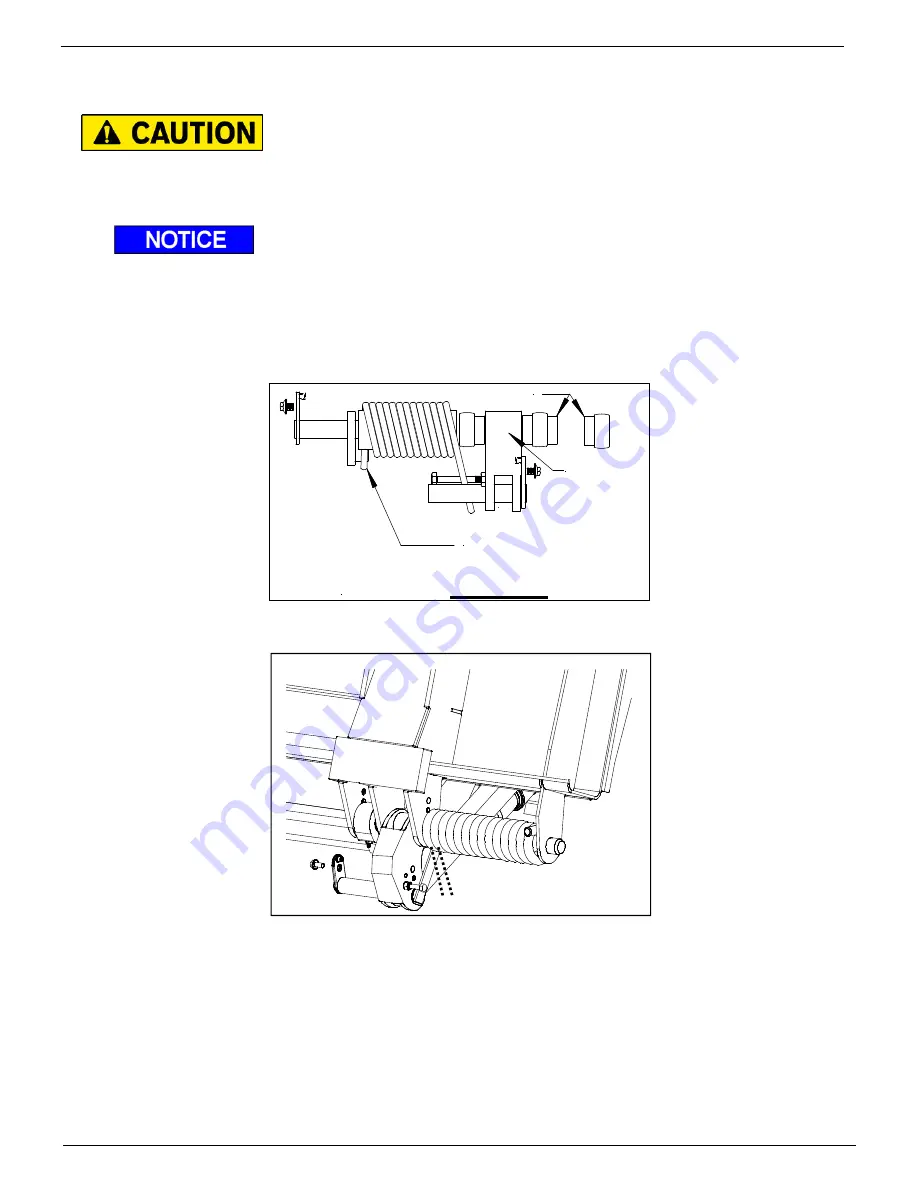
6
Gate and Platform Installation
Revision 1.3
- 19 -
6.2.1
Platform Installation
Never work under platform without safety supports
1. Support gate frame assembly on proper size and capacity horses or equiv.
2. Slide pins out to clear lift arm clevis (closest to center of platform)
3.
Do not slide so far that triangle block or spring fall out
4. Lift platform to lift arms with forklift or equiv.
5. Rotate coil spring away from 8x80mm bolt, so there is no tension during gate installation
6. Align lift arms into clevises and drive pin until pin tab seats in pin tab hole and install pin bolt and
tighten to 14 ft-lbs
Short leg against tab
Curb Side
LOOKING
Rear
Liftarm Clevis
Triangle Block
Figure 19 Platfrom spring installation
Figure 20 Platform coil spring install