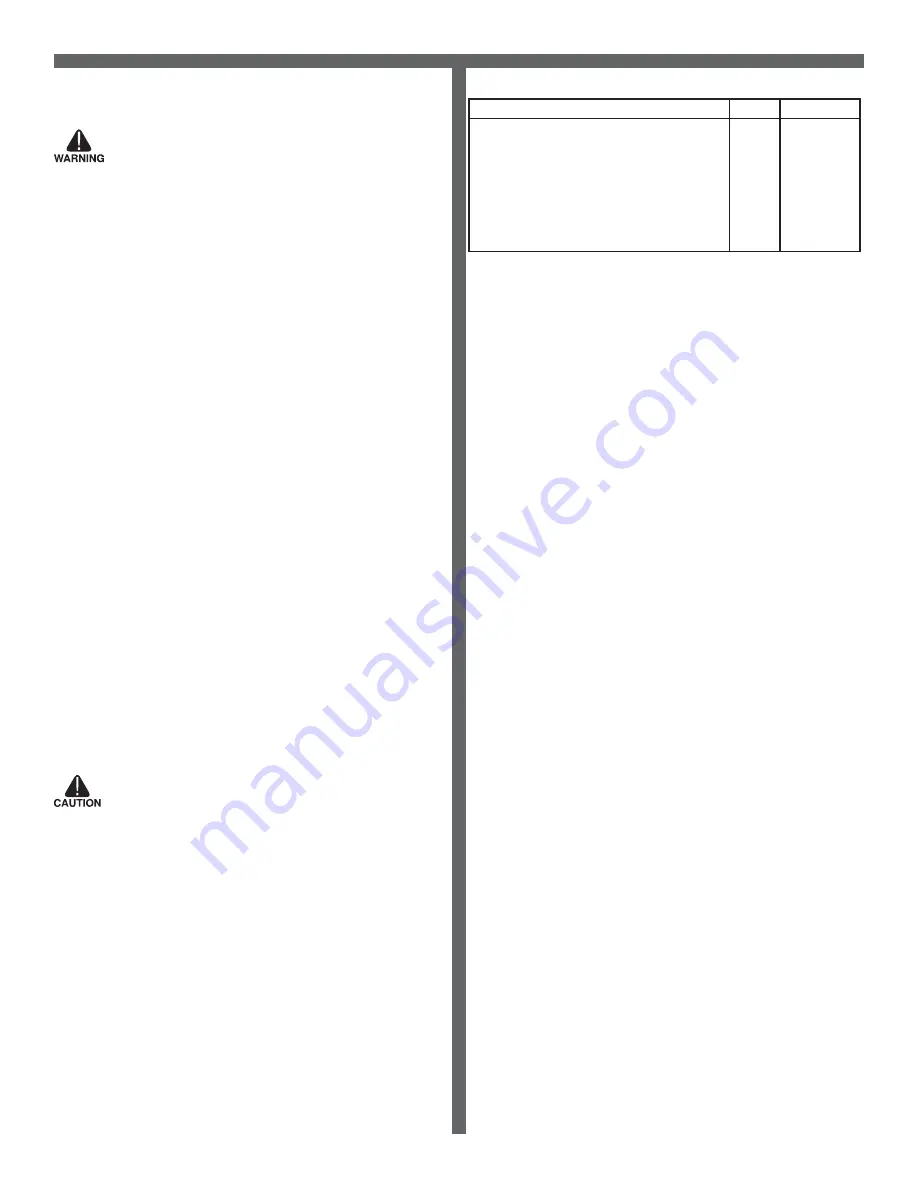
15
Setup
1. Open lid of solution tank. Fill solution with water or approved cleaning agent. For
best results, fill with warm water (140
o
).
Flammable materials can cause an explosion or fire. Do not use flammable solutions
or materials in tank(s).
FOR SAFETY: When using machine, follow mixing and handling instructions on
chemical containers.
ATTENTION: If using powdered cleaning chemicals, mix prior to adding.
2. Attach solution hose (located front of machine). NOTE: Make sure the quick
disconnect snap together firmly. As you do this, always inspect hoses for cracks or
fraying. Do not use if hoses are damaged.
3. Attach other end of solution hose to wand.
4. Attach vacuum hose to recovery tank.
5. Plug machine’s cord into a grounded wall outlet. FOR SAFETY: Do not operate
machine unless cord is properly grounded. FOR SAFETY: Do not operate machine
with the use of an extension cord.
