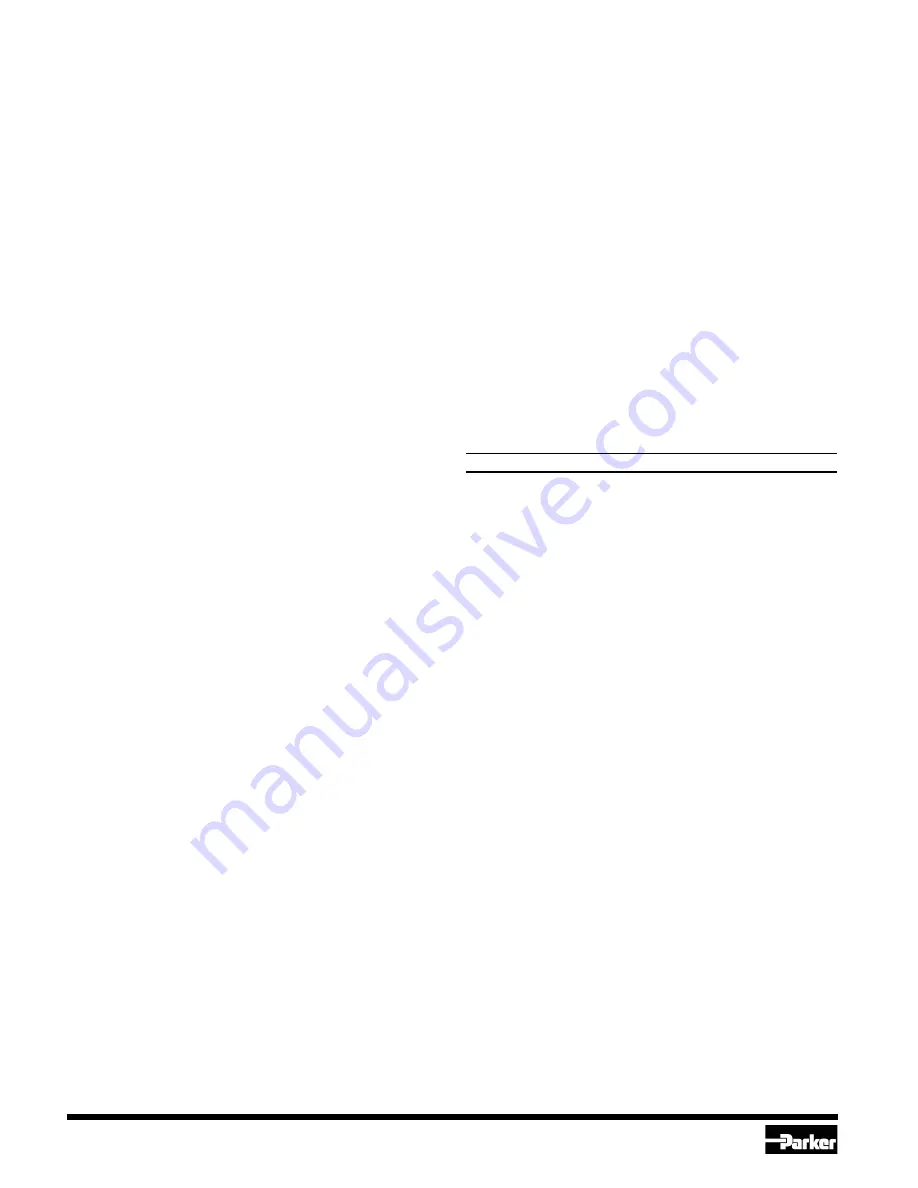
Refrigerating Specialties Division
2
refrigerant liquid pumps or compressors, and, as a warning device to
sound alarms or turn on lights when there is a danger of high or low
liquid level.
Principles of Operation
The Type ELL determines a discrete liquid level by measuring a
capacitance that varies with liquid level. The value of the capacitance
is proportional to the level of the liquid in terms of per cent of the
active probe length. This value of capacitance is conver ted
electronically to an electric signal which is used to operate a relay.
The Probe Assembly is inserted into a unique self-aligning steel Pipe
Column Fitting which is welded into either a 3" or a 4" Schedule 40
steel pipe. Another cap is available to fit either a 75 mm or 100 mm
metric tube. See Fig. 3.
The liquid level is shown on the face of the Controller by means of a
Digital/Bar Graph Display. (See Fig. 1) The Digital and Bar Graph
Display is calibrated from 0 to 100 per cent of the active probe length.
Level control or switch points can be changed in the field by a very
simple procedure which does not cause the controlled devices, such
as solenoids, to function during the adjustment period. See also
“Adjustment” section on page 5. Any of the Controllers can be used
with any of the Probe Assemblies.
All of the Controllers can accept either a 120/240 V 60 Hz or 110/220
V 50 Hz power supply. Power consumption is 10 VA. The relays have
10 amp contact ratings and are the plug-in type, single pole double
throw (SPDT) that can easily be replaced in the field.
