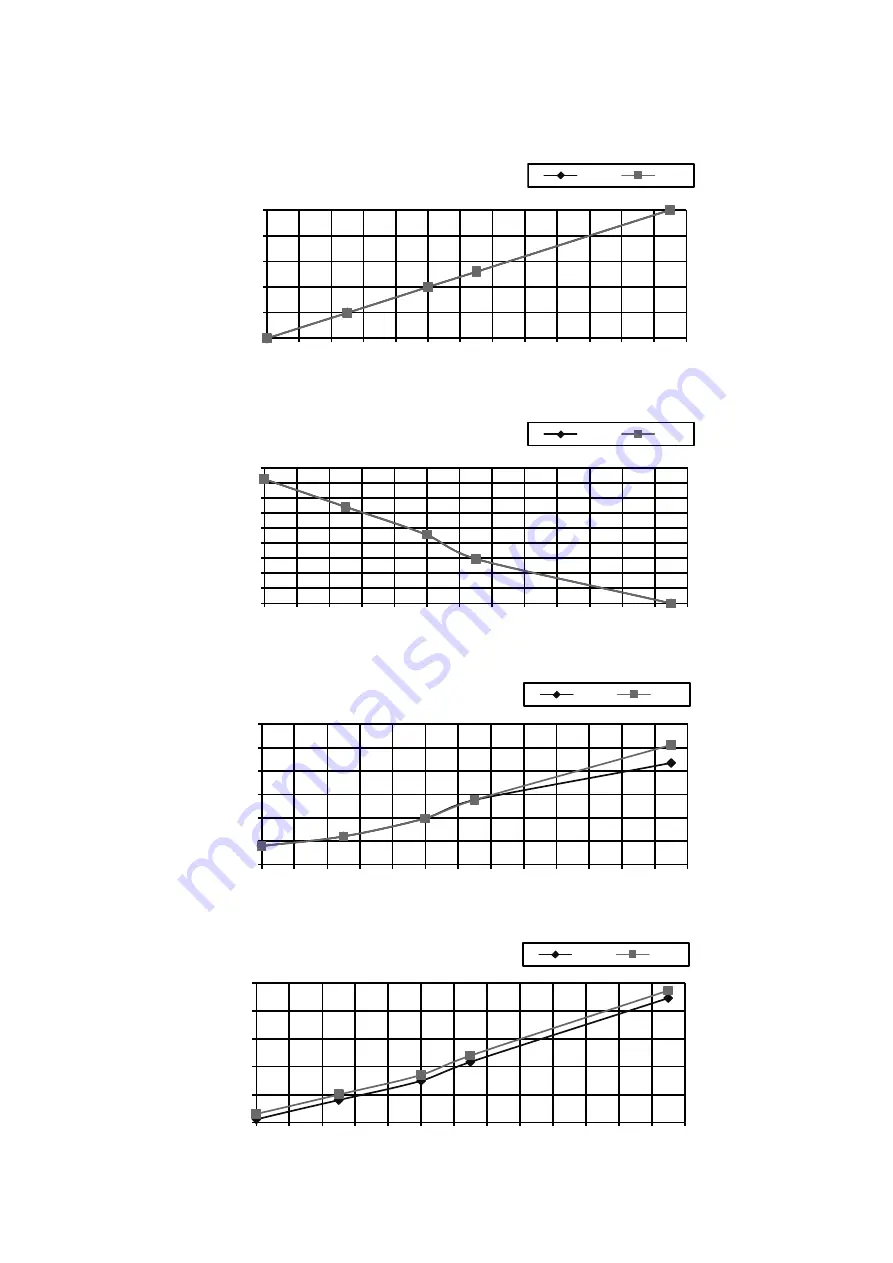
74
17.2.2 CS-PC18TKF
CU-PC18TKF
Cooling
Characteristic
[Condition] Room
temperature: 27°C (DBT), 19°C (WBT)
Operation condition: High fan speed
Piping length: 5.0 m
14.500
15.000
15.500
16.000
16.500
17.000
30
32
34
36
38
40
42
44
46
48
50
52
54
56
In
doo
r
D
is
ch
ar
ge
Air
T
e
m
p
e
ra
tu
re
(
℃
)
Outdoor Temperature (℃)
220V
240V
4.000
4.200
4.400
4.600
4.800
5.000
5.200
5.400
5.600
5.800
30
32
34
36
38
40
42
44
46
48
50
52
54
56
Ca
pa
ci
ty
(kW
)
Outdoor Temperature (℃)
220V
240V
9.000
10.000
11.000
12.000
13.000
14.000
30
32
34
36
38
40
42
44
46
48
50
52
54
56
Cu
rr
ent
(
A
)
Outdoor Temperature (℃)
220V
240V
0.450
0.500
0.550
0.600
0.650
0.700
0.750
30
32
34
36
38
40
42
44
46
48
50
52
54
56
Ga
s
S
id
e
Pipin
g
Pre
ssu
re
(M
Pa
)
Outdoor Temperature (℃)
220V
240V