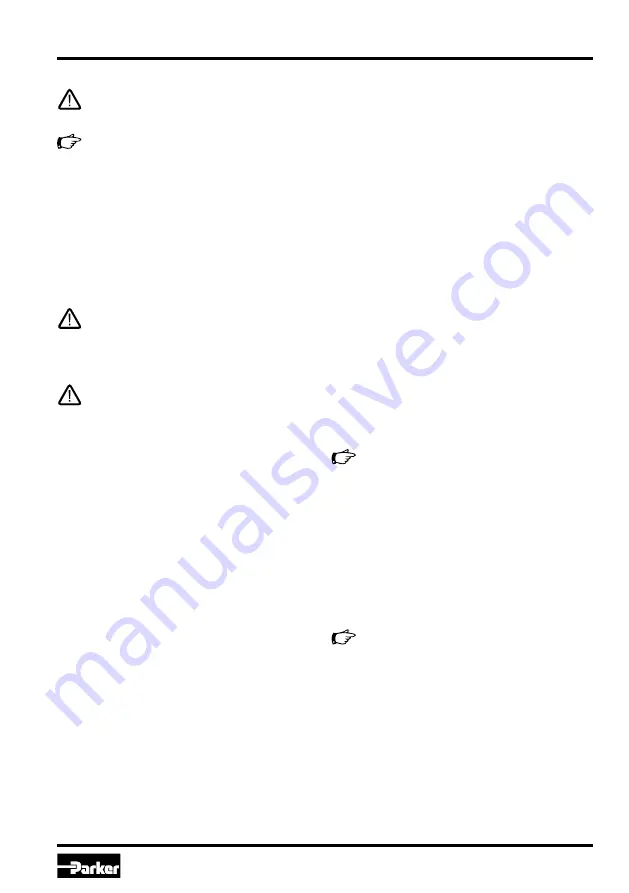
23
Parker Hannifin Corporation
Proportional DC Valves
Series D*FC, D*1FC
Operation Manual
D_FC 5715-686 UK 07.02.2019
Operation
If any of the safety features of the product are
not operational, the system/machine must be
shut down immediately.
Do not carry out any activities that might
jeopardize safety.
Note also the information in sections “Warranty and
liability”, “Use of operating instructions)”, “Compli-
ance with other rules and instructions”, “Personnel
requirements”, “Remaining risks”.
Modification
We define modification as the replacement of a
defective valve with a new valve of the same series.
In particular, it is not permitted to open the valve.
Make sure that the hydraulic system/machine
is unpressurised before the product is in-
stalled/removed.
Service/maintenance
Service work may only be carried out by
qualified personnel. Detailed knowledge of
the machine functions concerning switching
on and off as well as of the required safety
relevant technical tasks is required!
Periodical maintenance is essential for the longevity
of the system and guarantees reliability and avail-
ability. The following properties of the system has
to be checked in continuous short time intervals:
• oil level in the tank
• max. working temperature
• condition of the pressure fluid (visual inspection,
color and smell of hydraulic fluid)
• working pressure levels
• gas pre-load pressure on the pressure accu-
mulator
• leakage on all system components
• condition of filter elements
• condition of hose lines
• cleanliness of components
After a certain operating duration a change of the
hydraulic fluid is required. The frequency of change
depends from the following circumstances:
• kind resp. grade of the pressure fluid
• filtering
• operating temperature and environmental
conditions
Air bleeding of hydraulic system
During initial startup, after an oil change as well as
after the opening of lines or valves the hydraulic
system must be air bleeded.
Filter
The function and lifetime of the valve are strongly
affected by the cleanliness of the fluid.
Purity level class of 18/16/13 acc. ISO 4406 is
required.
Flushing
It is recommended to flush the pipelines by short
circuiting the pressure and return lines. This prevents
the installation dirt from entering the valve.
Decommissioning
Make sure that the hydraulic system/machine is
unpressurised before the product is removed. Note
also the information in sections “Warranty and
liability”, “Use of operating instructions”, “Compli-
ance with other rules and instructions”, “Personnel
requirements”, “Remaining risks”.
Disposal
At the end of the service life of this product
• all escaping pressure fluids must be removed
and disposed of properly
• any significant fluids remaining in the product
must be removed and disposed of properly
• all materials must be segregated for recycling
when they are removed and taken to a suitable
recycling center.
Please segregate the packaging material properly
(e.g. paper, plastic). None of the components of the
product contain hazardous materials.
The normal local environmental protection
laws must always be met when disposing the
product.
Note also the information in sections “Warranty and
liability”, “Basic information on using the manual”,
"Other applicable standards/rules", “Personnel
requirements”, “Remaining risks”.
Summary of Contents for D 1FC Series
Page 26: ......