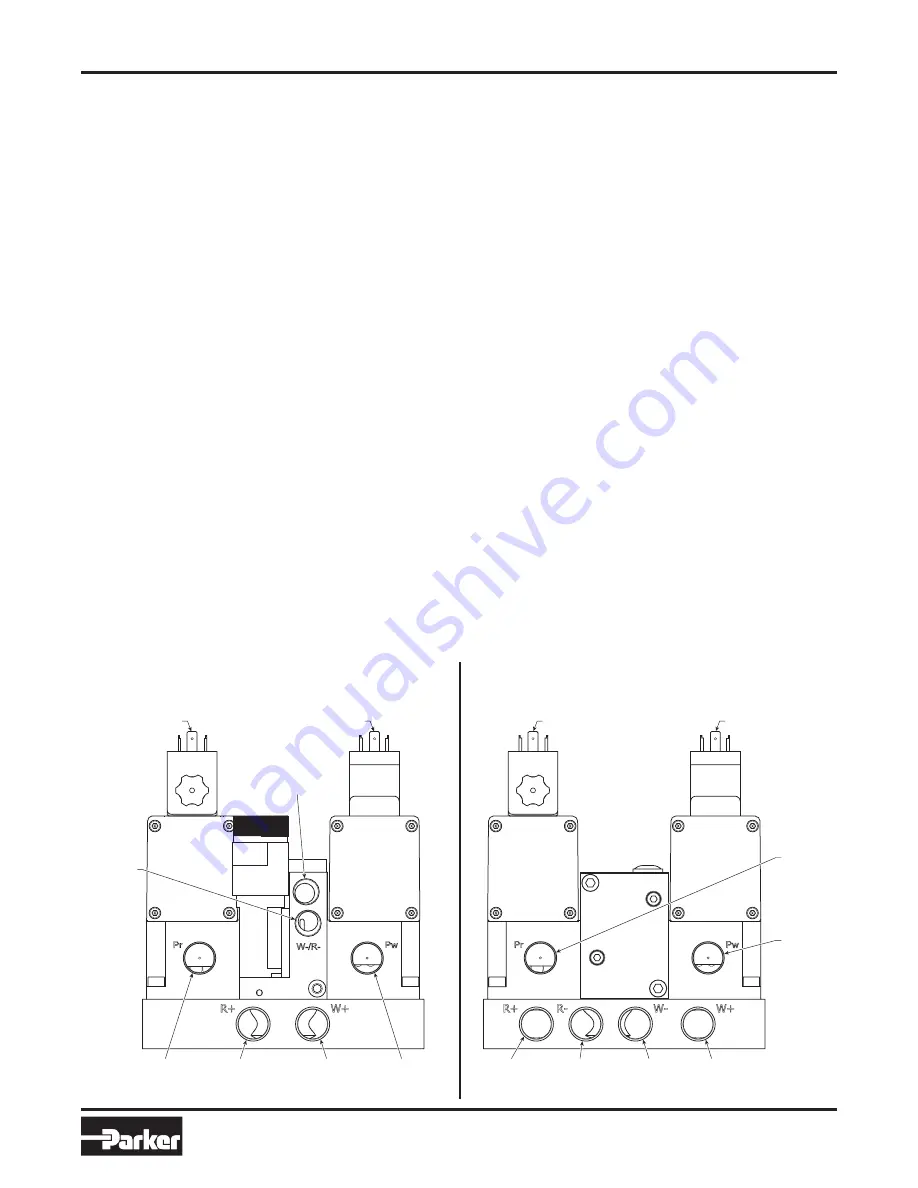
4
WCS-SIF-01
Training & Maintenance Manual
Pneumatic
Parker Hannifin Corporation
Pneumatic Division
Richland, Michigan
www.parker.com/pneumatics
Installation & Setup Instructions
Installation – Air and Electrical
A. Installing Weld Block with Existing Equipment
1. Shut off air supply to weld gun and turn power off to cell.
. Disconnect air hoses from existing weld block ports. This
will vary depending on weld gun type, and whether the
existing weld block is single or dual pressure.
Note: If the current weld block is mounted directly to the
cylinder, then only the inlet port hoses will be disconnected.
3. Disconnect solenoid connectors from valves. Be sure
to note which connectors are being used for pre-stroke
(retract) valves and weld stroke valves.
4. Remove current weld block from gun.
B. Installing Weld Block on New Equipment
5. Mount weld block spotwelding system to robot using (4) M8
screws and torque to 130 to 145 in. lbs (14.7 to 16.4 Nm).
6. Connect all air hoses to weld block (see schematic on
pages or 3).
Note: An additional air hose may be necessary for the
inlet, since this unit is dual pressure. If so, connect the
already existing hose to the Pw port (pressure weld).
This hose should be supplying scheduled pressures from
a proportional regulator. Connect the additional hose
before the proportional regulator using a T-fitting so that
full line pressure is being used. This hose should be
connected to the Pr port (pressure retract).
7. Connect the solenoid cables to the proper valves.
Connect an M1 sensor cable to the feedback sensor on
the unit. The other end of this cable should be wired to
the PLC controller.
8. Turn air supply and power on.
9. Check for air leaks. The weld cylinder should be in the
home position (completely open). If not, check that all
air hoses are connected to the correct ports. Verify that
all solenoids are de-energized, and valve overrides are
unactuated. Once this is done, verify the function of the
weld block, by actuating the weld block valves using the
manual overrides. Press and hold the retract (pre-stroke)
valve manual override. The weld cylinder should move to
the weld stroke position. Press and hold the weld stroke
valve manual override [still holding the retract (pre-stroke)
override]. The weld cylinder should now close. Release
the weld stroke override and the retract (pre-stroke)
override. The weld cylinder will return to home position.
Note:
The weld stroke portion of the cylinder will move
slower than the pre-stroke. This is due to the regulated
pressure being used, as well as the flow control.
Adjusting the speed of the cylinder will be covered in the
Setup Instructions. Repeat this process, now energizing
the solenoids. The cylinder should perform the same. If
not, verify that the solenoid connectors are located on the
proper valves. Once the unit has been properly installed,
the following setup procedure can be used to ensure that
the Parker weld system is used to its fullest potential.
Wiring
Refer to valve Instruction Sheet for proper wiring connections.
Available at: www.parker.com/pneumatic (see B6 and ISO
size valves Installation and Service Instructions).
3 Ported Installation
4 Ported Installation
Weld Stroke
Connector(s)
Exhaust
High
Pressure
Inlet
Retract
Extend
Weld
Extend
Weld
Pressure
Inlet
Weld
Return
High
Pressure
Inlet
Weld
Pressure
Inlet
Weld Stroke
Connector(s)
Retract
(Pre-Stroke)
Connector(s)
Retract
(Pre-Stroke)
Connector(s)
Retract
Extend
Weld
Extend
Weld
Return
Retract
Return