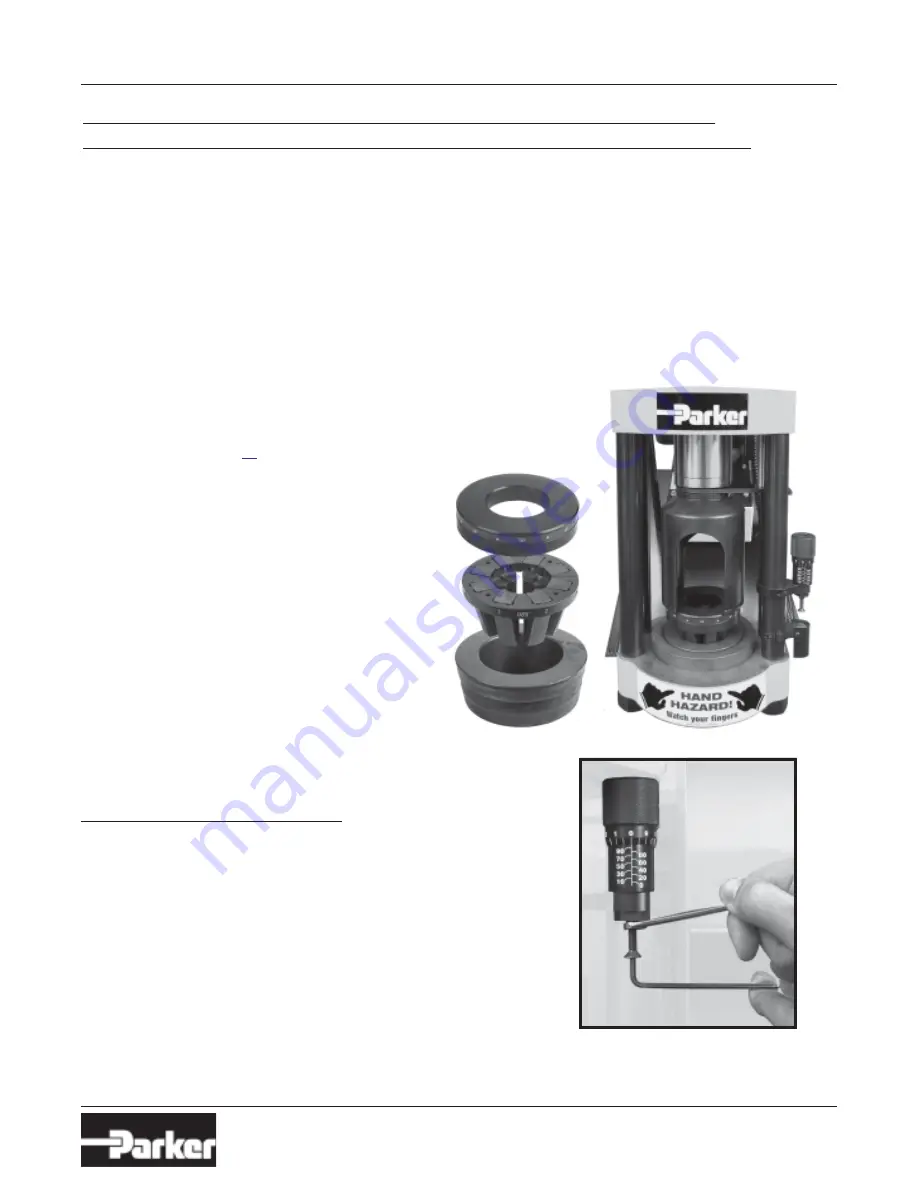
Hose Products Division
Parker Hannifin Corporation
Wickliffe, Ohio
www.parkerhose.com
4
Crimping Machine
TH8-D206
Bulletin 4480-T22-US
QUICK START GUIDE AND CALIBRATION CHECK
FOLLOW THESE STEPS BEFORE USING THE CRIMPER FOR THE FIRST TIME
Remove reservoir plug and replace with Oil Fill and Vent Cap. The Oil Fill and Vent cap and the work light
bulb are found in the accessories box.
Place the crimper on a sturdy bench in a well lit area, and plug the crimper directly into a 115 V
15 Amp wall outlet.
Do not run the crimper on an extension cord as low voltage can damage the motor.
The oil level in the pump should be approximately 1-1/2 inches below the fill plug. If necessary,
replenish with ISO Viscosity Grade 46 hydraulic oil.
Note: The crimper is calibrated prior to shipment, but a calibration check is recommended prior to using
the crimper for the first time.
Lubricate all contact surfaces and place the Cone Insert, any Small
Series die set and the Standard Pusher in the crimper in the order shown.
Note that a hose and fitting are not required for an initial calibration check.
Note: failure to lubricate all contact surfaces can
cause the Cone Insert and/or the dies to seize in
the cone base.
Slide the Pusher onto the stud on the
hydraulic ram.
Set the Micro-Crimp adjuster at “95”
Press and hold the start switch bulb.
If the ram extends and the crimper shuts off
approximately 1 second after the dies are
completely closed and the pump starts to build
pressure, the crimper is correctly calibrated.
If the time to shut off is not approximately 1
second, the crimper must be recalibrated. Recalibrate as follows:
CALIBRATION INSTRUCTIONS
Hold the micrometer barrel with a 5/16 inch open end wrench
and rotate the stem either in or out with a 5/32 inch hex key wrench.
If the motor shuts off too quickly or before the dies are
completely closed, rotate the stem in.
If the motor does not shut off or shuts off in substantially more
than 1 second, rotate the stem out.
Recheck calibration.
Start Guide and Calibration Check