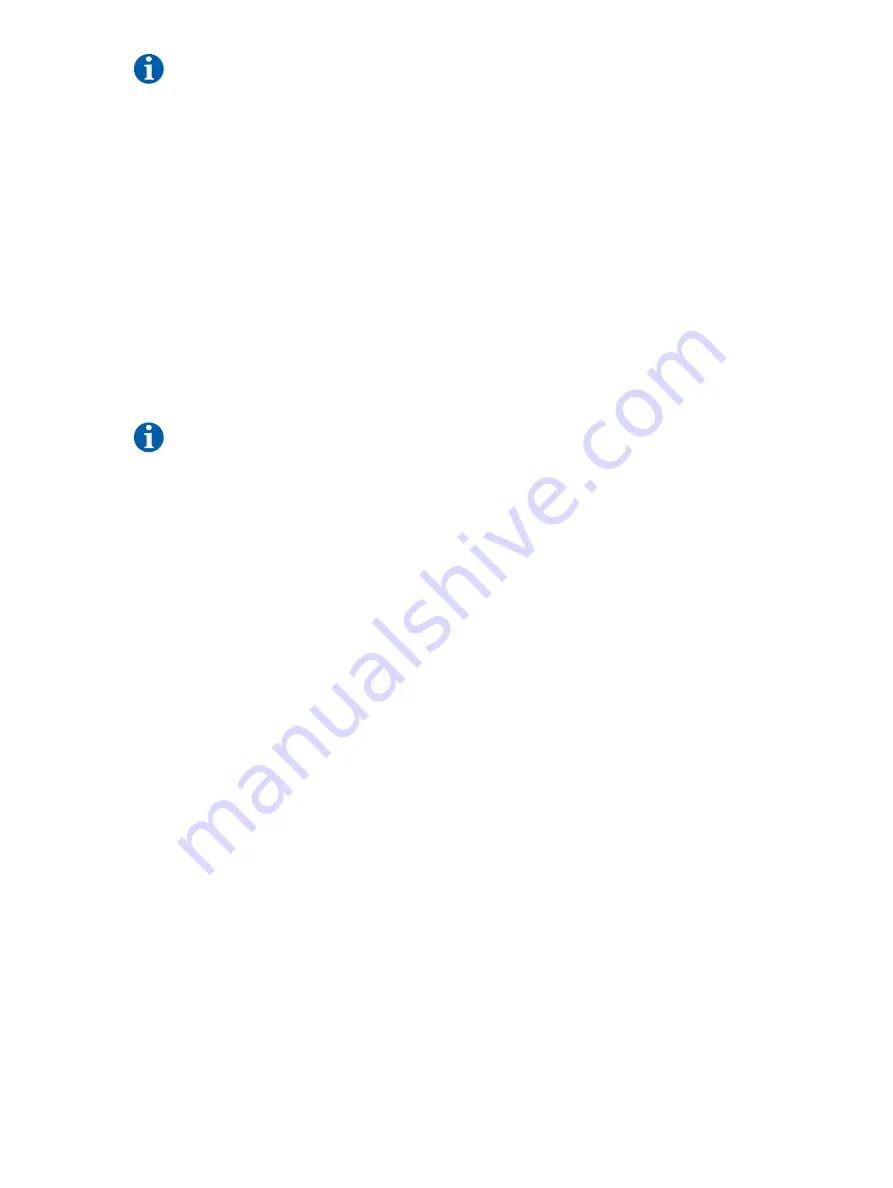
www.pall.com/biotech
17
HELPFUL INFORMATION:
The effectiveness of this cleaning procedure to remove product
residue will depend on the nature of the product. The user must evaluate and validate the
effectiveness of the cleaning process with respect to time, cleaning agent, and operating
conditions. Refer to the T-Series User Guides USTR2662 (Delta) and USTR2433 (Omega)
for more information on cleaning agents.
u
Procedure L — Flush the Cadence ILC Module with Purified Water
Flush the cleaning solution from the Cadence ILC module and system with purified water
following these steps:
1. Connect the feed line to a supply of purified water.
2. Direct the retentate and permeate lines to a collection vessel or waste.
3. Open the feed, retentate, and permeate 2 lines. Close the permeate 1 line.
4. Start the feed pump and slowly increase the pump speed until the feed pressure
reaches 1.4 – 4.1 barg (20 – 60 psig).
5. During flushing, open the permeate 1 line for 30 seconds. Repeat every 5 minutes.
6. Stop the feed pump after 25 L/m
2
of water passes through the module or when the
pH reaches
≤
7.
HELPFUL INFORMATION!
The effectiveness of this flushing protocol will depend on the
composition and volume of chemicals in the module and minimum acceptable levels in effluent
at the end of the flush. The user must evaluate and validate the effectiveness of the process
with respect to time, temperature and other operating conditions.
u
Procedure M — Determine Cadence ILC Module Normalized Water Permeability (NWP)
Determine the membrane NWP following the steps in Procedure E — Determine Cadence ILC
module Normalized Water Permeability (NWP).
As explained in Procedure E, a membrane NWP measurement before use and after use and
cleaning will provide a comparison to determine the effectiveness of the cleaning process.
Between uses, modules are typically stored in a sodium hydroxide solution (e.g., 0.1 N NaOH).
During this time, remaining foulants on the membrane may be degraded and removed when
the module is flushed prior to next use. As a result of membrane relaxation and static cleaning
during storage, it is not unusual for the module NWP, measured after storage, to increase
relative to the module NWP measured immediately after cleaning.
u
Procedure N — Test Integrity of the Cadence ILC Module
Test the integrity of the Cadence set-up and ILC module following the steps in
Procedure G — Test the Integrity of the Cadence Set-Up and ILC Module.
u
Procedure O — Add Storage Solution to the Cadence ILC Module
The objective for proper storage of the Cadence ILC module is to ensure the module remains
wet and to prevent microbial growth during storage.
Continue with the procedure
Adding Storage Solution to the Cadence ILC Module
provided
below.
Adding Storage Solution to the Cadence ILC Module
1. Connect the feed line to a supply of storage solution (see Materials Section 5.1).
2. Open the feed, retentate, and permeate 2 lines. Close the permeate 1 line.
3. Direct retentate and permeate lines to collection vessel or drain.
4. Start the feed pump and slowly increase the pump speed until the feed pressure reaches
1.4 – 2.8 barg (20 – 40 psig).
5. Open the permeate 1 line for 30 seconds and then close for the remainder of the procedure.