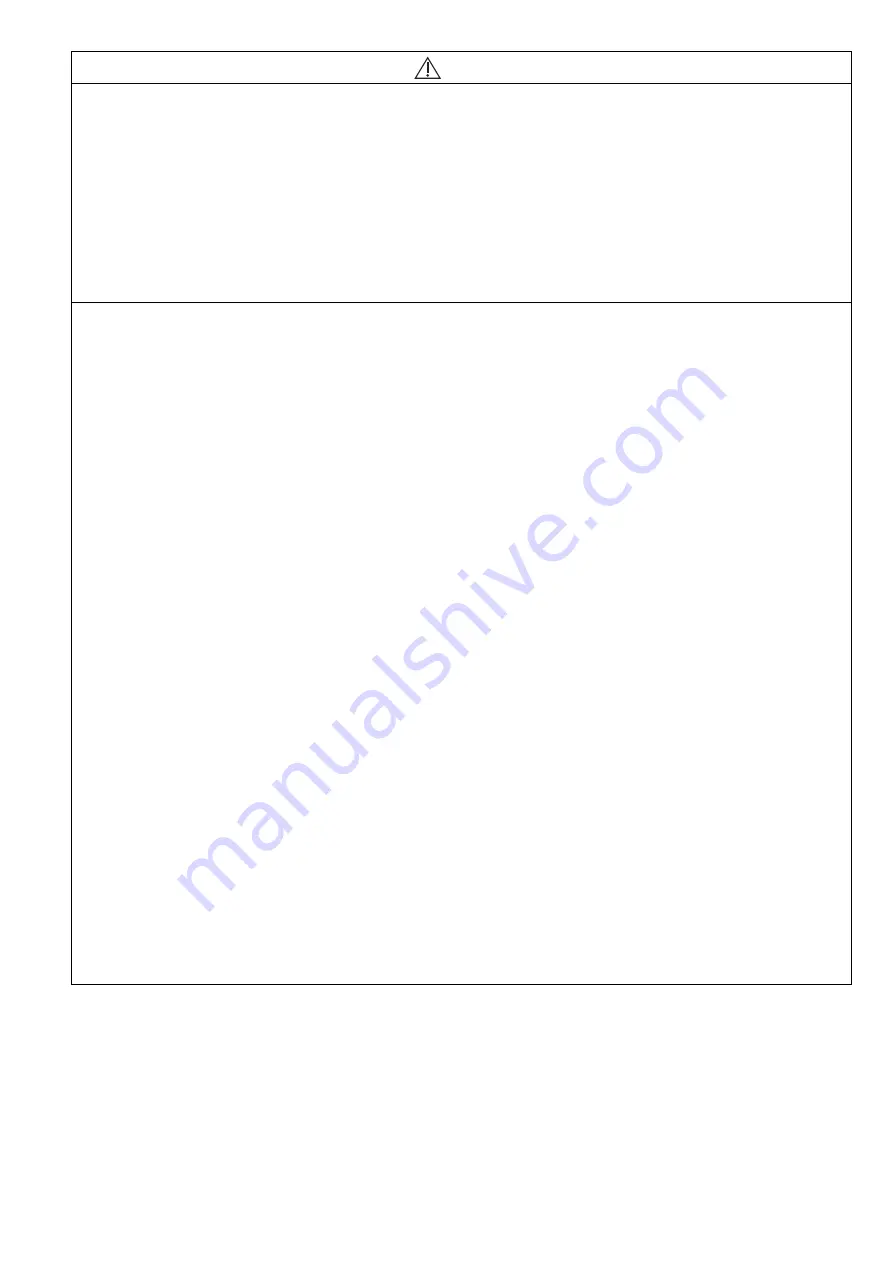
7
CAUTION
1.
General
Must ensure the installation of pipe-work shall be kept to a minimum. Avoid use dented pipe and do not allow acute bending.
Must ensure that pipe-work shall be protected from physical damage.
Must comply with national gas regulations, state municipal rules and legislation. Notify relevant authorities in accordance with all
applicable regulations.
Must ensure mechanical connections be accessible for maintenance purposes.
In cases that require mechanical ventilation, ventilation openings shall be kept clear of obstruction.
When disposal of the product, do follow to the precautions in #12 and comply with national regulations.
In case of field charge, the effect on refrigerant charge caused by the different pipe length has to be quantified, measured and
labelled.
Always contact to local municipal offices for proper handling.
Ensure the actual refrigerant charge is in accordance with the room size within which the refrigerant containing parts are installed.
Ensure refrigerant charge not to leak.
Wear appropriate protective equipment, including respiratory protection, as conditions warrant.
Keep all sources of ignition and hot metal surfaces away.
2.
Servicing
2-1. Qualification of workers
Any qualified person who is involved with working on or breaking into a refrigerant circuit should hold a current valid certificate from
an industry-accredited assessment authority, which authorizes their competence to handle refrigerants safely in accordance with an
industry recognized assessment specification.
Servicing shall only be performed as recommended by the equipment manufacturer. Maintenance and repair requiring the
assistance of other skilled personnel shall be carried out under the supervision of the person competent in the use of flammable
refrigerants.
Servicing shall be performed only as recommended by the manufacturer.
The system is inspected, regularly supervised and maintained by a trained and certified service personnel who is employed by the
person user or party responsible.
2-2. Checks to the area
Prior to beginning work on systems containing flammable refrigerants, safety checks are necessary to ensure that the risk of
ignition is minimised.
For repair to the refrigerating system, the precautions in #2-3 to #2-7 must be followed before conducting work on the system.
2-3. Work procedure
Work shall be undertaken under a controlled procedure so as to minimize the risk of a flammable gas or vapour being present while
the work is being performed.
2-4. General work area
All maintenance staff and others working in the local area shall be instructed and supervised on the nature of work being carried
out.
Avoid working in confined spaces. Always ensure away from source, at least 2 meter of safety distance, or zoning of free space
area of at least 2 meter in radius.
2-5. Checking for presence of refrigerant
The area shall be checked with an appropriate refrigerant detector prior to and during work, to ensure the technician is aware of
potentially flammable atmospheres.
Ensure that the leak detection equipment being used is suitable for use with flammable refrigerants, i.e. non sparking, adequately
sealed or intrinsically safe.
In case of leakage/spillage happened, immediately ventilate area and stay upwind and away from spill/release.
In case of leakage/spillage happened, do notify persons downwind of the leaking/spill, isolate immediate hazard area and keep
unauthorized personnel out.
2-6. Presence of fire extinguisher
If any hot work is to be conducted on the refrigeration equipment or any associated parts, appropriate fire extinguishing equipment
shall be available at hand.
Have a dry powder or CO
2
fire extinguisher adjacent to the charging area.
2-7. No ignition sources
No person carrying out work in relation to a refrigeration system which involves exposing any pipe work that contains or has
contained flammable refrigerant shall use any sources of ignition in such a manner that it may lead to the risk of fire or explosion.
He/She must not be smoking when carrying out such work.
All possible ignition sources, including cigarette smoking, should be kept sufficiently far away from the site of installation, repairing,
removing and disposal, during which flammable refrigerant can possibly be released to the surrounding space.
Prior to work taking place, the area around the equipment is to be surveyed to make sure that there are no flammable hazards or
ignition risks.
“No Smoking” signs shall be displayed.
2-8. Ventilated area
Ensure that the area is in the open or that it is adequately ventilated before breaking into the system or conducting any hot work.
A degree of ventilation shall continue during the period that the work is carried out.
The ventilation should safely disperse any released refrigerant and preferably expel it externally into the atmosphere.