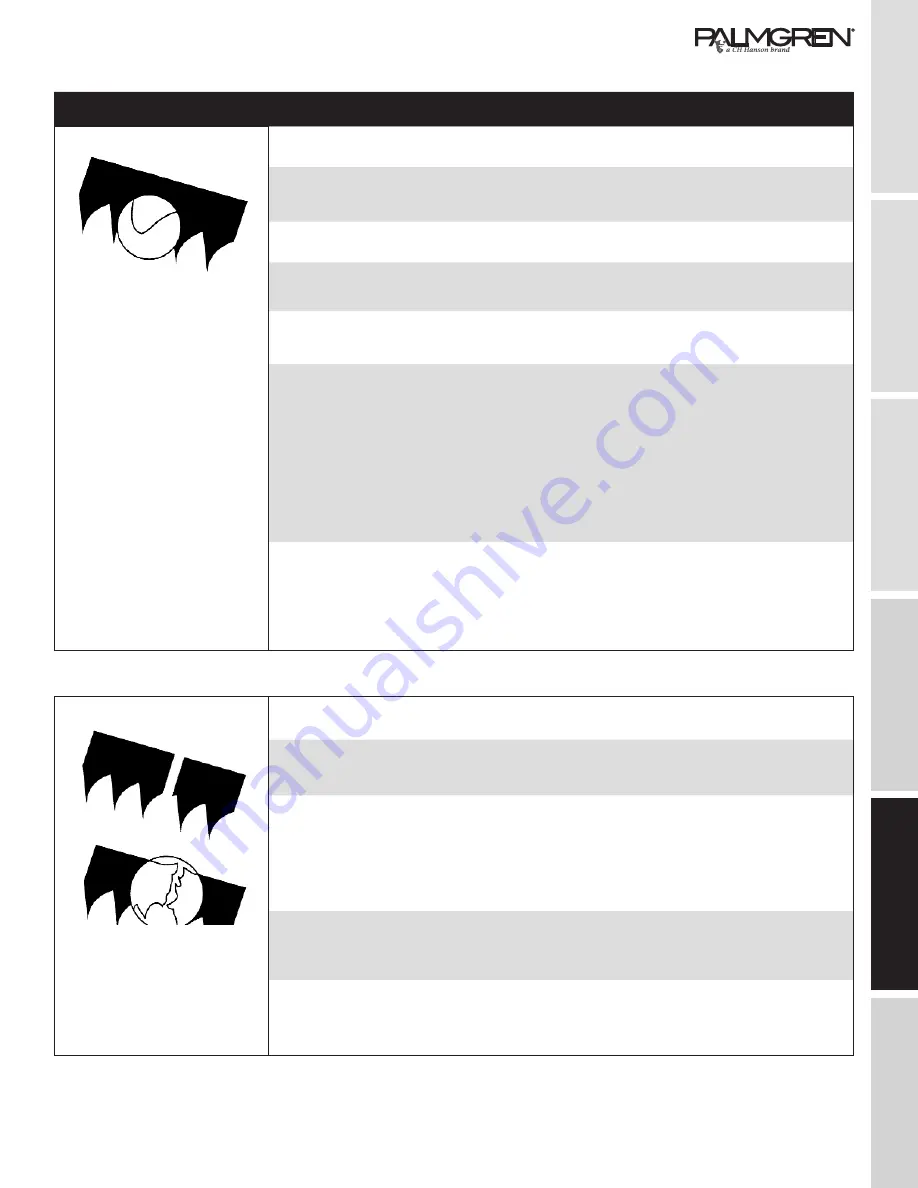
21
GETTING STARTED
SAFETY / SPECIFICATIONS
ASSEMBLY / INSTALLATION
OPERATION
TROUBLESHOOTING
MAINTENANCE / REPAIR
TROUBLESHOOTING GUIDE
Symptom
Possible Cause(s)
Corrective Action
Premature blade wear
Faulty blade break-in
Break in a new blade. (See pgs. 12 and 13)
Teeth positioned in the direction opposite
of the cutting direction
Remove the blade and reinstall it with the teeth
cutting in the proper direction.
Poor quality blade
Switch to a superior quality blade.
Cut advancing too quickly
Decrease cutting advance, exerting less cutting
pressure.
Wrong cutting speed
Change speed and/or type of blade to better
match the material being cut.
Defects on the material or material too
hard
Material surfaces can be oxidized or covered with
impurities making these areas harder than the
blade itself. Materials may have hardened areas
or inclusions inside the section due to production
materials such as castings and welding wastes,
etc. Avoid cutting these materials. In a situation
where a cut has to be made use extreme care,
cleaning and removing hard impurities as quickly
as possible.
Insufficient coolant. Coolant not flowing or
wrong coolant
Check level of coolant in the tank. Check to
ensure the coolant is flowing freely. Check the
lubricant viscosity. In cold situations the coolant
may need to be heated with the optional heater.
Check and user proper lubricant.
Blade breakage/damage
Faulty welding of blade
Switch to a superior quality blade.
Cut advancing too quickly
Decrease cutting advance, exerting less cutting
pressure. Adjust the braking device.
Wrong cutting speed
Change speed and/or type of blade to better
match the material being cut.
Wrong tooth pitch
Replace blade choosing the proper tooth pitch. to
better match the material being cut.
Ineffective gripping of the part in the vice
Check the gripping of the part being cut. Adjust
the position of the material being cut so the vise
clamps better.
Blade touching material at beginning of
cut
The saw bow should advance quickly and then
slow before beginning a cut. Have a qualified
technician troubleshoot any issues.