There is an LED pilot light for each relay that is “On” whenever the
relay coil is energized. For an ELL-3, the condition of each relay relative
to liquid level is shown in the table below, which lists conditions when
the liquid level is BELOW the level for which the switch has been set:
RELAY (typical use)
RELAY IS:
LED IS:
R1 (Level Control)
Energized
On
R2 (Low Level Alarm)
Energized
On
R3 (High Level Alarm)
De-energized
Off
R4 (Low Level Shutdown)
Energized
On
R5 (High Level Shutdown)
De-energized
Off
It is helpful to refer to figure 4, TB2 when reviewing these five relay
positions. This figure illustrates the five relays in their de-energized
positions when a five relay unit is being analyzed.
One of the most important principles of operation concerning the Type
ELL, or ANY type of liquid level control, is that it is intended to sense
the level of a LIQUID, not the level of a mixture of bubbles in liquid.
Whether it be a varying capacitance or a floating ball that is measuring
the level of the liquid, it is difficult to sense the true level if the liquid is
bubbling. Heat will readily cause a volatile liquid, such as a refrigerant
to boil. Thus it is important to impede the transfer of heat to a cold
refrigerant whose level is being measured.
A cold liquid refrigerant contained in an uninsulated pipe column that
is located in a warm compressor room is a good example of an
improper installation. It is important to properly insulate the pipe column
and to use 4" (100 mm) pipe which will reduce the ratio of the pipe,
surface area to its internal volume. The larger the pipe size the smaller
will be this ratio and the less will be the tendency to boil refrigerant
inside the pipe. 4" (100 mm) pipe is the preferred size, but in many
cases (particularly where there is a relatively small temperature
difference between the liquid and the ambient space), a 3" (75 mm)
size should result in proper performance.
Installation
PIPE COLUMN: The Pipe Column should be installed as shown in
Fig. 2. The position and orientation of the column must be appropriate
to the specific application and installation criteria. The Pipe Column
must always be in a vertical position. In any case, it must be in a
serviceable location and out of the way of any possible damage by
material handling vehicles such as lift trucks.
It is important to have several sight glasses well spaced (See Table A)
along the height of the Pipe Column to determine the level of the
liquid when setting the ELL as well as to check its performance during
operation of the system. These are an essential part of any well
designed pressure vessel system and the use of an Electronic Liquid
Level Control does not eliminate this need. See also the section on
“Adjustment” on page 5.
TABLE A
Formula For Positioning Of Sight Glasses On ELL (Fig. 2B)
Notes:
1) “D” is the position of Sight Glass from top of standpipe cap.
2) In order to clear standpipe cap “D” must be 4" (100mm) minimum.
3) It is important when using the formula to make sure there is enough
space between Sight Glasses so that they clear each other.
4) P = Probe Length
5) L = Active Probe Length (Probe Length - 1" [25mm])
6) Y = Percentage of Active Probe Length measured from bottom of
probe.
D = L x (100% - Y) + 3/4" (20mm)
Example: If high level alarm is set at 75% and this is the position
where a Sight Glass is desired.
1) Determine your Probe Length P = 24"
2) Active Probe Length is L = 24" - 1“ = 23”
3) Position of Sight Glass from top of standpipe cap is:
D = 23" x (100% - 75%) + 3/4" = 6½"
(4” Column)
Probe Lengths “P”
Minimum Tube Lengths “M” *
Inches
cm
Inches
cm
24”
60.9 cm
26
3
/
8
”
67.0 cm
36”
91.4 cm
38
3
/
8
”
97.5 cm
48”
121 cm
50
3
/
8
”
128 cm
72”
182 cm
74
3
/
8
”
188 cm
96”
243 cm
98
3
/
8
”
250 cm
120”
304 cm
122
3
/
8
”
311 cm
* Subtract 3/4" (20mm) from “M” when 3" dia. column is used.
The probe is a PTFE encapsulated rigid steel rod which must not be
bent or bowed when installing. Thus it is important to consider the
headroom needed for installation (and possible removal) of the probe
when locating the pipe column, pressure vessel and determining how
the pipe column is to be connected to the vessel. The use of isolating
valves and flange unions in the top and bottom equalizing lines can
eliminate problems caused by a lack of head-room. See Fig. 2A.
The pipe connection at the top of the Pipe Column equalizing the
vapor spaces must be well above the highest switch point level on the
vessel upon which it is to be mounted. The piping for this line should
never be trapped, as any liquid in such a trap can cause the Pipe
Column to become vapor-bound.
The liquid equalizing line at the bottom of the Pipe Column must be
well below the lowest switch point level on the vessel on which it is to
be mounted. This line must be free draining and offer no obstruction
to a gravity flow of liquid. It should not be trapped, particularly on an
Ammonia system, as it would then become an ideal location for oil to
accumulate and could cause false levels in the Pipe Column. It is
recommended that a drain connection be installed at the low point in
the Pipe Column so that the Pipe Column can be drained when service
is required. (On an Ammonia system, this connection could be used
to drain oil.)
Both the vapor and the liquid equalizer lines should be as short as
possible.
An ELL can be added to an existing properly sized Pipe Column without
the need to remove any of the LL Float Switches being replaced. The
LL Switches could be used for an alternate purpose, such as an
independent or backup shut down means.
PROBE ASSEMBLY and PIPE COLUMN FITTING: See Fig. 3. The
Pipe Column Fitting is a unique design which is exclusive with the
Parker R/S Type ELL Liquid Controls. It is intended to slip inside the
(continued on page 5)