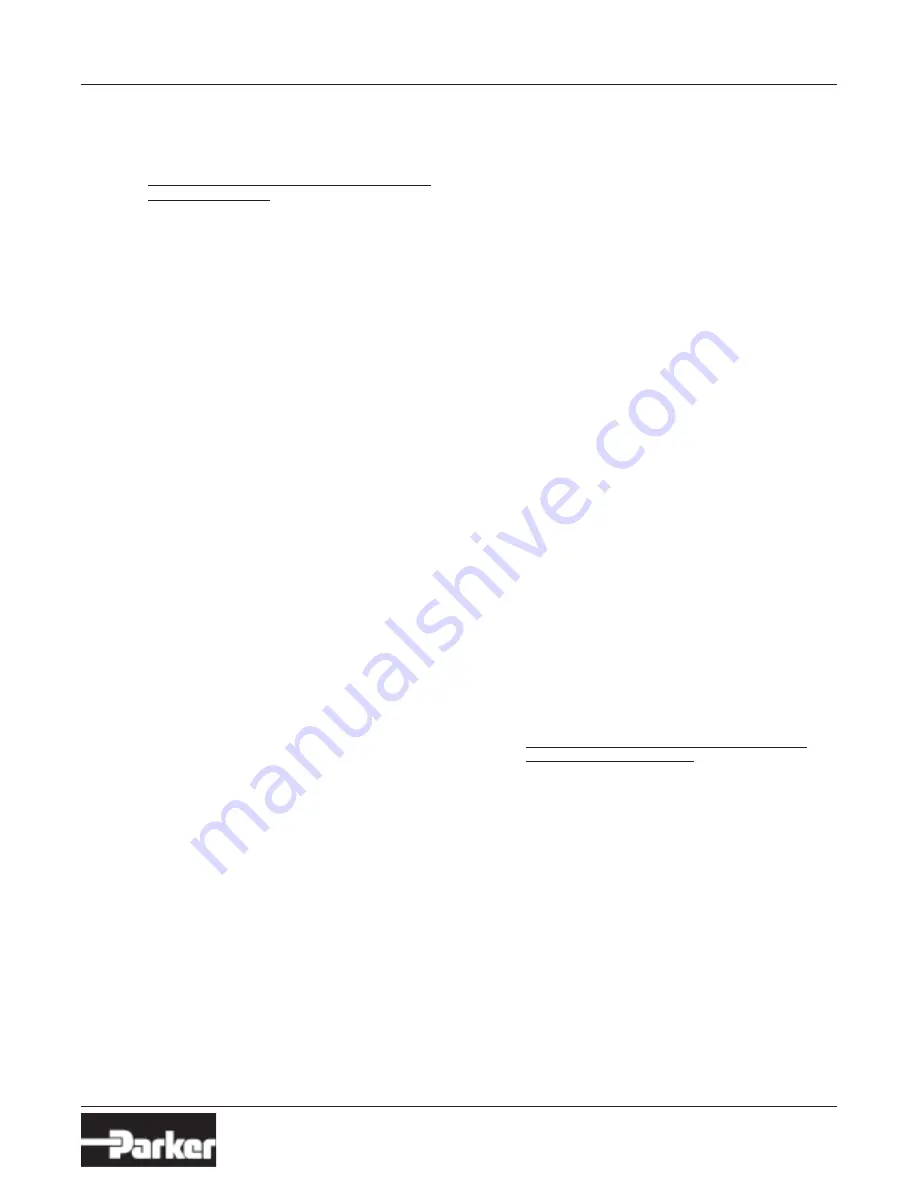
Hose Products Division
Parker Hannifin Corporation
Wickliffe, Ohio
www.parkerhose.com
14
Crimping Machine
TH8-D206
Bulletin 4480-T22-US
or if the sleeve is bumped or moved enough to cause
disconnect. Threaded couplings should be considered
where there is a potential for accidential uncoupling.
3.0
HOSE AND FITTING ASSEMBLY AND INSTALLA-
TION INSTRUCTIONS
3.1
Component Inspection: Prior to assembly, a careful
examination of the Hose and Fittings must be per-
formed. All components must be checked for correct
style, size, catalog number, and length. The Hose must
be examined for cleanliness, obstructions, blisters,
cover looseness, kinks, cracks, cuts or any other vis-
ible defects. Inspect the Fitting and sealing surfaces
for burrs, nicks, corrosion or other imperfections. Do
NOT use any component that displays any signs of
nonconformance.