6. Turn on pump. Key tool until you have a steady flow.
7. Release tool trigger. Turn on heater.
8. Wait 8–10 minutes for unit to pre-heat.
9. Re-key upholstery tool until hot water begins flowing.
10. Once hot water is flowing, release trigger and pre-heat an additional 4–5 minutes.
11. Turn on vacuum motor.
12. Begin cleaning. Make two dry passes to every wet pass.
13. For floor cleaning, unplug tool and attach floor wand.
14. Work away from cords to avoid damage.
15. Use a defoamer in your recovery tank.
16. To clean heavily soiled areas, repeat cleaning from different directions.
17. When float shuts off vacuum, empty tanks.
18. When work is complete, unplug cords and hoses.
19. Wrap and clean hoses. Clean all tanks.
Pre-Operation
1. Vacuum carpet and upholstery and remove other debris.
2. Perform machine setup procedures.
3. Inspect power cord for damage.
Operation
1. Turn pump switch on.
2. Pull up on tool lever to release air in the line. Hold lever until a steady flow of water
comes out of the wand.
3. Once pump is primed and there is pressure in the solution line, turn on heater switch
(if model is equipped with heater) and wait a few minutes for water to heat up.
4. Once water is heated, turn on vacuum and begin cleaning.
Note: When cleaning upholstery, always check manufacturer’s cleaning instructions.
1. Work away from outlet and power cord to prevent cord damage.
2. Use a recommended foam control solution in the recovery tank to prevent vacuum
motor damage. Periodically check for excessive foam buildup in solution tank, and
recovery tank.
3. To clean heavily soiled areas, repeat cleaning path from different direction.
4. When ball float shuts off vacuum, it is time to empty the dirty water from the
recovery tank, and refill solution tank.
5. After cleaning, relieve water pressure from tool before disconnecting hose.
Squeeze trigger for five seconds after turning main power switch off.
After Use
1. Unplug.
2. Empty solution tank and rinse it with clean water.
3. Inspect hoses and replace if damaged.
4. Inspect solution filter. Clean or replace if damaged.
5. Store the machine in a clean, dry place.
6. Open recovery tank cover to promote air circulation.
Maintenance Schedule
Maintenance item
Daily
Once a week
Clean and inspect Tanks
Clean and inspect Hoses
Check filters
Check power supply cable
Clean machine with all purpose cleaner and cloth
Check spray nozzles
Flush solution system with Mytee system maintainer
Remove and clean float shut-off screen from tank
Inspect vacuum hoses for holes and loose cuffs
x
x
x
x
x
x
x
x
x
Trouble Shooting
There is no power.
1. Plug machine in proper outlet.
2. Check circuit breaker; reset circuit breaker, other items should not run on the
same circuit as machine. Outlet must be a 20-amp circuit.
Pump does not work properly.
1. Snap quick disconnects firmly together.
2. Check solution tank; may be empty.
3. Jets clogged, remove jet and flush clean.
4. Filters clogged, remove filters and rinse clean with water.
5. Heater is blocked; flush out with Mytee’s system maintainer.
6. If brass check valve is stuck replace valve.
7. Check pump wire. May need to reconnect wire.
8. Switch plate switch may need to be replaced.
9. If pump motor brushes are worn, replace pump.
Heater does not work properly.
1. If sensor mounted on the heater has popped, reset sensor by pushing in button.
2. Heating element may need to be replaced.
Vacuum motor does not work properly.
1. Check that hose is tightly connected.
2. Close drain hose valve completely.
3. Secure the vacuum tank tightly.
4. If ball float is shut off, empty vacuum tank of all wastewater.
5. Make sure ball float is firmly installed on the elbow.
6. If water is coming out of vacuum motor, use a low foaming detergent.
7. Clean upholstery tool or floor wand jets.
FAQs
Q: How much does the Contractor’s Special™ weigh and what are the shipping
dimensions?
2000CS
A: 79 Pounds - Box dimensions are 29 3/4” x 19” x 46 1/4”. Must ship motor freight.
2001CS
A: 85 Pounds - Box dimensions are 29 3/4” x 19” x 46 1/4”. Must ship motor freight.
Q: What comes standard with the Contractor’s Special™?
A: The Contractor’s Special™ comes with 15’ 1-1/4” Vacuum/Solution Hose and a
12” wand and Cuff-Lynx™ reducer.
Q: Where do I plug the machine in?
A: The Contractor’s Special™ requires a 20A grounded circuit. Please note: GFI
outlets may trip before the breaker setting.
Q: What is the proper pre heat cycle for the 2001CS?
A: Turn pump switch to the on position and prime pump through the solution hose
and the tool. Then turn the heater switch to the on position. Let the machine sit idle
for 8-10 minutes. Spray tool until you feel the hot water from the jet. Let machine sit
idle for an additional 3-5 minutes. This will insure the water in the heater and hoses
will be at the hottest point to start cleaning.
Q: Are the pumps re-buildable for the Contractor’s Special™?
A: Yes, both the seals and the pistons have repair kits available.
Please see the pump manual that shipped with your machine for the
maintenance schedule.
Q: Is there anything I can do to increase the expected life of my machine?
A: Running the vacuum motors with the tank empty and lid off will allow excess
moisture in the vacs to dry off. You should also run a System Maintainer through
the system to keep the hoses, pump, and heater clean and free of debris.