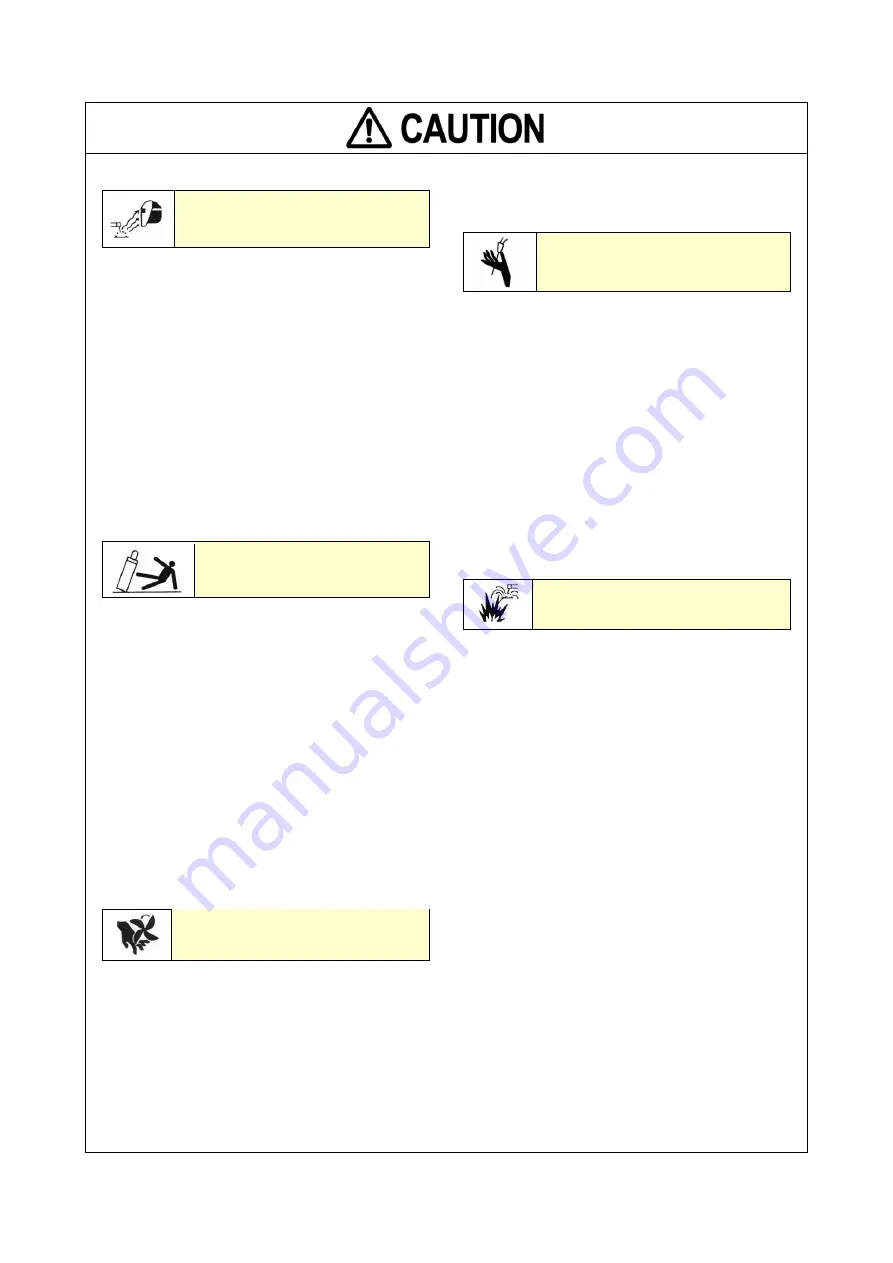
III
Installing shielding (curtain etc.)
Arc flash, flying spatter, slugs, and
noise generated during welding can
damage your eyes, skin and hearing.
(1)Install a protective curtain around the welding
manipulator site to prevent the arc flash from
entering the eyes of people in the surrounding area.
(2)When welding or monitoring welding, wear safety
glasses with sufficient light blocking structure or
use a protective mask designed for welding
operation.
