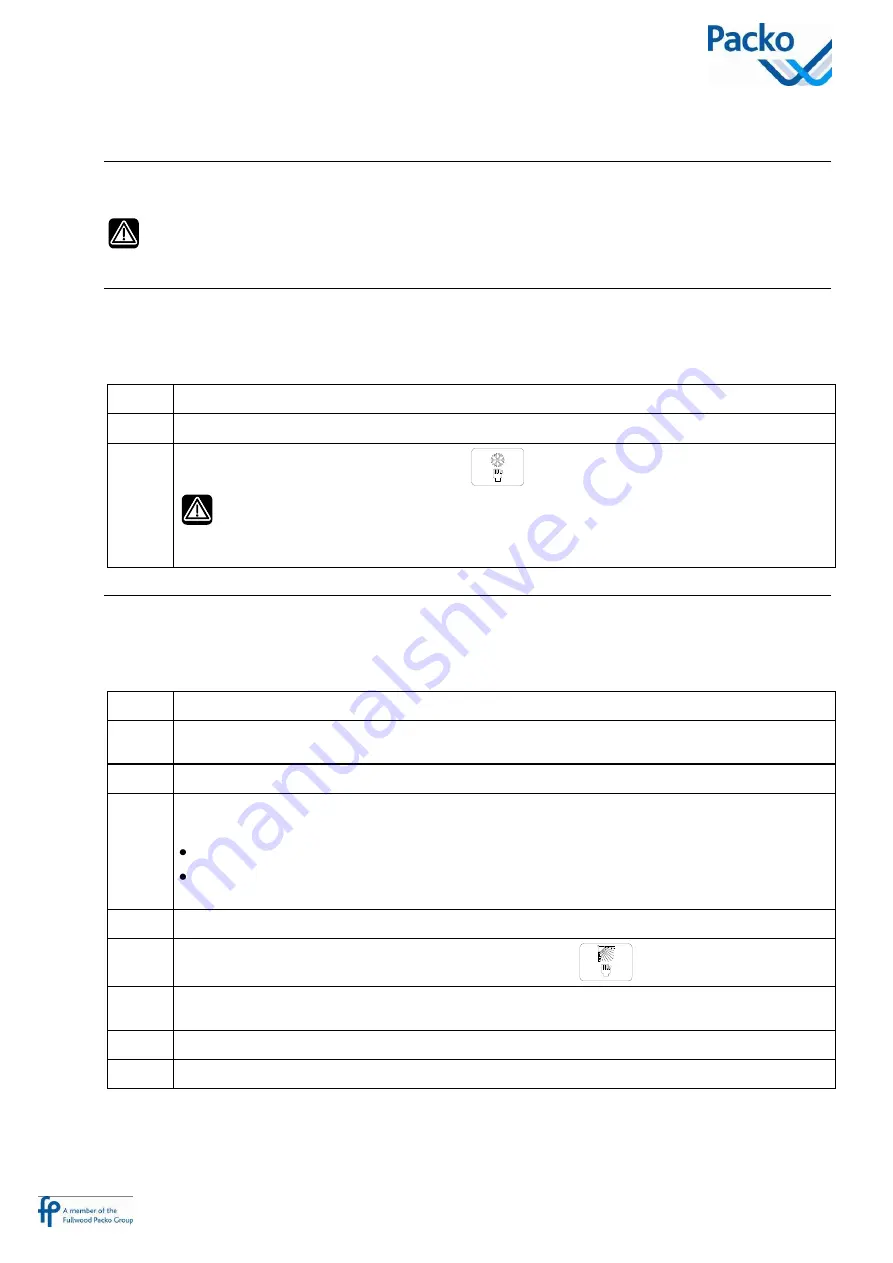
68/78
06/02/2008
1.00
Manual cooling and cleaning (option)
Warning
The manual cooling function is only to be used in case of a breakdown of all automatic functions and
under permanent supervision!
Manual cooling
Proceed as follows to start up manual cooling:
Step
Action
1
Remove the protective cover from the operator console.
2
Set the desired cooling time using the timer
.
Mind that the cooling will not stop automatically when the setpoint temperature is reached -
in DX tanks there is danger of freezing. Do not set too long a cooling time and regularly check
the milk temperature.
Manual cleaning
Proceed as follows to clean the tank manually:
Step
Action
1
Screw the wash cap to the milk outlet or attach the rubber connection from the cleaning pump to
the outlet.
2
Open the outlet valve.
3
Fill the tank with water via the manhole with ± 1% of its nominal volume. Depending on the
cleaning phase (see next page), use hot water and a cleaning agent.
Follow the instructions enclosed or on the packaging of the cleaning agent.
Make sure the alkaline cleaning agent is not too old. It should not be older than 6 months after
the purchase date
4
Close the manhole cover and check that the vent and the rubber plug are fitted.
5
Set the required circulation time (see next page) using timer
.
6
After the cleaning pump has stopped, open the outlet valve and remove the wash cap or the rubber
connection.
7
Empty the tank.
8
Repeat steps 1-7 for each of the cleaning phases stated on the next page.