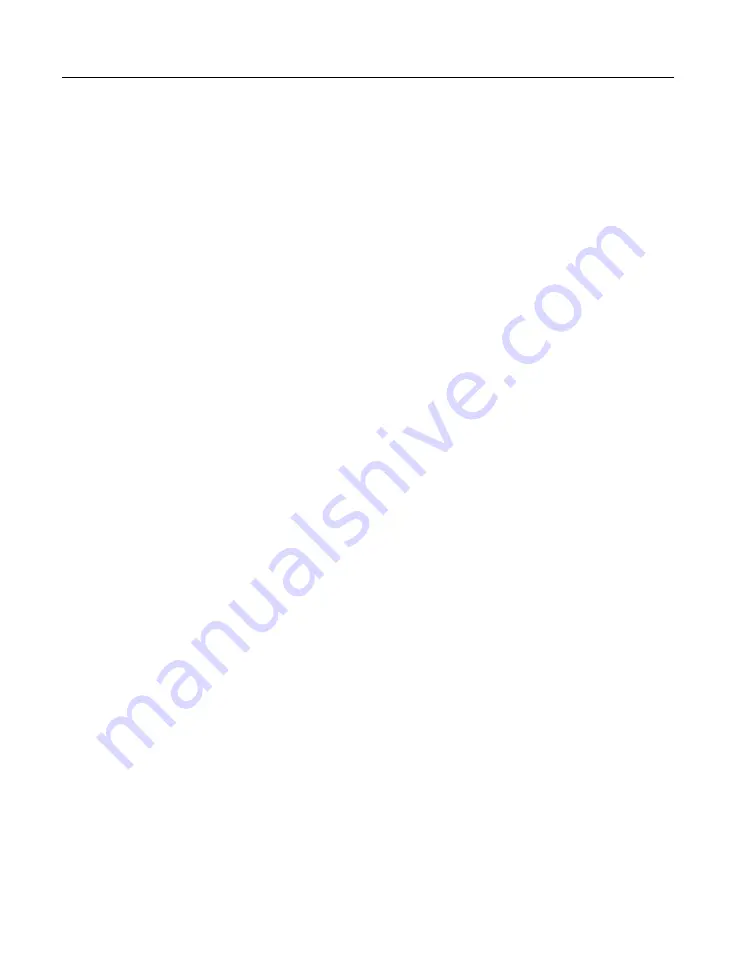
51
Max pressure of pressure sensor /system Max pressure
≥
1.4
d.
Oil pump is damaged and oil is not sufficient.
e.
Check servodrive standby current, which should be lower than 3A.
If current is too high, check motor and Resolver wiring, check commutation again.
3.
System pressure is not stable or can not reach Max pressure.
(1)
Pressure loop parameters are not suitable.
Unsuitable parameters cause unstable pressure.
Please set parameter referring to pressure control paramters.
(2)
Servo drive outputs max capacity, but system pressure is not enough.
Press “M” key to check motor current, if current is nearly or equal to F803*FA23, drive can not output
larger pressure. Study motor pole position again or adjust F817 to check whether drive output current is
reduced. If current can’t be reduced, motor load ability is insufficient, user can increase FA23 or change
motor.
(3)
Motor overheat or loss magnetism leads to insufficient output torque. User should change motor.
(4)
Oil pump is damaged or internal leakage is serious. User should replace oil pump. In normal state, oil
pump rocked-rotor speed for holding pressure is lower than 70rpm.
(5)
Feedback voltage of pressure sensor is too high. User should replace pressure sensor or adjust
FA18\FA19.
4.
Machine vibration
In oil pump system, servo motor is controlled first and then oil pump is controlled.
(1)
Adjust or reduce PI parameter of servo motor: F813, F814, F812, FA25/FA27, FA26/FA28.
(2)
Adjust or reduce PI parameters of oil pump.
(3)
Signal is disturbed. Connect motor and servo drive to ground, add ferrite core to drive input and output
cable, add filter, ferrite core and safety capacitor to signal or power supply, add ferrite core to analog
cable and feedback cable of pressure sensor.
(4)
Check whether Resolver cable is good.
(5)
Motor or motor cable has problem. Motor rotation is not stable.
(6)
Oil pump has problem. Large internal leakage or unstable pressure causes unstable pump.
5.
Sometimes system pressure keeps high and out of control.
(1)
Pressure sensor malfunction. AI2 can not detect feedback pressure.
(2)
Hydraulic oil has too many impurities. Pressure sensor filter is blocked
(3)
Feedback signal of pressure sensor is disturbed or lost temporarily.
6.
Injection terminal point is not stable
(1)
Lamination head, non-return valve, or lamination meson is worn or they are not combined well.
(2)
Injection technological parameter or mode is set wrong.
(3)
Pressure loop gain is not optimum.
(4)
Position detection device for molding machine is disturbed, for example, electronic ruler.
7.
Sometimes product has deficiency at startup.
(1)
Feed tube temperature is set so high that melt viscosity is low, fluidity is good, product easy to have
deficiency.
Molding machine pressure is set too high.
(2)
Pressure sensor is damaged.
8.
Plastic output is not sufficient. Raising injection pressure or speed is not effective.
(1)
During production process, because heat is taken by melt glue continually, melt glue is high viscosity ,
poor
flow, and insufficient. Raising feed tube temperature may slove the problem.
(2)
Back-pressure is not suitable.