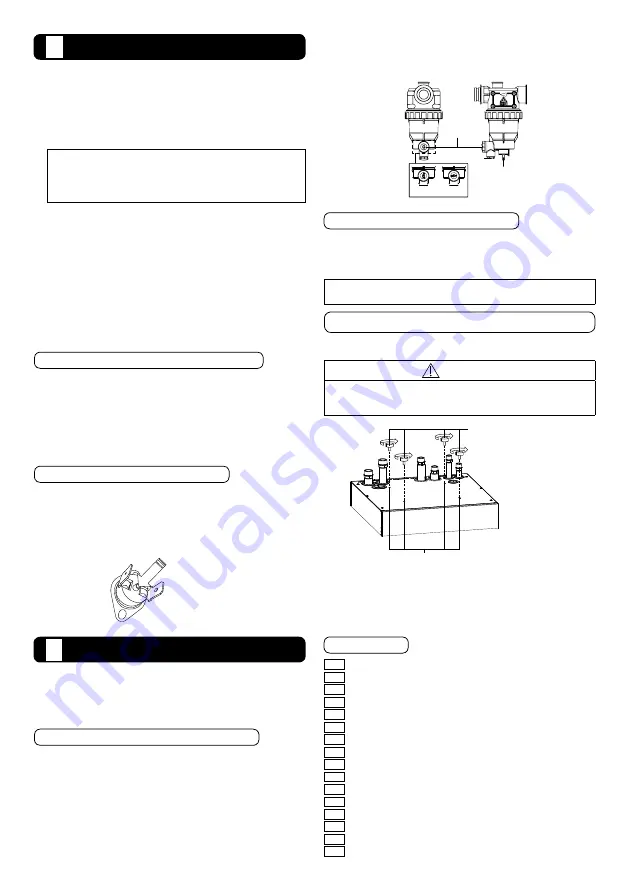
10
1. Before test run, make sure below items have been checked:-
a) Pipework are properly done.
b) Electric cable connecting work are properly done.
c) Tank Unit is fi lled up with water and trapped air is released.
d) Please turn on the power supply after fi lling the tank until full.
2. Switch ON the power supply of the Tank Unit. Set the Tank
Unit RCCB /ELCB to “ON” condition. Then, please refer to the
Operation Instruction for operation of Remote Controller
1
.
Note:
•
During winter, turn on the power supply and standby the unit for at
least 15 minutes before test run.
Allow suffi cient time to warm up refrigerant and prevent wrong error
code judgement.
3. For normal operation, Water Pressure reading should be in between
0.5 bar and 3 bar (0.05 MPa and 0.3 MPa). If necessary, adjust the
Water Pump
4
SPEED accordingly to obtain normal water pressure
operating range. If adjust Water Pump
4
SPEED cannot solve the
problem, contact your local authorized dealer.
4. Remove the electric anode cover to check the electric anode PCB
r
. (AN model only)
Confi rm the LED is green.
If the LED is red, confi rm the tank is full of water.
If the LED is OFF, please set the electric anode “YES” in the system
set up of the R/C.
5. After test run, please clean the Magnetic Water Filter Set
9
and
Water Filter Set
t
. Reinstall it after fi nish cleaning.
CHECK WATER FLOW OF WATER CIRCUIT
Select Installer setup
Service setup
Pump maximum speed
Air purge
Confi rm the maximum water fl ow during main pump operation not
less than 15 l/min.
*Water fl ow can be check through service setup (Pump Max Speed)
[Heating operation at low water temperature with lower water fl ow
may trigger “H75” during defrost process.]
*If there is no fl ow or H62 is displayed, stop operating the pump and
release the air (see Checking for Air Accumulation P.8).
RESET OVERLOAD PROTECTOR
b
Overload Protector
b
a serves the safety purpose to prevent the
water over heating. When the Overload Protector
b
a trip at high
water temperature, take below steps to reset it.
1. Take out the cover.
2. Use a test pen to push the centre button gently in order to reset
the Overload Protector
b
.
3. Fix the cover to the original fi xing condition.
Use test pen to push
this button for reset
Overload protector
b
.
CHECK ITEMS
Is the Tank Unit properly installed on the concrete fl oor?
Is there any water leakage at water piping connections?
Has the heat insulation been carried out at water piping connection?
Is the Pressure Relief Valve operation normal?
Is water pressure higher than 0.5 bar?
Is the water drainage work properly done?
Is the power supply voltage within the rated voltage range?
Is the cables being fi xed to RCCB/ELCB and terminal board fi rmly?
Is the cables being clamped fi rmly by holder (clamper)?
Is the earth wire connection properly done?
Is the RCCB/ELCB operation normal?
Is the Remote Controller
1
LCD operation normal?
Is there any abnormal sound?
Is the heating operation normal?
Is the Tank unit water leak free on test run?
Is the Safety Relief Valve
o
knob turned for releasing air?
•
In order to ensure safety and optimal performance of the Tank Unit,
seasonal inspections on the Tank Unit, functional check of RCCB/
ELCB, fi eld wiring and piping have to be carried out at regular
intervals. This maintenance should be carried out by authorized
dealer. Contact dealer for scheduled inspection.
Maintenance for Magnetic Water Filter Set
9
1. Turn OFF power supply.
2. Place a container below Magnetic Water Filter Set
9
.
3. Turn to remove the Magnet Bar at bottom of Magnetic Water Filter Set
9
.
4. By using Allen key (8mm), remove the Cap of Discharge Port.
5. By using Allen Key (4mm), open the Service Valve to release the dirty water
from the Discharge Port into a container. Close the service valve when the
container is full to avoid spillage in the tank unit. Dispose the dirty water.
TEST RUN
6. Reinstall the Cap of Discharge Port and Magnet Bar.
7. Re-charging the water to Space Heating / Cooling circuit if necessary
(refer Section 5 for details.)
8. Turn ON power supply.
Service
Valve
Magnet Bar
Open
Close
Discharge port
Maintenance for Safety Relief Valve
o
•
It is strongly recommended to operate the valve by turn the knob
counter clockwise to ensure free water fl ow through discharge
pipe at regular intervals to ensure it is not blocked and to remove
lime deposit.
Stagnant water in Tank Unit should be drained if it is not going to
be operated for more than 60 days.
Installation of Ventilation Unit on top of Tank Unit (Optional)
•
For installation works of Ventilation Unit on top of Tank Unit, refer
to the Ventilation Unit Installation Manual.
CAUTION
Before install Ventilation Unit, fi x the Feet that provided by Ventilation
Unit to the half punch holes on Top Panel of Tank Unit,
Otherwise, heavy Ventilation Unit may fall and cause injury.
Feet (4 pieces)
- provided by Ventilation Unit
Half punch holes
8
MAINTENANCE
9