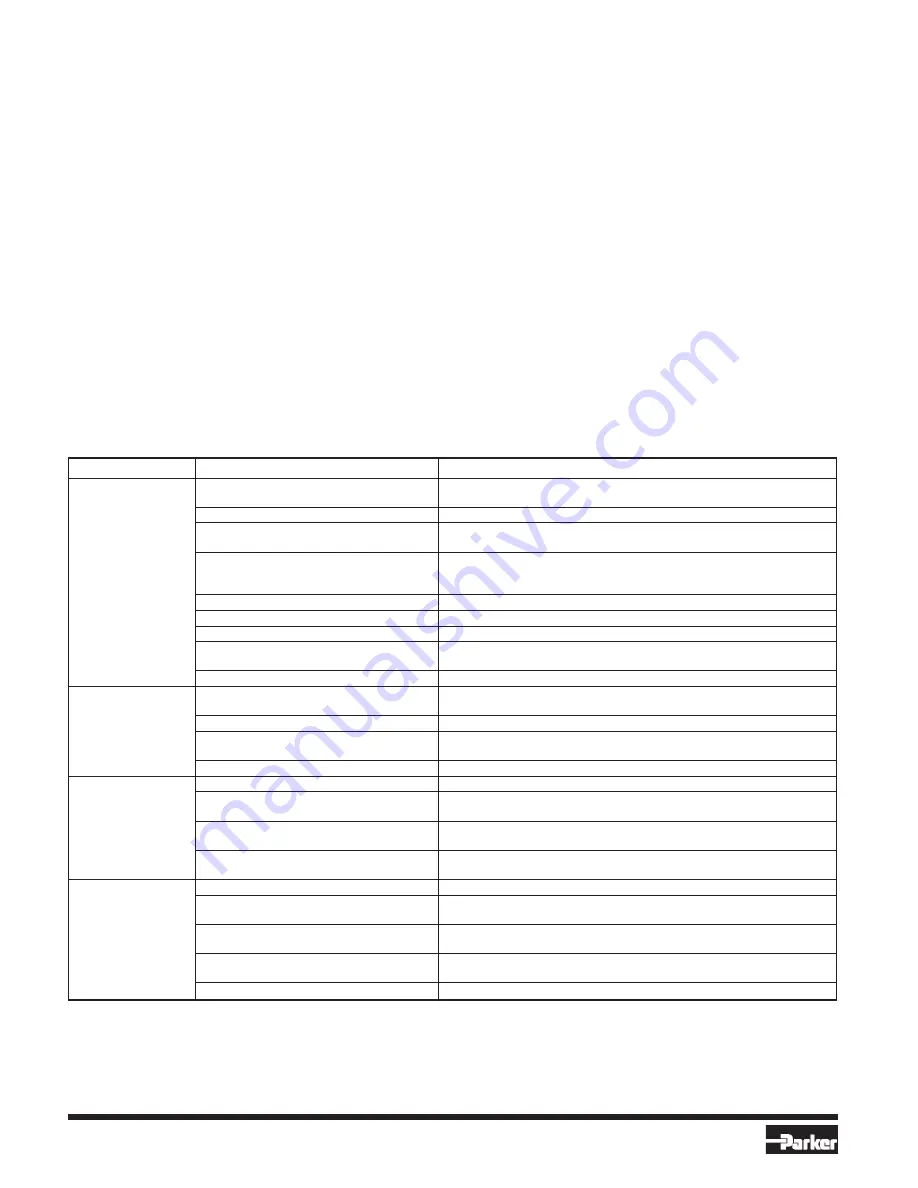
Refrigerating Specialties Division
8
Maintenance and Service (continued)
Electrical
The Refrigerating Specialties Division molded water resistant Class
“B” solenoid coil is designed for long life and powerful opening force.
The standard coil housing meets NEMA 3R and 4 requirements. This
sealed construction can withstand direct contact with moisture and
ice. The coil housing far exceeds the requirements of NEMA Standard
ICS, 1-110.57 salt spray test for rust resistance.
By definition, Class “B” coil construction will permit coil temperatures,
as measured by resistance method, as high as 130°C (266°F). Final
coil temperatures are a function of both fluid and ambient temperatures.
The higher fluid temperatures require lower ambient temperatures so
the maximum coil temperature is not exceeded. Conversely, low fluid
temperatures permit higher ambient temperatures.
