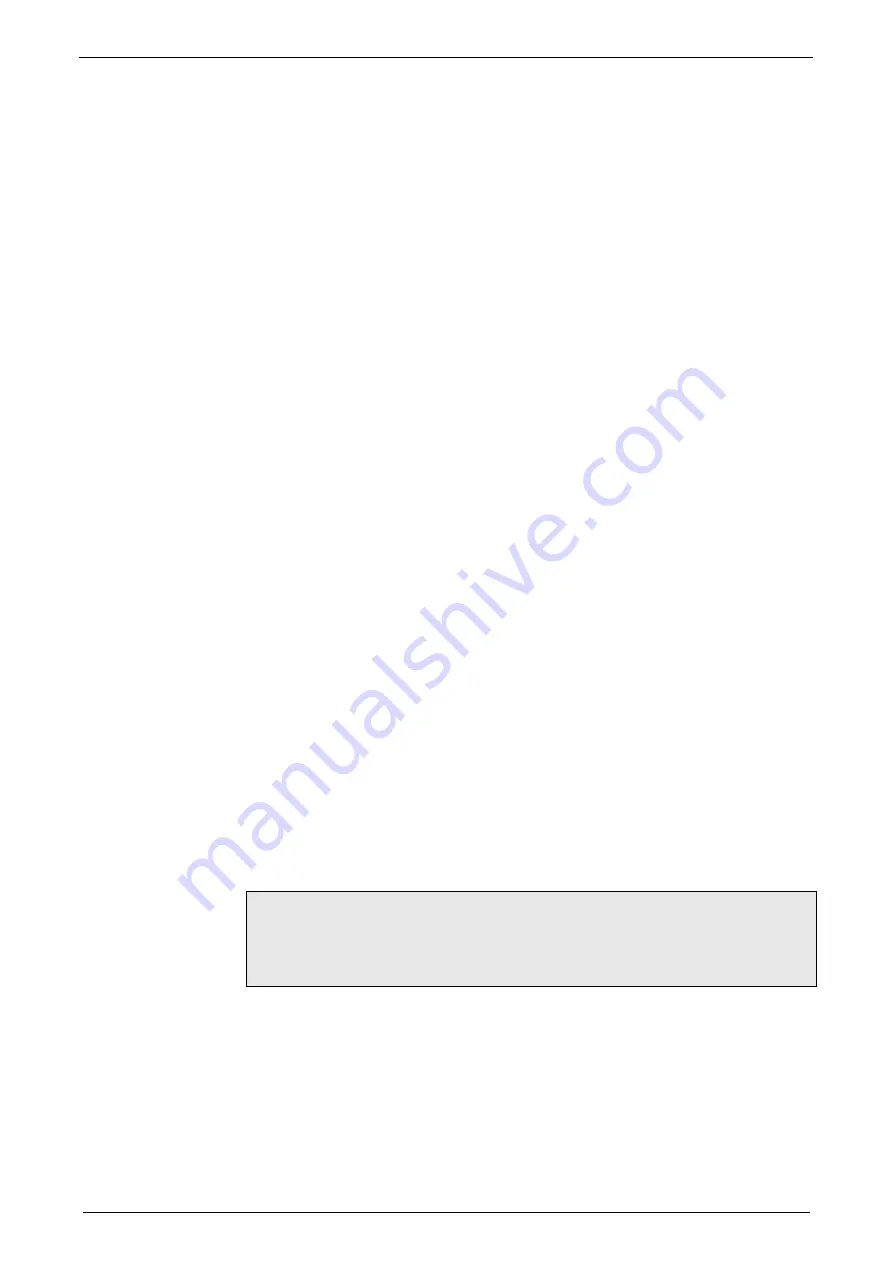
Parker EME
Setting up Compax3
192-120103 N13 C3I20T11 / C3I32T11 December 2010
157
4.3.1.
Configuration of load control
Configuration in the "configure signal source" wizard under "load
feedback system":
The selection of the feedback signal activates the acquisition and the signals are
available as
status values
(see on page 158).
Rotatory or linear feedback systems are supported.
Input values for rotatory feedback systems:
Increments per feedback revolution (physical, without quadruplication)
Direction reversal
Attention!
With wrong sense of direction and active load control, you will get a
positive feedback; the motor will accelerate in an uncontrolled way
Solution: Before the load control is activated, the signals must be checked with
the aid of the
status values
(see on page 158) and secured against wrong
sense of direction by configuring a "maximum difference to motor position”
(O410.6).
Load travel per feedback revolution: Is used for establishing the measure
reference between load- and motor position.
The value can be configured very precisely by entering numerator and
denominator.
Input values for linear feedback system
Feedback resolution (physical, without quadruplication)
Position difference, which corresponds to a cycle duration of the feedback
signal.
Direction reversal
Attention!
With wrong sense of direction and active load control, you will get a
positive feedback; the motor will accelerate in an uncontrolled way
Solution: Before the load control is activated, the signals must be checked with
the aid of the
status values
(see on page 158) and secured against wrong
sense of direction by configuring a "maximum difference to motor position”
(O410.6).
Scaling factor for an additional adaptation of the feedback signal (is normally
not required = 1)
Maximum difference tot he motor position
Upon exceeding this value, Compax3 will report
error 7385hex
(see on page
158) (29573dec)
Intervention limitation (=2201.13 in % of the reference velocity or reference
speed);
only active with position controller I component switched off (O2200.25=0)
You can use this specification in order to limit position correction intervention, i.e.
to limit the velocity correction factor resulting from the position difference. This
can be especially sensible during the acceleration phase, if the material slips
because of too high corrective velocities.
Activate / Deactivate load control
Attention!
The load control is immediately active after the configuration download!
Please do only activate after checking the load position signal (scaling,
direction, value).