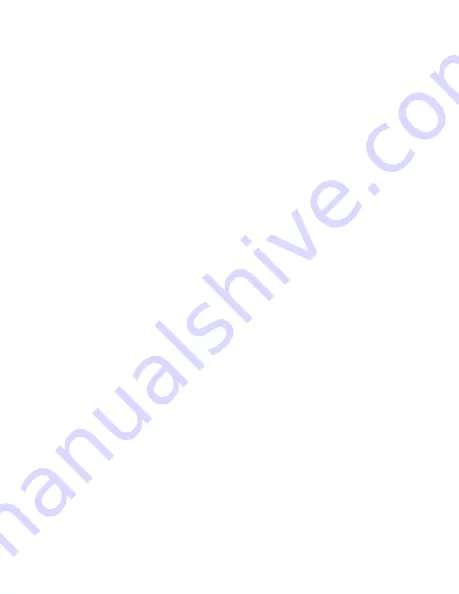
pressurizing unit with 30 psig (0.21 MPa) of HCl for 2 hours and then flowing
5.0 slpm (10.6 scfh) of 100% process gas through the unit for 150 minutes.
Ensure that effluent gas during conditioning is directed to a scrubber or vent
and NOT the process tool.
Note:
During the conditioning, the surface temperature of the purifier may
feel warm to the touch. If the purifier feels hot, continue conditioning by
reducing the gas flow rate or introducing an inert gas to create a dilute
blend until the elevated temperature subsides then return to previous
conditioning parameters. No damage to the purification material or
purifier is expected. Once the unit has completely cooled, the purifier is
ready for service.
For purifiers containing HCLP or HBRP material, the indicator is shipped with
the assembly but is not affixed to the housing. After conditioning (
i.e.
when
the housing has returned to room temperature) attach the supplied over-
temperature indicator sticker to the housing where it can be easily seen.
Alternative Group III:
For SiH
3
Cl, SiH
2
Cl
2
, SiHCl
3
, SiCl
4
and BF
3
.
For Group III gases, conditioning can alternately be done first with a dilute
blend containing less than 20% process gas at a low flow rate. After using a
dilute blend, the conditioning should be repeated using the actual (operating)
blend of process gas. This two-step conditioning procedure will help prevent
the generation of excess temperatures within the purifier. High temperature
will not damage the AresKleen purification material but may lead to
decomposition of the process gas and may cause a personnel hazard
because of a hot surface.
Refer to Table 4, columns B and D. Slowly, pressurize purifier with dilute
blend at ≥ 15 psig (0.10 MPa) for 2 hours (do not exceed maximum flow