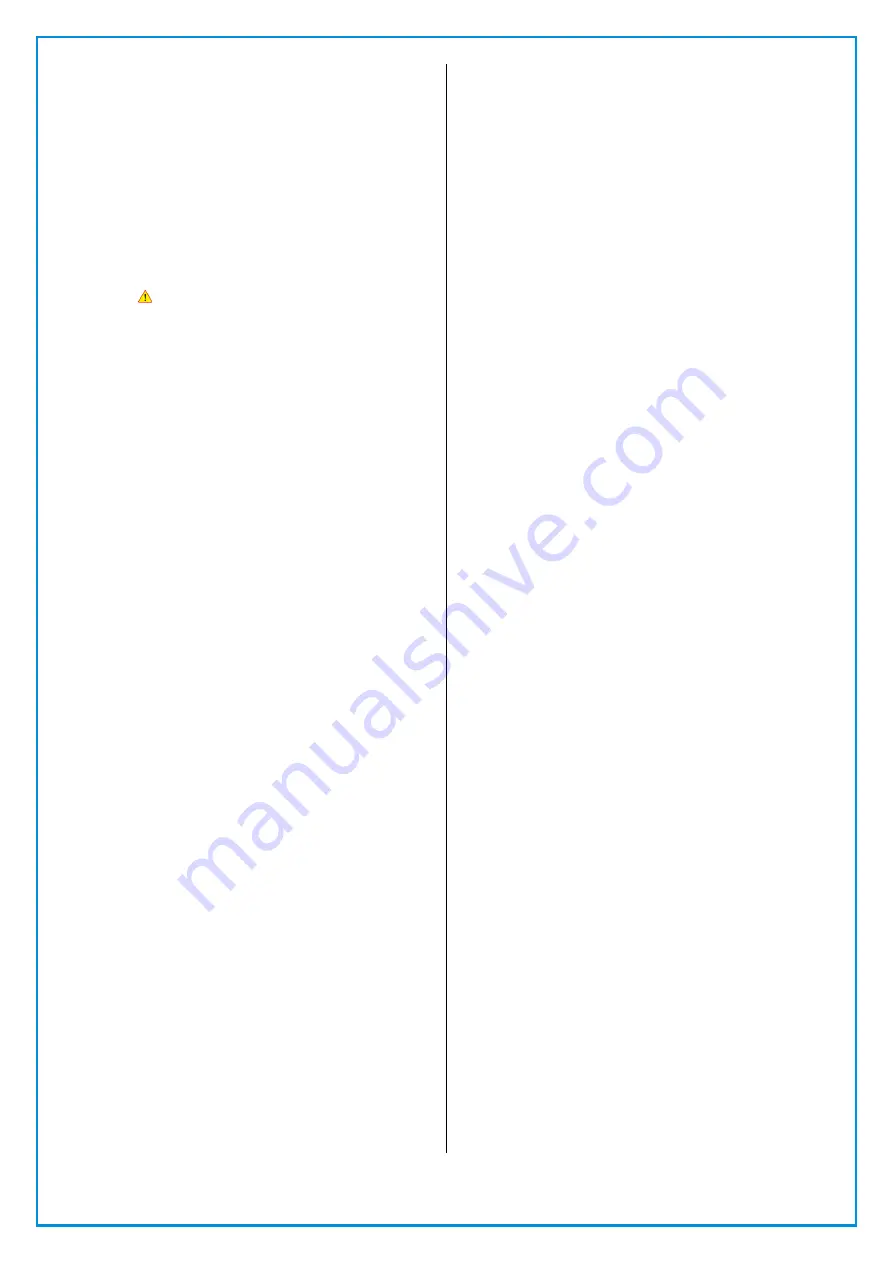
- 3 -
ZVP-PC-0227-00-R0
4.1
On a daily basis
4.1.1
All piping, fittings and hoses must be checked
daily for tightness and leakage.
4.1.2
All equipment and components must be
thoroughly checked for wear.
4.1.3
All worn or suspect parts must be replaced
4.1.4
The cabinet’s viewing window becomes frosted
from the impact of rebounding abrasive media;
replace the window by unscrewing the four
retaining nuts and removing the cabinet widow
frame.
! WARNING ! - THE CABINET VIEWING
WINDOW IS MADE FROM 6MM THICK
LAMINATED GLASS. NEVER USE PLAIN PLATE
GLASS FOR A CABINET WINDOW, AS SERIOUS
INJURY MAY OCCUR.
