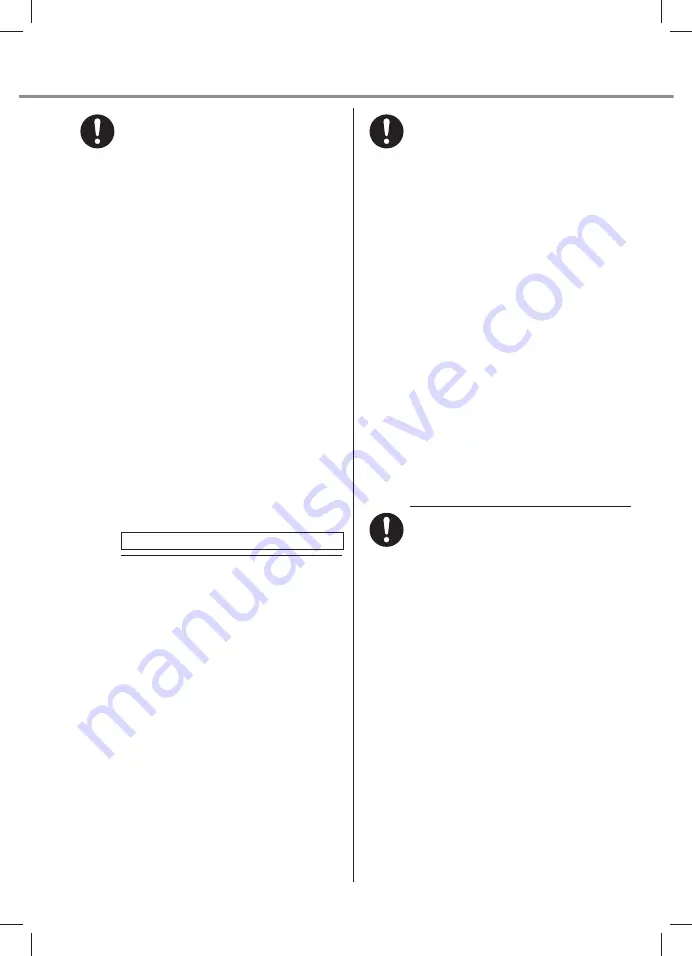
10
Safety precautions
9. Charging procedures
• In addition to conventional charging
procedures, the following requirements shall
be followed.
- Ensure that contamination of different
refrigerants does not occur when using
charging equipment.
- Hoses or lines shall be as short as possible
to minimize the amount of refrigerant
contained in them.
- Cylinders shall be kept in an appropriate
position according to the instructions.
- Ensure that the refrigerating system is
earthed prior to charging the system with
refrigerant.
- Label the system when charging is
complete (if not already).
- Extreme care shall be taken not to over fi ll
the refrigerating system.
• Prior to recharging the system it shall be
pressure tested with OFN (refer to #7).
• The system shall be leak tested on completion
of charging but prior to commissioning.
• A follow up leak test shall be carried out prior
to leaving the site.
• Electrostatic charge may accumulate and
create a hazardous condition when charging
and discharging the refrigerant.To avoid fi re
or explosion, dissipate static electricity during
transfer by grounding and bonding containers
and equipment before charging/discharging.
10. Decommissioning
• Before carrying out this procedure, it is
essential that the technician is completely
familiar with the equipment and all its details.
• It is recommended good practice that all
refrigerants are recovered safely.
• Prior to the task being carried out, an oil
and refrigerant sample shall be taken in
case analysis is required prior to re-use of
recovered refrigerant.
• It is essential that electrical power is available
before the task is commenced.
a) Become familiar with the equipment and
its operation.
b) Isolate system electrically.
c) Before attempting the procedure ensure
that:
• mechanical handling equipment is
available, if required, for handling
refrigerant cylinders;
• all personal protective equipment is
available and being used correctly;
• the recovery process is supervised at all
times by a competent person;
• recovery equipment and cylinders conform
to the appropriate standards.
d) Pump down refrigerant system, if possible.
8. Removal and evacuation
• When breaking into the refrigerant circuit
to make repairs – or for any other purpose
– conventional procedures shall be used.
However, it is important that best practice is
followed since fl ammability is a consideration.
The following procedure shall be adhered to:
remove refrigerant -> purge the circuit with
inert gas -> evacuate -> purge with inert gas
-> open the circuit by cutting or brazing
• The refrigerant charge shall be recovered into
the correct recovery cylinders.
• The system shall be purged with OFN to
render the appliance safe.
• This process may need to be repeated
several times.
• Compressed air or oxygen shall not be used
for this task.
• Purging shall be achieved by breaking
the vacuum in the system with OFN and
continuing to fi ll until the working pressure is
achieved, then venting to atmosphere, and
fi nally pulling down to a vacuum.
• This process shall be repeated until no
refrigerant is within the system.
• When the fi nal OFN charge is used, the
system shall be vented down to atmospheric
pressure to enable work to take place.
• This operation is absolutely vital if brazing
operations on the pipe work are to take place.
• Ensure that the outlet for the vacuum pump
is not close to potential ignition sources and
there is ventilation available.
OFN = oxygen free nitrogen, type of inert gas.
ACXF55-28780_SS0720-0.indd 10
25/6/2020 11:10:07 AM