3.2
Hose and Fitting Assembly: Do not assemble a
Parker Fitting on a Parker Hose that is not specifically
listed by Parker for that Fitting, unless authorized in
writing by the engineering manager or chief engineer
of the appropriate Parker division. Do not assemble a
Parker Fitting on another manufacturers Hose or a
Parker Hose on another manufacturers Fitting unless
(i) the engineering manager or chief engineer of the
appropriate Parker division approves the Assembly in
writing or that combination is expressly approved in
the appropriate Parker literature for the specific Parker
product, and (ii) the user verifies the Assembly and
the application through analysis and testing. For Parker
Hose that does not specify a Parker Fitting, the user is
solely responsible for the selection of the proper Fit-
ting and Hose Assembly procedures. See instruction
1.4.
The Parker published instructions must be followed
for assembling the Fittings on the Hose. These in-
structions are provided in the Parker Fitting catalog
for the specific Parker Fitting being used, or by calling
1-800-CPARKER, or at www.parker.com.
3.3
Related Accessories: Do not crimp or swage any
Parker Hose or Fitting with anything but the listed
swage or crimp machine and dies in accordance with
Parker published instructions. Do not crimp or swage
another manufacturers Fitting with a Parker crimp or
swage die unless authorized in writing by the engi-
neering manager of chief engineer of the appropriate
Parker division.
3.4
Parts: Do not use any Parker Fitting part (including
but not limited to socket, shell, nipple, or insert) ex-
cept with the correct Parker mating parts, in accor-
dance with Parker published instructions, unless au-
thorized in writing by the engineering manager or chief
engineer of the appropriate Parker division.
3.5
Reusable/Permanent: Do not reuse any field attach-
able (reusable) Hose Fitting that has blown or pulled
off a Hose. Do not reuse a Parker permanent Hose
Fitting (crimped or swaged) or any part thereof. Com-
plete Hose Assemblies may only be reused after proper
inspection under section 4.0. Do not assemble Fit-
tings to any previously used hydraulic Hose that was
in service, for use in a fluid power application.
3.6
Pre-Installation Inspection: Prior to installation, a
careful examination of the Hose Assembly must be
performed. Inspect the Hose Assembly for any dam-
age or defects. Do NOT use any Hose Assembly that
displays any signs of nonconformance.
3.7
Minimum Bend Radius: Installation of a Hose at
less than the minimum listed bend radius may signifi-
cantly reduce the Hose life. Particular attention must
be given to preclude sharp bending at the Hose to
Fitting juncture. Any bending during installation at less
than the minimum bend radius must be avoided. If
any Hose is kinked during installation, the Hose must
be discarded.
3.8
Twist Angle and Orientation: Hose Assembly in-
stallation must be such that relative motion of machine
components does not produce twisting.
3.9
Securement: In many applications, it may be neces-
sary to restrain, protect, or guide the Hose to protect it
from damage by unnecessary flexing, pressure surges,
and contact with other mechanical components. Care
must be taken to insure such restraints do not intro-
duce additional stress or wear points.
3.10 Proper Connection of Ports: Proper physical instal-
lation of the Hose Assembly requires a correctly in-
stalled port connection insuring that no twist or torque
is transferred to the Hose when the Fittings are being
tightened or otherwise during use.
3.11 External Damage: Proper installation is not complete
without insuring that tensile loads, side loads, kink-
ing, flattening, potential abrasion, thread damage, or
damage to sealing surfaces are corrected or elimi-
nated. See instruction 2.10
3.12 System Checkout: All air entrapment must be elimi-
nated and the system pressurized to the maximum
system pressure (at or below the Hose maximum work-
ing pressure) and checked for proper function and free-
dom from leaks. Personnel must stay out of potential
hazardous areas while testing and using.
3.13 Routing: The Hose Assembly should be routed in
such a manner so if a failure does occur, the escaping
media will not cause personal injury or property dam-
age. In addition, if fluid media comes in contact with
hot surfaces, open flame, or sparks, a fire or explo-
sion may occur. See section 2.4.
4.0
HOSE AND FITTING MAINTENANCE AND RE-
PLACEMENT INSTRUCTIONS
4.1
Even with proper selection and installation, Hose life
may be significantly reduced without a continuing main-
tenance program. The severity of the application, risk
potential from a possible Hose failure, and experience
with any Hose failures in the application or in similar
applications should determine the frequency of the in-
spection and the replacement for the Products so that
Products are replaced before any failure occurs. A
maintenance program must be established and fol-
lowed by the user and, at minimum, must include in-
structions 4.2 through 4.7.
4.2
Visual Inspection Hose/Fitting: Any of the following
conditions require immediate shut down and replace-
ment of the Hose Assembly:
• Fitting slippage on Hose,
• Damaged, cracked, cut or abraded cover (any rein-
forcement exposed);
• Hard, stiff, heat cracked, or charred Hose;
Safety Guide for Selecting and Using Hose, Fittings and Related Accessories