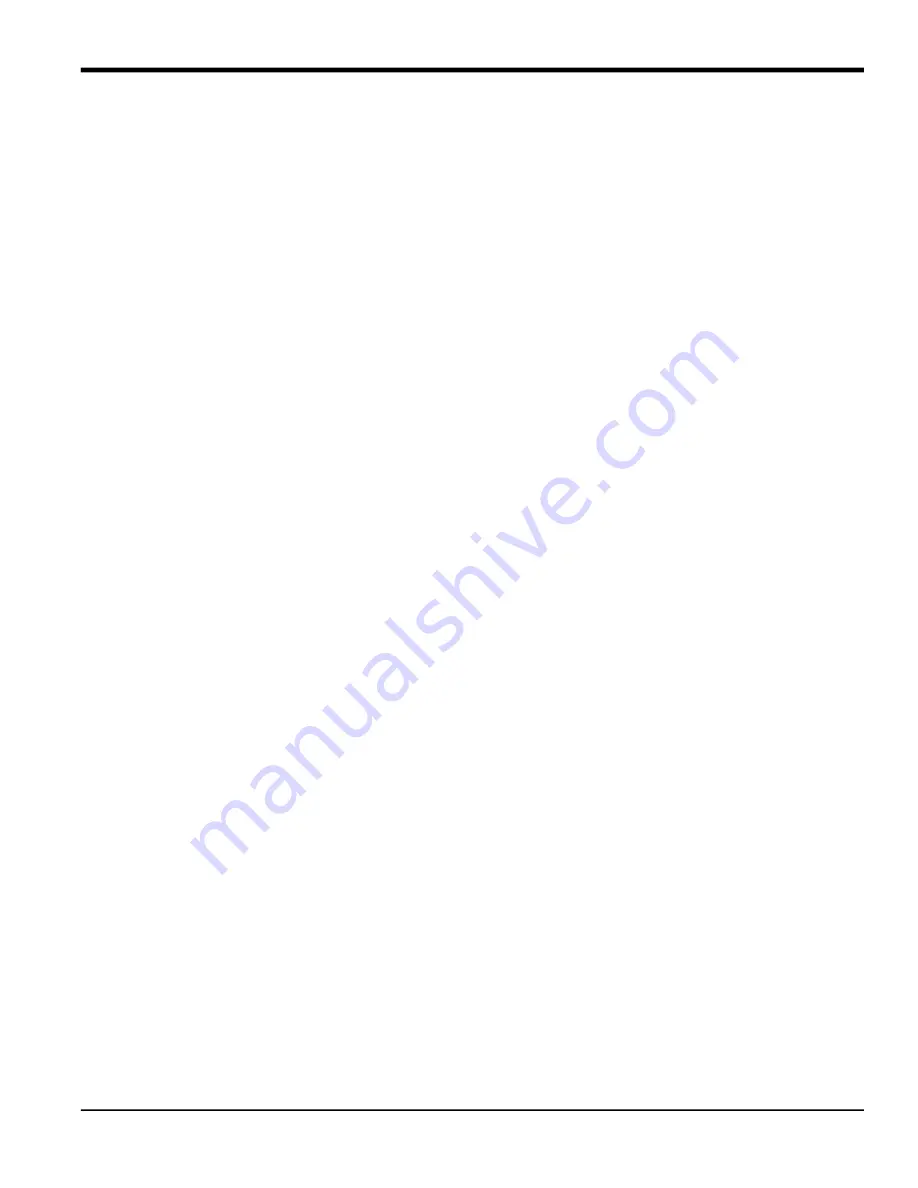
DigitalFlow™ XMT868i Service Manual
3
Chapter 4. Parts Replacement
4.3 Replacing the LCD Display/Interconnect Board Subassembly
The LCD display normally provides years of dependable service, but it is easily field-replaceable when necessary. To
replace the LCD display, see Figure 8 on page 12 for the component locations, and complete the following steps:
1.
Complete the steps in
Removing the Circuit Board Assembly
2.
Place the circuit board assembly on a flat surface with the LCD display board facing upward. Refer to Illustration
4 in Figure 8 on page 12, and remove the
three mounting screws
(with flat washers and lock washers) indicated.
3.
Grasp the LCD display/keypad board/interconnect board subassembly at the top and bottom edges, and
carefully pull it straight upward until it comes free from the main board and option boards. Refer to Illustration 5
in Figure 8 on page 12. Remove two screws from the back of the interconnect board. Then hold the edge of the
keypad board by one hand, and the edge of the LCD display/interconnect board by the other hand, and pull the
two boards apart.
Note:
The two circuit boards are attached by a connector located beneath the top edge of the LCD display board
(see Illustration 5 in Figure 8 on page 12). The LCD display is attached to the interconnect board as one
subassembly.
Do not
disassemble the LCD display from the interconnect board.
4.
Place the keypad board directly over the new LCD display/interconnect board subassembly and align the J1
connector on the rear of the keypad board with the P6 pins on the interconnect board. Firmly, push the two
boards together until the interconnect board contacts the two standoffs on the keypad board.
5.
Secure the keypad board to the interconnect board with the two screws, flat washers and lock washers
previously removed.
6.
Firmly insert and seat the complete assembly by aligning the P4 connector on the interconnect board to the J4
connector on the main board and the P1 and P2 connectors to any option card (as applicable). Replace the three
screws removed in step 2, while referring back to Illustration 4 in Figure 8 on page 12.
Complete the LCD display/interconnect board subassembly replacement by proceeding to
Installing the Circuit
Board Assembly
Summary of Contents for DigitalFlow XMT868i
Page 2: ......
Page 4: ...ii no content intended for this page...
Page 24: ...Chapter 2 Error Codes 4 DigitalFlow XMT868i Service Manual...
Page 34: ...Chapter 3 Diagnostics 10 DigitalFlow XMT868i Service Manual...
Page 44: ...Chapter 4 Parts Replacement 10 DigitalFlow XMT868i Service Manual...
Page 48: ...Chapter 4 Parts Replacement DigitalFlow XMT868i Service Manual...
Page 52: ...Appendix A Service Record 18 DigitalFlow XMT868i Service Manual...
Page 66: ...Appendix B Calibration and Testing with PanaView 32 DigitalFlow XMT868i Service Manual...
Page 72: ...Warranty 38 DigitalFlow XMT868i Service Manual no content intended for this page...
Page 73: ......