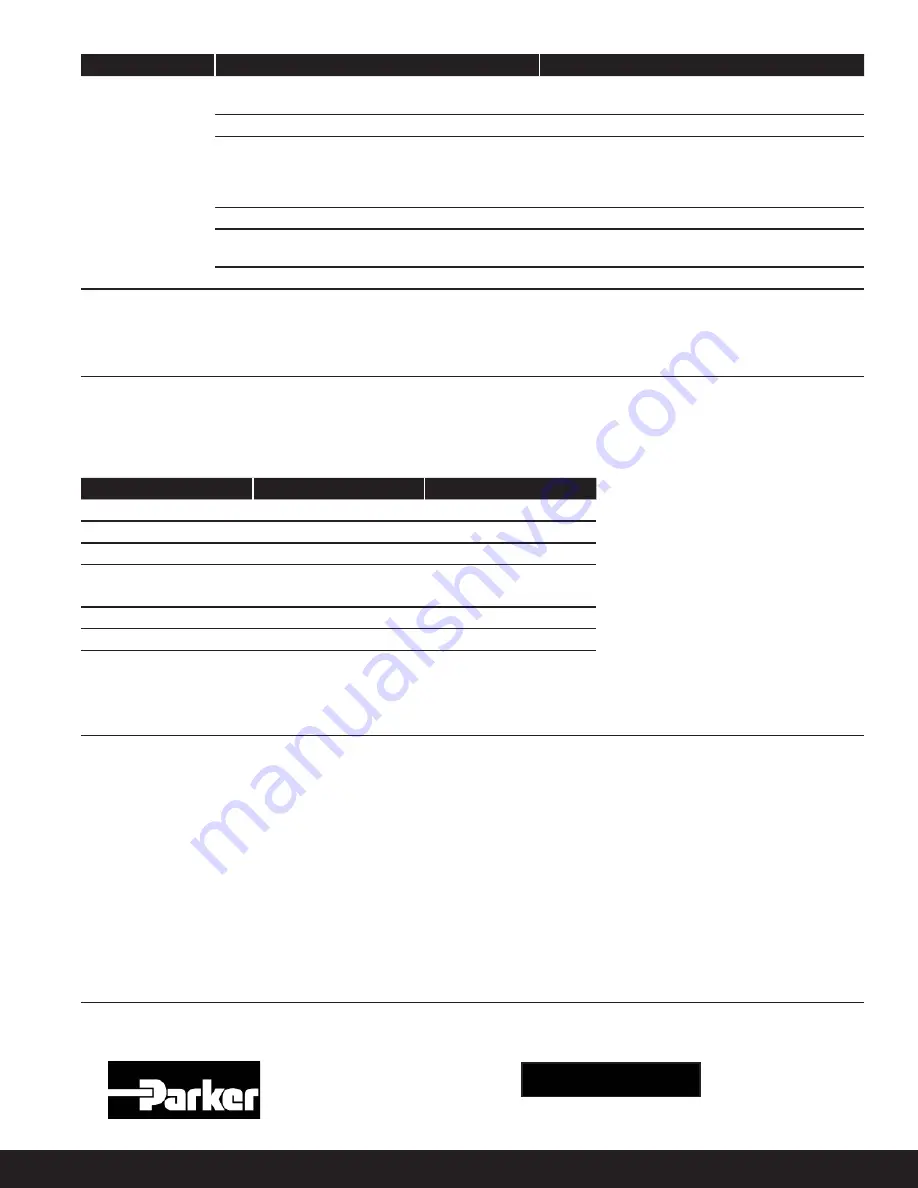
© 2008 Parker Hannifi n Corporation
ISO 9001 CERTIFIED
312069 ECN: 9078 06/11/09
Safe Operation (See Bulletin RSBCV)
People doing any work on a refrigeration system must be
qualifi ed and completely familiar with the system and the
Refrigerating Specialties Division valves involved, or all other
precautions will be meaningless. Th
is includes reading and
understanding pertinent Refrigerating Specialties Division
Product Bulletins and Safety Bulletin RSB prior to installation
or servicing work.
Where cold refrigerant liquid lines are used, it is necessary
that certain precautions be taken to avoid damage which
could result from liquid expansion. Temperature increase in a
piping section full of solid liquid will cause high pressure due
to the expanding liquid which can possibly rupture a gasket,
pipe or valve. All hand valves isolating such sections should
be marked, warning against accidental closing, and must
not be closed until the liquid is removed. Check valves must
never be installed upstream of solenoid valves, or regulators
with electric shut-off , nor should hand valves upstream of
solenoid valves or downstream of check valves be closed until
the liquid has been removed.
It is advisable to properly install relief devices in any section
where liquid expansion could take place. Avoid all piping
or control arrangements which might produce thermal or
pressure shock.
For the protection of people and products, all refrigerant
must be removed from the section to be worked on before a
valve, strainer, or other device is opened or removed. Flanges
with ODS connections are not suitable for ammonia service.
Warranty
All Refrigerating Specialties products are under warranty
against defects in workmanship and materials for a period of
one year from date of shipment from factory. This warranty
is in force only when products are properly installed, fi eld
assembled, maintained, and operated in use and service as
specifi cally stated in Refrigerating Specialties Catalogs or
Bulletins for normal refrigeration applications, unless other-
wise approved in writing by the Refrigerating Specialties
Division. Defective products, or parts thereof returned to the
factory with transportation charges prepaid and found to be
defective by factory inspection, will be replaced or repaired at
Refrigerating Specialties option, free of charge, F.O.B. factory.
Warranty does not cover products which have been altered,
or repaired in the fi eld, damaged in transit, or have suffered
accidents, misuse, or abuse. Products disabled by dirt or other
foreign substances will not be considered defective.
Th
e express warranty set forth above constitutes the only
warranty applicable to Refrigerating Specialties products, and
is in lieu of all other warranties, expressed or implied, written
including any warranty of merchantability, or fi tness for a
particular purpose.
In no event is Refrigerating Specialties
responsible for any consequential damages of any nature what-
soever. No employee, agent, dealer or other person is authorized
to give any warranties on behalf of Refrigerating Specialties, nor
to assume, for Refrigerating Specialties, any other liability in
connection with any of its products.
Symptom
Probable Cause
Correction
Failure to open,
close, or regulate
Piston jammed due to excessive dirt
Flush clearance space between piston and
cartridge bore with refrigeration oil solvent
Valve Manually Open
Close manual bypass stem by tuning clockwise
Adjusting stem improperly positioned:
a. Turned in too far. Does not open (inlet regulator)
b. Not turned far enough. Does not close (inlet
regulator). Does not open (outlet regulator)
Position adjusting stem properly
Passage “N” clogged
Clean passage “N”
Pilot seat dirty or eroded
Clean and smooth pilot seat. If diaphragm is
removed, replace with new gasket and O-Ring
Regulator installed backwards
Re-install regulator in proper position
System Control
cannot be
maintained -
unstable valve
operation
Improper regulator selection:
a. Actual load is mush lower than regulator capacity
b. Actual pressure drop across valve higher than
originally intended
c. Combination of a and b
Replace cartridge with one of suitable size
A4WO Service Pointers
Location
Description (SAE)
Torque mkg (Ft-Lbs)
Bonnet Screws
M6 x 18 MM
(7)
Port Plate Screws
M10 x 45 MM
(35)
Bonnet Seal Cap
—
Snug
Solenoid Pseudo
Assembly
—
Snug
Gages Port Plug
1/4” NPT
1.4 (10)
Pilot Plug
—
Snug
A4WO Torque Requirement Table