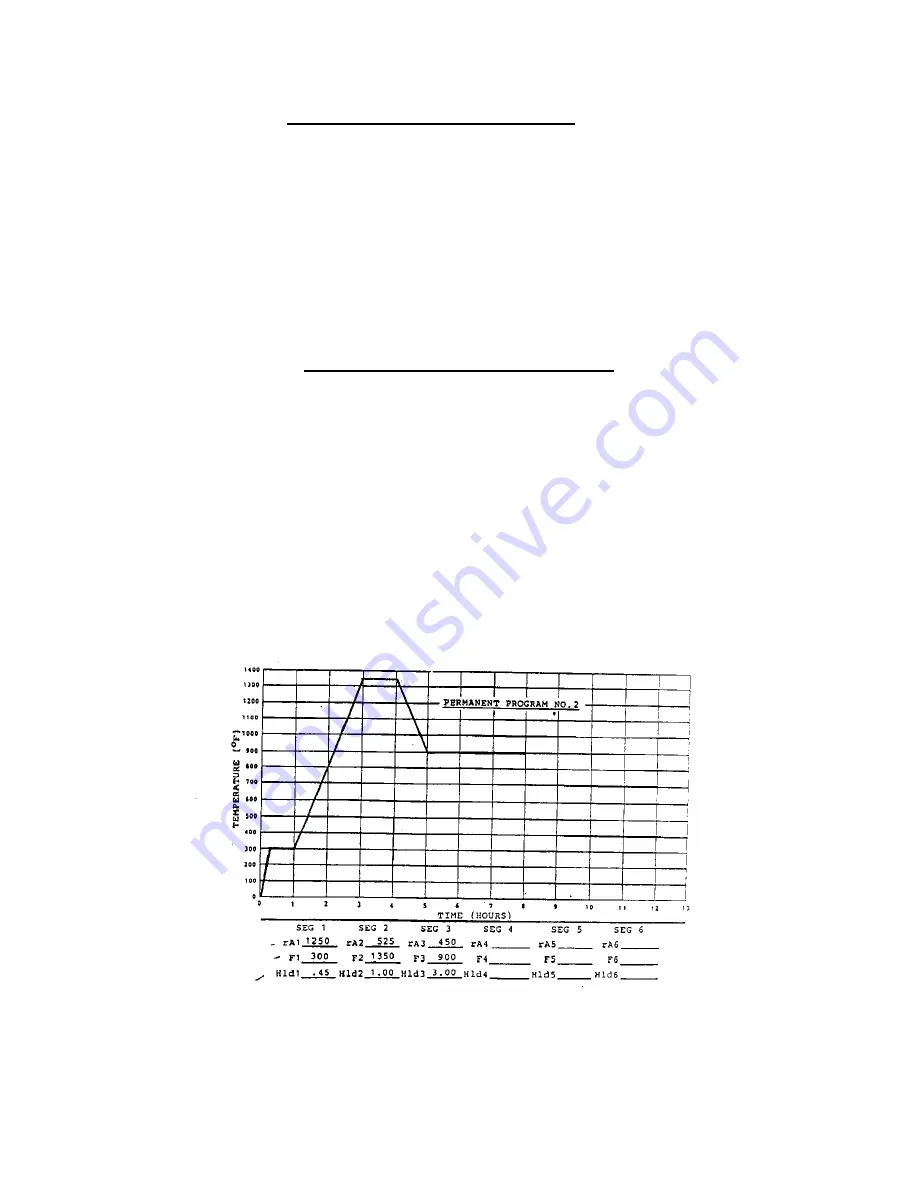
12
PERMANENT PROGRAM NO. 2 [ 5Hr]
This program operates the furnace for 1 hour at 300
°°°°
F (150
°°°°
C) and then advances slowly
to 1350
°°°°
F (730
°°°°
C) over a period of approximately 2 hours, then holds that temperature for 1 hour.
The programmer then lowers the temperature to 900
°°°°
F (480
°°°°
C) in a period of 1 hour and holds
that temperature for 3 hours. NOTE: AT THE END OF THE 5 HOUR PROGRAM, WE HAVE BUILT IN
3 EXTRA HOURS OF HOLD TIME IN CASE THE OPERATOR IS NOT READY TO CAST
IMMEDIATELY.
Once casting is completed, press “STOP” ( # ). Otherwise, the furnace will continue to
operate at 900
°°°°
F until 8 hours has passed and then shut off automatically. The display will show [
CPLt ].
FLASK TEMPERATURE FOR CASTING
We have used 900
°°°°
F (480
°°°°
C) as casting temperature for the flask. This temperature is
suitable for most castings, however many casters prefer other temperatures. This setting is
governed by experience. You may use any casting temperature you wish by entering your own
custom program.
ENTER PROGRAM NO. 2 [ 5 Hr ] AS FOLLOWS:
ACTION
DISPLAY
1) Apply Power
[ ldLE ] alternating with current furnace temperature
2) Press “1”
[PROG] alternating with [EL}
3) Press “2”
[5 HR]
4) Press “ENTER”
[ ldLE ] alternating with current furnace temperature. Program saved.
5) Press “ENTER”
[STRT] The furnace starts firing cycle.