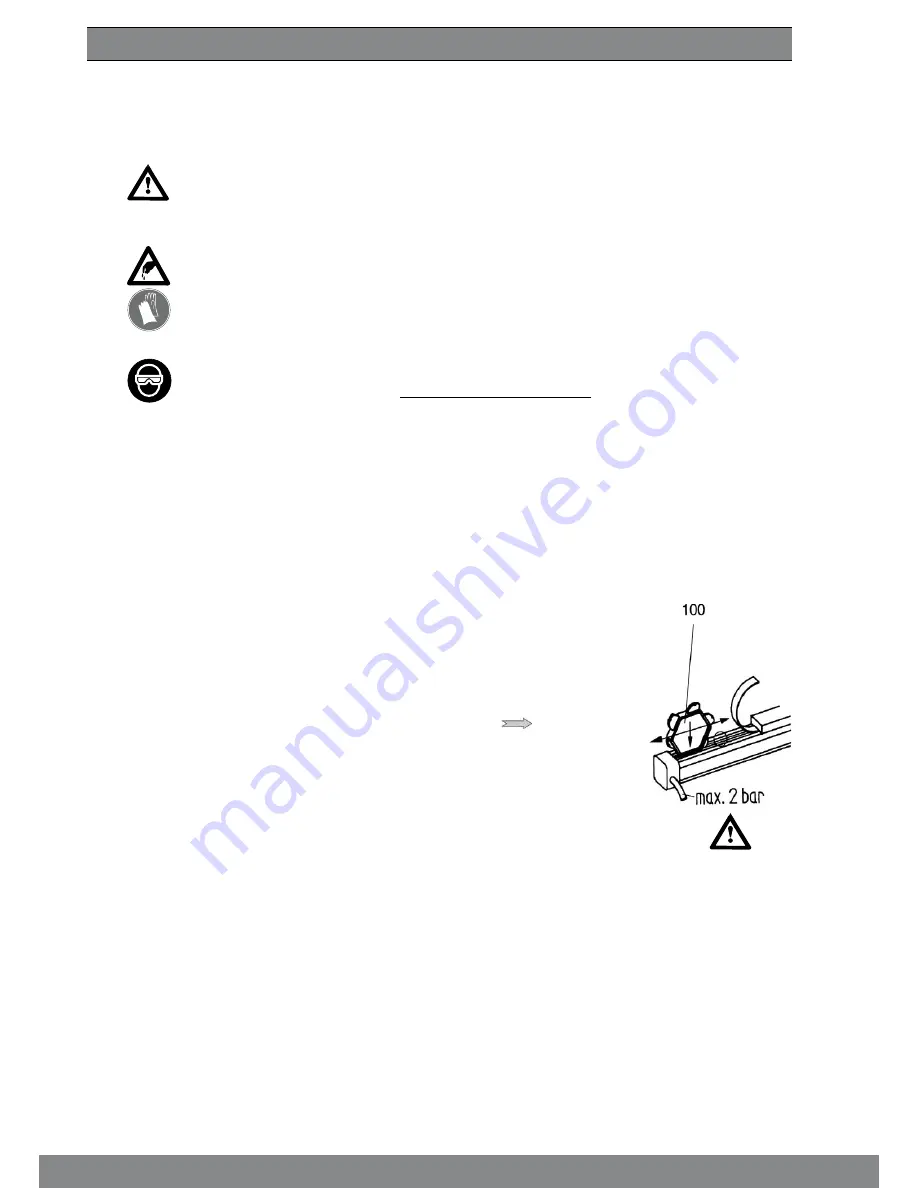
32
Modular Pneumatic Linear Drive System OSP -P / OSPP-BG
outer sealing
band
14.2 Cleaning the Inner Sealing Band OSP-P
(not Clean Room Cylinder)
Dirt particles can lodge between the inner sealing band and the cylinder bore and cause leakage.
Cleaning is then required.
Warning!
Danger of eye injury !
Wear safety glasses where indicated!
• There is danger of eye injury from flying dirt particles.
Danger of cuts on fingers etc.
• Risk of injuries by cutting from contact with the sharp edge of the inner sealing band! Wear protective
gloves when handling the inner sealing band.
The piston must be freely movable by hand, all driven parts must be removed. Depending on the local condi-
tions it might become necessary to dismantle the complete cylinder.
Put on safety glasses
Check the position of the parts on the exploded view drawing on page 35.
• Reduce working pressure to 2 bar.
• Move piston to one end position, if necessary move by hand.
• Vent cylinder on the side where the piston is.
OSP-P Ø10:
• Loosen two screws (13) for outer sealing band (11).
OSP-P Ø16 to Ø80:
• Remove two clamp caps (12).
• Remove two screws (13) and clamping piece (14) for outer sealing band (11).
• Pressurise the opposite side to where
the piston not is
, to a maximum
pressure of 2 bar (keep other side being vented)
.
• Lift up one end of outer sealing band (11) without creasing it (see diagram)
NOTE
:
If the groove is not completely accessible for the cleaning tool because
of short strokes, you must:
- completely remove the cover (9) with wipers (8) and
- the cover band (11).
(See chap. „13.4 Dismantle OSPP-BG (Basic Guide)“ on page 19 )
• Insert appropriate blade of cleaning tool (100) into cylinder slot up to the
stop, the cylinder sizes are impressed in accordance with the diameter
(Ø 10 complies with Ø 16).
•
Carefully
draw cleaning tool along slot several times
the escaping
air blows out and dirt particles.
•
Second side
:
Remove pressure and push piston to other end position.
• Pressurise the opposite side to where
the piston not is
, to a maximum
pressure of 2 bar (vent other side).
• Repeat cleaning tool operation at other end of slot.
• Remove pressure and reassemble outer sealing band in reverse order.
cleaning tool
( )
Summary of Contents for OSP-P
Page 1: ...Modular Pneumatic Linear Drive System OSP P OSPP BG Operating Instructions ORIGA SYSTEM PLUS...
Page 35: ...35 EN 17 Spare Parts Lists 17 1 OSP P 10 17 2 OSP P 16 to 80 Item Number Item Number...
Page 36: ...36 Modular Pneumatic Linear Drive System OSP P OSPP BG 17 3 OSPP BG Item Number...