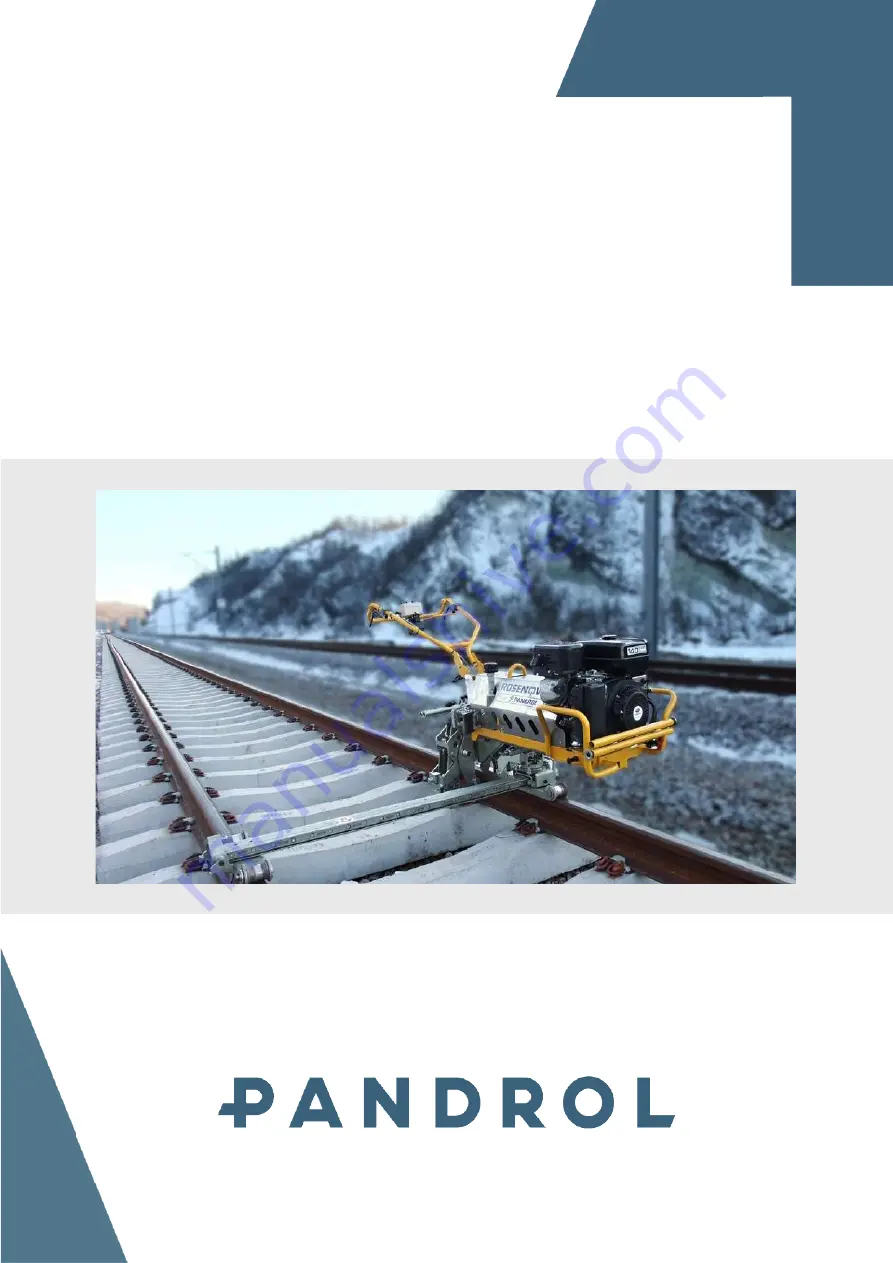
Operation &
Maintenance Manual
Rosenqvist CD200
Issue date:2016-11-11
Dokument ID:ENG_OMM_CD200
Revision:P05
Original instructions
Pandrol AB, Hyggesvägen 4, 824 34 Hudiksvall, Sweden
Phone +46 650-16505, www.rosenqvistrail.com, [email protected]