(3)When welding or monitoring welding wear protective
clothing designed for welding operation, such as
leather gloves, leg cover and leather apron, and also
wear long-sleeve shirts.
(4)Be sure to wear noise-proof protective equipment if
the noise level is high.
(5)The larger the welding current is, or in case of AC
TIG or MIXTIG welding, the larger the AC frequency
is, the larger the arc sound becomes.
Gas cylinder and gas flow regulator
Overturn of gas cylinder and
blowout of gas flow regulator can
cause injury.
(1)The gas cylinder must be handled properly according
to the applicable law and in-house standards.
(2)Use the gas flow regulator that is supplied or recom-
mended by our company.
(3)Read the instruction manual of the gas regulator prior
to using it, and observe the cautions in the manual.
(4)Secure the gas cylinder to a dedicated gas cylinder
stand.
(5)Do not expose the gas cylinder to high temperature.
(6)When opening the valve of the gas cylinder, do not
bring your face close to the discharge outlet.
(7)When the gas cylinder is not used, be sure to install a
protective cap.
(8)Do not hang the welding torch on the gas cylinder, or
touch the gas cylinder with the electrode.
(9)Do not attempt to disassemble or repair the gas
regulator. Such works require special knowledge.
Rotating parts
Rotating parts can cause injury.
(1)Keep away from rotating parts such as cooling fans
,
and feed roller of the wire feeder, or hand, finger(s)
,
hair or part of your clothes may be caught by the
parts resulting in injury.
(2)Keep all covers, panels and cases closed when
using the product.
(3)Maintenance work and repair should be perform only
by educated and/or skilled persons who thoroughly
understand welding machines. While
performing maintenance work or repair work, provide
fence or the like around the welding machine so that
unauthorized person can not come close carelessly.
Welding wire
Welding wire, especially wire tip part
can cause injury.
(1)Do not perform inching operation or pull the torch
switch with your eyes, face or body close to the end
of the welding torch - wire extends out from the end
of the welding torch and may stick into the eye,
face or body.
(2)In case of using a torch cable with the resin liner,
straighten the torch cable and reduce the preset feed
amount (current) to a half or less before applying
the wire inching.
(3)Performing wire inching while torch cable has been
bent extremely can cause the wire to pierce the
resin liner and cable. Make sure to replace any
damaged liner or cable with a new one, or damaged
liner/wire can cause gas leak or dielectric
degradation.
. Against insulation deterioration
Insulation deterioration can cause fire
of welding power source.
(1)Keep enough distance from welding power source
when performing welding or grinding work so as to
prevent spatters or iron particles from getting
into the power source.
(2)Perform check and maintenance work periodically
so as to prevent insulation deterioration due to
accumulated dust or dirt.
(3)When spatters or iron particles get into the welding
power source, turn off the power switches of the
welding power source and power distribution box,
and then blow out.
(4)Make sure to replace any damaged liner or cable
with a new one as use of damaged liner/cable may
cause gas leak or dielectric degradation.
(5)In order to avoid dust and dirt to be collected inside
of the power source, make sure not to leave the
panel and bolts (including eyebolts) open and
removed.
Summary of Contents for YC-300WY
Page 8: ...YC 500WY4 YC 500WX4 415 ...
Page 10: ... 2 2 ...
Page 12: ......
Page 13: ......
Page 14: ......
Page 15: ......
Page 16: ......
Page 17: ......
Page 18: ......
Page 19: ......
Page 20: ......
Page 21: ......
Page 22: ......
Page 23: ......
Page 24: ......
Page 25: ......
Page 26: ......
Page 27: ......
Page 28: ......
Page 30: ......
Page 31: ......
Page 33: ......
Page 34: ......
Page 35: ...CIRCUIT DIAGRAM YC 500WY4 WX4HJE 27 R100 ...
Page 36: ... 8 ...
Page 40: ...YC 300WY4HGE 4 42 44 37 45 49 45 34 46 40 56 58 57 55 32 22 13 12 8 25 20 3 50 41 19 59 7 21 ...
Page 41: ...YC 500WY ...
Page 42: ...YC 300WY4HGE ...
Page 43: ......
Page 44: ......
Page 45: ......