NOTE: THE SERVICE LIFE OF THE WINDOW
WILL BE INCREASED BY ENSURING THAT THE
OPERATOR ALWAYS DIRECTS THE BLASTING
ACTION AWAY FROM THE WINDOW AS MUCH
AS POSSIBLE OR BY USING WINDOW COVER
BAC-CA-PB-0392
4.1.5
If moisture separator is fitted, clean filter daily &
drain away excess water.
4.1.6
Use abrasive that is properly sized and free of
harmful substances such as free silica, cyanide,
arsenic or lead. Check for presence of toxic or
harmful substances
4.2
On a weekly basis
Blasting Nozzle
4.2.1
On a weekly basis, remove the blast nozzle from
the nozzle holder by unscrewing the nozzle in a
counter-clockwise direction, and inspect it for
wear. Replace the nozzle if the internal diameter
is worn by 1.5mm (1/16") from its original size,
or if the liner is chipped or cracked.
4.2.2
Check the condition of the nozzle washer and
replace as required, then re-fit/replace the blast
nozzle by screwing it clockwise into the nozzle
holder until it is fully sealed against the nozzle
washer.
4.2.3
Check the condition of the nozzle holder, and
inspect for any cracks or signs of damage.
Replace if required.
Dust Collector
4.2.4
On a weekly basis, or when the visibility within
the cabinet becomes poor, with the dust
collector fan turned off, operate the dust
collector pulse system 2-3 times by depressing
then releasing the valve lever located on the
side of the dust collector behind the main
cabinet. Wait a few moments for the dust to
settle, then open the drain valve on the bottom
of the dust collector and drain the dust into a
refuse dustbin. When all the dust has completely
drained out, close the drain valve. Do not over
pulse the dust collector cart, as this will cause
damage to the filter cartridge media, and this in
turn will cause the dust collector to leak dust
from the fan outlet.
4.2.5
Open the dust collector inspection door, and
visually inspect the filter cartridge for any
damage, wear or excessive dust build up. If the
filter media is damaged in any way, or there is
dust present in the air being discharged from
the dust collector, then the filter cartridge
should be replaced.
4.2.6
As the abrasive is used, dust and debris may
build up in the abrasive mix. This will reduce
the performance of the blast gun, increase wear
on the gun parts and hoses, and also reduce
visibility within the cabinet area. If cabinet
visibility does not improve after carrying
maintenance as detailed in 4.2.4 and 4.2.5, then
it will be necessary to drain all the abrasive from
the cabinet, and replace it with new, clean
abrasive media.
Cabinet Gloves
4.2.7
On a weekly basis, give the cabinet gloves a
visual inspection and check for holes and signs
of deterioration. Replace the gloves as
necessary.
Rubber Seals
4.2.8
On a weekly basis, inspect the main cabinet
door seal around the door opening for wear and
damage. Also inspect the abrasive hopper seal
and the dust collector inspection door seal for
wear and damage. Replace all seals as required.
Door Safety Interlock
4.2.9
On a weekly basis, inspect the cabinet door
safety interlock for condition and operation. The
blasting system should not operate with the
main cabinet door open. Replace/adjust the
door interlock as required.
NOTE: NEVER BYPASS OR DISABLE THE DOOR
INTERLOCK AS SERIOUS INJURY MAY OCCUR.
4.3
On a monthly basis
Abrasives Delivery Hose
4.3.1
On a monthly basis, inspect the abrasive supply
hose along its entire length, by feeling for soft
spots which will indicate areas of wear. If the
wear is near the end of the hose, it is
permissible to cut off the worn section of hose
and re-connect the shortened hose. Otherwise it
will be necessary to replace the entire length of
hose.
Blast Pot
4.3.2
On a monthly basis, inspect the pop up valve
located in the top of the blast pot for wear in
the form of cracks or grooves. If replacement is
required, remove the blast pot shell inspection
cover located on the front of the blast pot.
Using a suitable pipe wrench, unscrew the
vertical pipe section which houses the pop up
valve, and remove both the pipe section and
pop up valve through the inspection opening.
Installation of the new pop up valve is a reversal
of the removal procedure and ensures that the
pop up valve is positioned directly below the top
opening of the blast pot for correct sealing.
4.3.3
Check and inspect the pop up valve seating ring
for wear. If replacement is necessary, use a
large screwdriver or similar tool to pry the