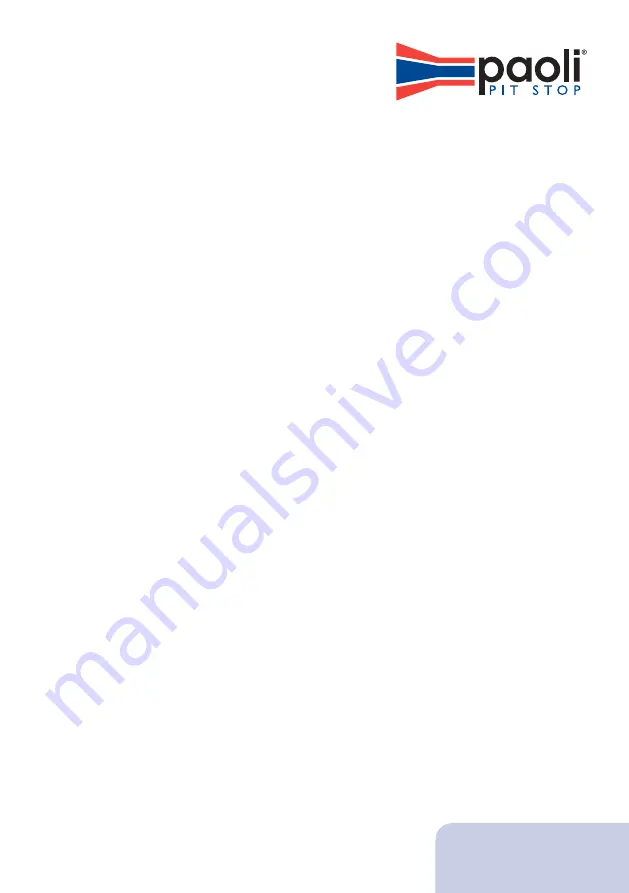
ENGLISH
7
L
When the cross holes on the socket
and square drive near alignment, install
socket pin in socket. While applying side
pressure to the pin continue to press
the socket onto the square drive. When
the holes are aligned the pin will slide
through easily.
L
Socket pins can be staked in one of two
ways.
⚪
One is to use two 45 deg. center
punches. Place one punch point up in
vice jaws and clamp down. With the help
of an assistant, position the socket pin
in the center of the socket, place socket
and pin on punch point in vice. Using
a second punch and hammer strike the
top of the socket pin. This action should
be enough to stake both the top and the
bottom of the pin, repeat operation if
necessary.
⚪
The second method of staking socket pins
is the use of a staking tool. A staking tool
can easily be produced by incorporating
a fixed bottom stake point, a square or
“U” shaped yoke and a sliding top stake
point or punch. This tool can be used
with either a hammer or a press.
L
After the socket pin has been staked, any
part of the pin protruding out of the socket
will need to be ground flush. This can be
done with a right angle die grinder and a
medium Scotch-Brite wheel. Avoid grinding
any titanium surfaces of the socket. Pay
close attention not to leave any rough or
high points that may cause hand injury
during use.
L
Apply some of the metal strip on the outside
diameter of the socket to coincide with the
locking pin to prevent any unexpected
slippage of the pin.
L
Match coordinating clutch cover assemblies
and guns. Re-install the socket and clutch
cover assembly on wheel gun using the four
screws and new lock washers.
L
In ideal situations, an aluminum block should
be machined to fit either the I.D. or the surface
of the socket. This will be used for pressing the
socket onto the square drive. Special attention
must be taken to assure the inner O-ring
groove (retention ring) is not damaged by a
tool used on the socket I.D.. A tool used on the
magnet surface (i.e. for wheel nut sockets with
magnets) should also fit properly to prevent
damage to the magnets. In certain situations a
thick block of aluminum can be used to press
directly on the teeth of the socket (i.e. for
wheel nut sockets with fingers) for installation.
This is not a recommended practice and
should only be used when a proper press tool
cannot readily be made.
L
The sockets are designed to have a press fit
on the 1” square drive. Sockets and 1” square
drives should never be modified to allow a
hand press fit or a slip on installation. Older
sockets that slide freely on square drives
should be replaced.
L
IMPORTANT: If there are magnetic parts and
rubber in the socket under no circumstances
should it be heated to assist the installation
onto the square drive. Heating the socket
will compromise the magnet’s holding power
and destroys the epoxy bold that holds the
magnets in the socket.
L
Place anvil shank, clutch cover bearing and
clutch cover on lower aluminum support block.
Lubricate the square drive and internal square on
socket with appropriate press fit lubricant. Most
anti-seize, anti-galling compounds will work.
L
Place the anvil shank along with the clutch
cover assembly and support block in a press,
adjust height accordingly.
L
Align the cross holes for the socket pin on
both the socket and square drive. Insert top
press block in or on socket. Making sure the
stacked assembly is square; begin pressing
the assembly together using low pressure.
As the socket is being installed it may be
necessary to go to the high pressure setting
on your hydraulic press.
OPERATING AND MAINTENANCE MANUAL