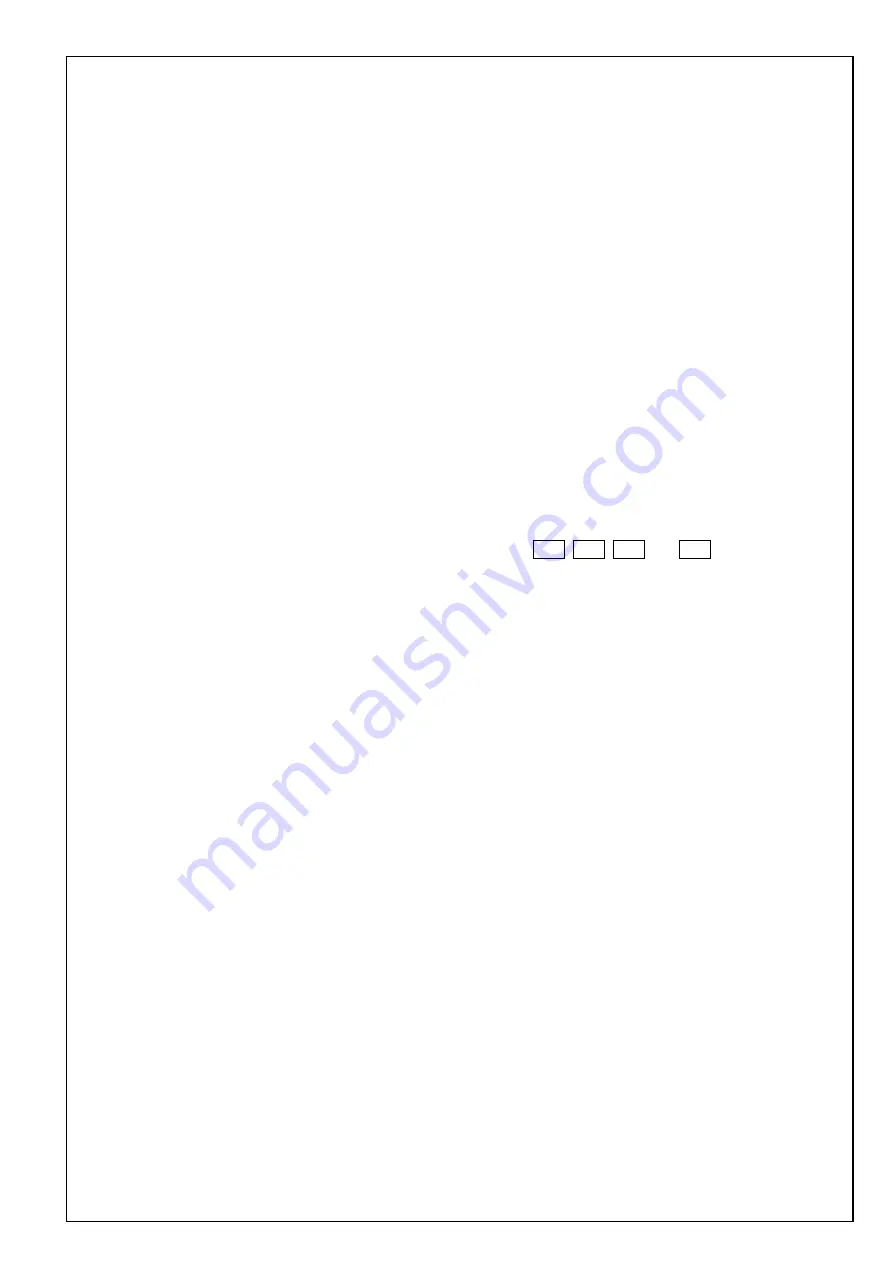
No. SX-DSV03015 - 40 -
Motor Business Unit, Panasonic Corporation
[1] When the servo driver uses single phase power supply for sizes A - D, connect the servo driver to the
terminals L1, L3 of main power supply input. Do not connect anything to the terminal L2.
[2] Surely insert the connector into place until it clicks.
[3] Make sure to use an insulation coated crimp terminal when connecting to each terminal on the terminal
block.
[4] Terminal block cover is fixed with screws. When wiring to the terminal block, unscrew these screws to
uncover the cover. Tighten the cover fixing screw with the torque of 0.2 Nm or less.
[5] To not use an external regenerative resistor, short out the circuit between terminals RB and B. (For sizes C,
D, E, F)When a trip occurs due to the regenerative load protection error No.18.0, externally install a
regenerative resistor.
To externally install a regenerative resistor, remove a connection cable between terminals RB, B and then
connect the regenerative resistor between terminals P, B.
The products (Sizes A, B) supporting only the external regenerative resistor, connect an external
regenerative resistor if necessary.
To use an external regenerative resistor, set Pr.0.16 (external regenerative resistor selection) to 1 or 2.
[6] Apply the power supply of the voltage indicated on the nameplate.
[7] Do not reverse-connect the power input terminals (L1, L2, and L3) and the motor output terminals (U, V,
and W).
[8] Do not connect the motor output terminals (U, V, and W) to ground or short out them.
[9] Because high voltage is applied to the power connectors XA , XB , XC , and XD , and the terminal
block, never touch them on any account. It may cause electric shock.
[10] Suitable for use on a circuit capable of delivering not more than 5000 rms symmetrical amperes, below the
maximum input voltage of the product.
[11] An AC servomotor, unlike an induction motor, cannot change the rotation direction by exchanging three
phases.
Make sure to coincide the motor output terminals (U, V, and W) of the servo driver with the colors
(pin number for cannon plugs) of the motor output cables.
[12] Surely connect the ground terminals of the motor and the servo driver and earth the ground terminal as well
as that of the noise filter. In addition, earth the equipment unit. To earth them, ground resistance should be
100 ohm or less for grounding.
When the power supply voltage is over 300 V ground resistance should be 10ohm or less.
Please tight the earth screws by appropriate torque and use correct size earth cable decided in the
specifications.
In order to avoid the impact of electrolytic corrosion, do not immediately have any contact between
aluminum and copper.
[13] Attach the serge absorbing circuits for preventing noises to an electromagnetic contactor placed around the
servo driver, a coil between relay contact points, and a brake winding of motor with a brake.
[14] Attach the no fuse breaker. In case of emergency, make sure to power off outside the servo driver. To use
an earth leakage circuit breaker, use that in which a high frequency wave countermeasure is taken.
[15] In order to reduce the terminal noise voltage, install a noise filter.
[16] Customer is responsible for the power supply of the brake attached to a motor.
[17] Turn ON the power after the wiring was finished.