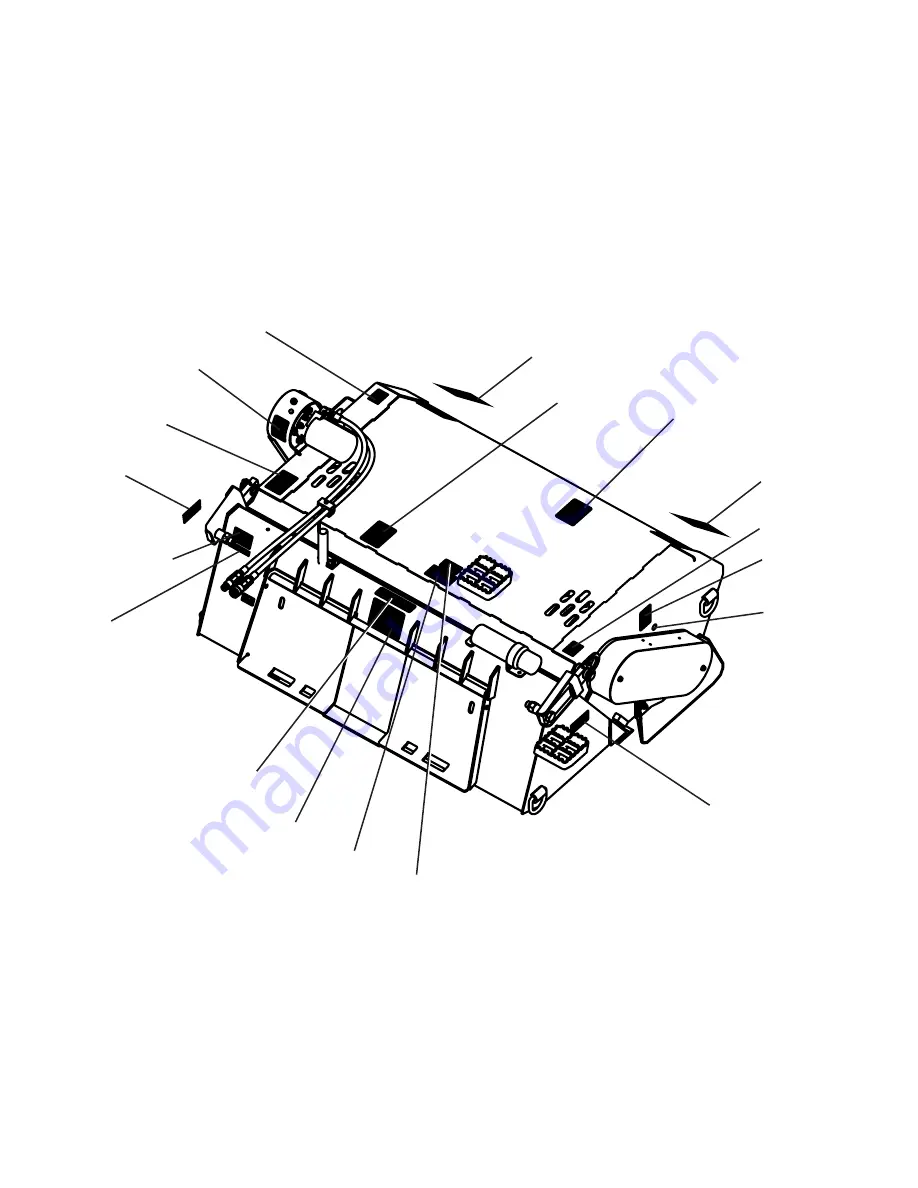
MR955512
11
DECALS
DECAL PLACEMENT
GENERAL INFORMATION
The diagram on this page shows the location of the decals used on your attachment.
The decals are identified by their part numbers, with reductions of the actual decals located on
the following page. Use this information to order replacements for lost or damaged decals. Be
sure to read all decals before operating the attachment. They contain information you need to
know for both safety and product longevity.
IMPORTANT:
Keep all safety decals clean and legible. Replace all missing, illegible, or damaged safety decals.
When replacing parts with safety decals attached, the safety decals must also be replaced. Safety decals are
available, free of charge, from your local dealer or Paladin.
REPLACING SAFETY DECALS
: Clean the area of application with nonflammable solvent, then wash the same
area with soap and water. Allow the surface to fully dry. Remove the backing from the safety decal, exposing the
adhesive surface. Apply the safety decal to the position shown in the diagram above and smooth out any bubbles.
# 50-0724
# RDL3102
SERIAL TAG
LOCATION
# 50-0769
# RDL3100
# RDL3100
# RDL3178
# RDL3102
# 50-0909
# 50-0737
# 50-0737
# 50-0769
# RDL3180
# 41204
# RDL3101
# 50-10017
# 40590
# RDL3178
Summary of Contents for FFC PREPARATOR LAF3566
Page 2: ......