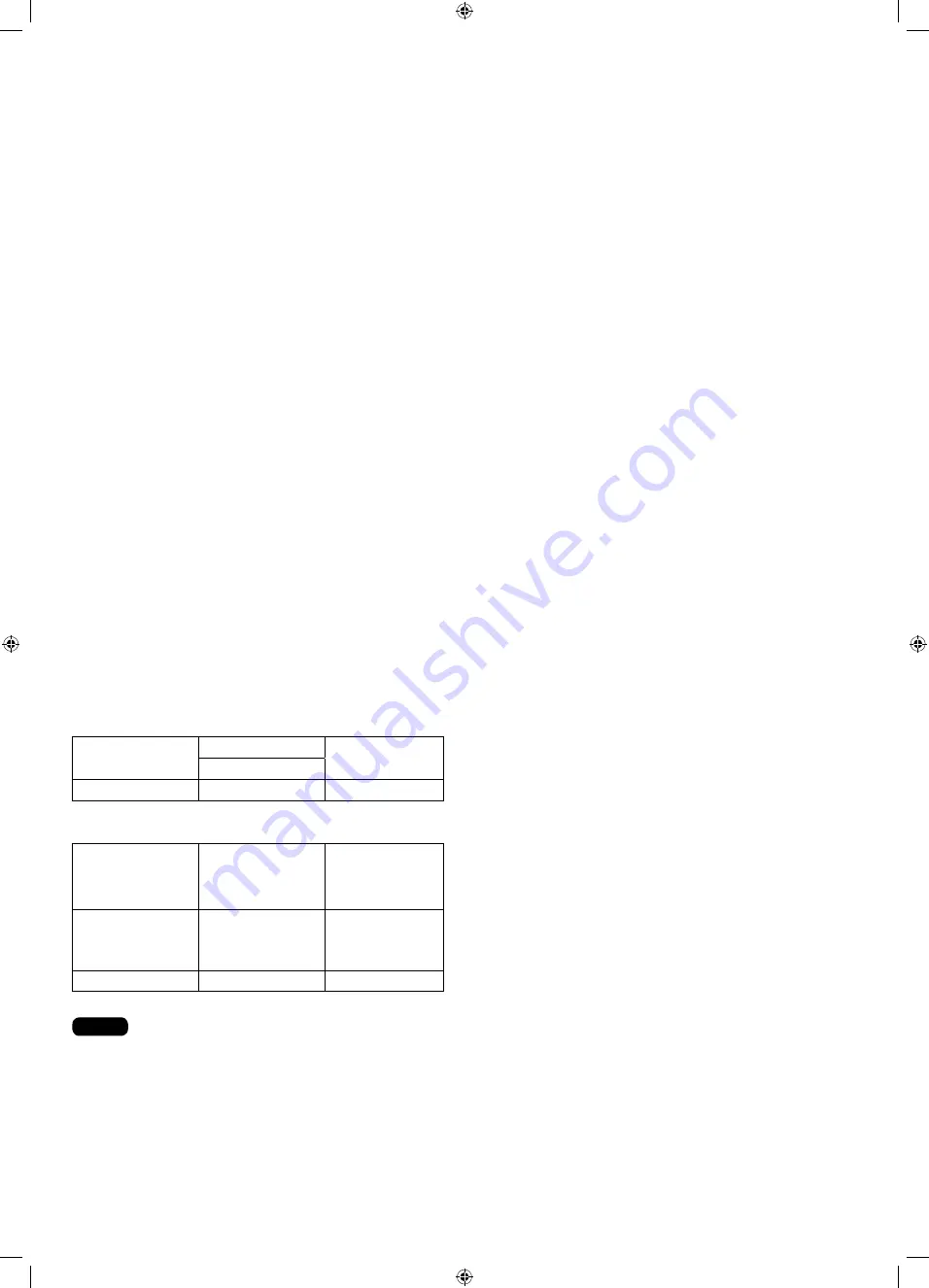
18
4. ELECTRICAL WIRING
4-1. General Precautions on Wiring
(1) Before wiring, confi rm the rated voltage of the unit as shown
on its nameplate, then carry out the wiring closely following the
wiring diagram.
(2) Provide a power outlet to be used exclusively for each unit and
a circuit breaker for overcurrent protection should be provided
in the exclusive line.
(3) To prevent possible hazards from insulation failure, the unit
must be grounded.
(4) Each wiring connection must be done in accordance with the
wiring system diagram. Wrong wiring may cause the unit to
misoperate or become damaged.
(5) Do not allow wiring to touch the refrigerant tubing, compressor,
or any moving parts of the fan.
(6) Unauthorized changes in the internal wiring can be very
dangerous. The manufacturer will accept no responsibility for
any damage or misoperation that occurs as a result of such
unauthorized changes.
(7) Regulations on wire diameters differ from locality to locality. For
fi eld wiring rules, please refer to your LOCAL ELECTRICAL
CODES before beginning.
You must ensure that installation complies with all relevant
rules and regulations.
(8) To prevent malfunction of the air conditioner caused by
electrical noise, care must be taken when wiring as follows:
The remote control wiring and the inter-unit control wiring should
be wired apart from the inter-unit power wiring.
Use shielded wires for inter-unit control wiring between units
and ground the shield on both sides.
(9) If the power supply cord of this appliance is damaged, it must
be replaced by a repair shop designated by the manufacturer,
because special-purpose tools are required.
4-2. Recommended Wire Length and Wire Diameter for Power
Supply System
Indoor unit
Type
(B) Power supply
Time delay fuse or
circuit capacity
2.5 mm
2
N1 SERIES
Max. 130 m
10-16 A
Control wiring
(C) Inter-unit
(between outdoor
and indoor units)
control wiring
(D) Remote control
wiring
(E) Control wiring
for group control
0.75 mm
2
(AWG #18)
Use shielded
wiring*
0.75 mm
2
(AWG #18)
0.75 mm
2
(AWG #18)
Max. 1,000 m
Max. 500 m
Max. 200 m (Total)
NOTE
* With ring-type wire terminal.
P07-T11630.indb 18
P07-T11630.indb 18
2/27/2012 9:21:19 AM
2/27/2012 9:21:19 AM
Summary of Contents for S-100PN1E5A
Page 1: ......