The molded Class “B” coil is available from stock with most standard
voltages. However, coils are available for other voltages and
frequencies, as well as for direct current. Coils are also available as
transformer type with a 6 volt secondary winding for use with the
Refrigerating Specialties Division Pilot Light Assembly (see current
copy of Bulletin 60-10, “Pilot Light Assembly and Solenoid Transformer
Coil”).
The solenoid coil must be connected to electrical lines with volts and
Hertz same as stamped on coil. The supply circuits must be properly
sized to give adequate voltage at the coil leads even when other
electrical equipment is operating. The coil is designed to operate with
line voltage from 85% to 110% of rated coil voltage. Operating with a
line voltage above or below these limits may result in coil burnout.
Also, operating with line voltage below the limit will definitely result in
lowering the valve opening pressure differential. Power consumption
during normal operation will be 33 watts or less.
Inrush and running current is listed below:
Inrush Running Fuse
Standard Coil
Current Current Size
Vohs/Hertz
(Amps) (Amps) (Amps)
120/60 (Blue leads)
1.1860
0.46
1
208/60 (Blue & Red leads)
0.63
0.26
1
240/60 (Red leads)
0.60
0.23
1
440/60 (Yellow & Red leads)
0.39
0.13
1
115/50 (Yellow & Blue leads)
1.22
0.21
1
230/50 (Yellow leads)
0.65
0.26
1
Other
Contact Factory
On transformer coil the 6 volt leads are always black.
SYMPTOM
PROBABLE REASON
CORRECTION
Regulator does not
Diaphragm or seat dirty, damaged or frozen.
Clean or replace. Clean strainer.
shut off flow.
Diaphragm follower stuck or damged.
Clean or replace. Install follower carefully.
Piston jammed with excess dirt.
Remove and polish piston and bore with crocus cloth. Clean valve and
strainer.
Throttling plug leaking due to excess
Clean or replace. If used on liquid, check for
dirt or damage.
erosion due to excessive flash gas. Reduce flash gas by subcooling or by
reducing pressure drop across valve by providing restriction at valve outlet.
Diaphragm ruptured or badly deformed.
Replace. If Range “D” make sure has 2 diaphragms.
A4AB Modular Solenoid Pilot seat leaking.
Check seat and needle. Replace as needed,
A4AS Modular Solenoid Pilot seat leaking.
Check seat and needle. Replace as needed.
Diaphragm and seat eroded due to flash gas.
Replace. Reduce flash gas by subcooling or by reducing pressure drop
across regulator by providing restriction at valve outlet.
Modular Solenoid Pilot not closing.
Check power at leads, make sure coil is de-energized.
Regulator does not
A4A (inlet) Pressure Regulator Diaphragm
Replace. It Range D make sure has 2
open
ruptured or badly deformed.
diaphragms.
Diaphragm follower stuck, damaged or frozen.
Clean or replace. Install follower carefully.
A4AS/A4AB Modular Solenoid
Pressure drop across valve too high; over 21 bar (300 psig). Lower pressure
Pilot not opening.
drop. Improper power supply. Correct. Replace solenoid coil.
Piston worn, too much clearance.
Replace piston. Check for reason. If used on liquid, check for flash gas.
Regulator Operation
Diaphragm or seat dirty or damaged.
Clean or replace. Clean strainer.
erratic.
Diaphragm follower has dirt on the outside
Clean or replace.
diameter or outside diameter is damaged.
Other system components, line controllers,
Adjust, repair or replace.
thermostats, etc., erratic.
Regulator too far oversized.
Check load. Replace with smaller regulator or investigate use of reduced
capacity plug.
Pressure drop across
Inlet or outlet restricted.
Check for restriction. Clean strainer.
regulator too high.
Regulator too small.
Open manually to be sure valve is full open.
Replace with proper size regulator.
Large amount of flash gas in liquid line.
Reduce flash gas by subcooling. Reduce line restriction by increasing line
size, particularly at the regulator outlet. Replace with larger regulator.
High pressure drop causes high rate of
Increase pipe size at the outlet of the
expansion of gas at regulator outlet.
regulator.
Regulator does not open all the way.
Check piston for wear. Replace, it needed.
SERVICE POINTERS (Check General Procedure)