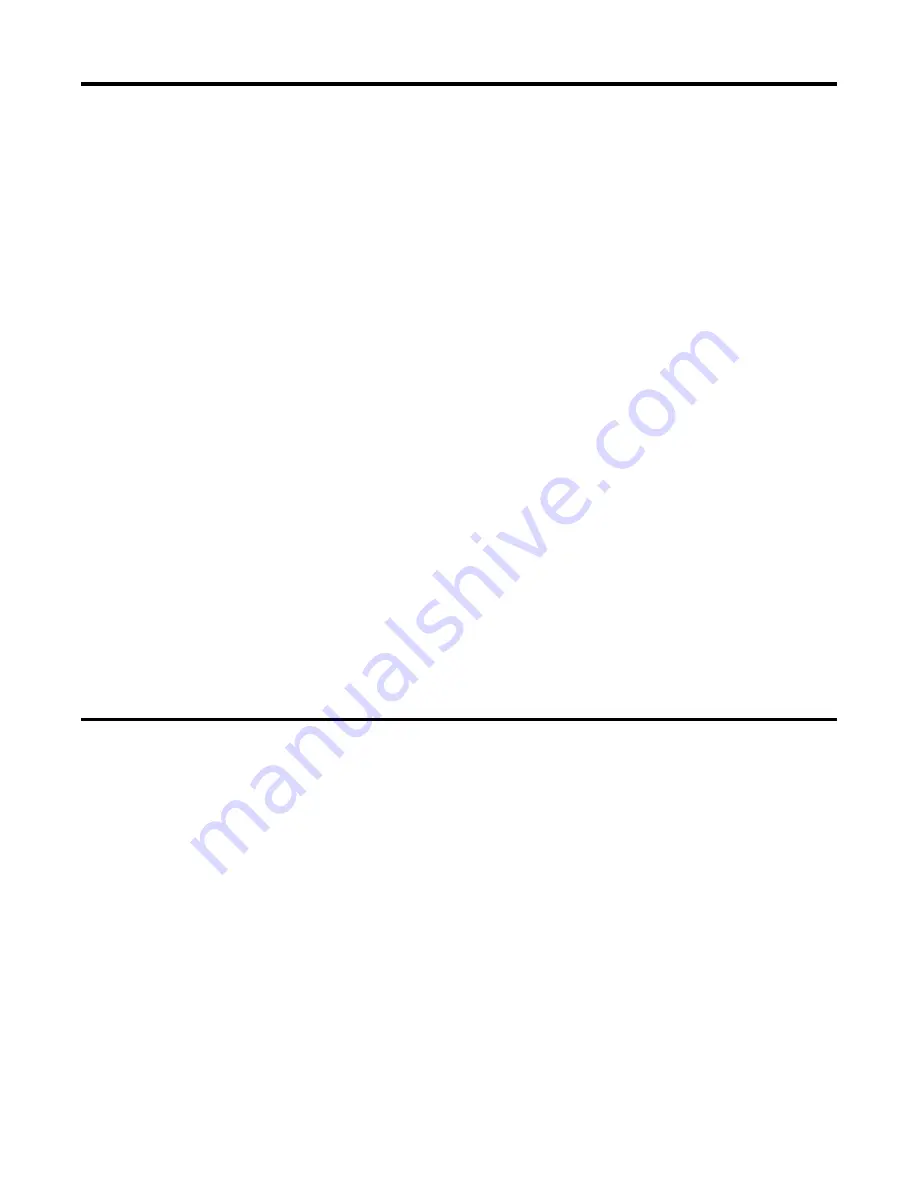
3
MAINTENANCE
Good maintenance procedures assure better operation,
fewer repairs and longer life to your machine.
DISCONNECT THE ELECTRICAL PLUG OF THE MA-
CHINE FROM THE ELECTRICAL OUTLET BEFORE
DOING ANY CLEANUP, REPAIRS OR MAINTENANCE
OF THE MACHINE AND WHEN LEAVING THE MACHINE
UNATTENDED.
CLEAN THE MACHINE AFTER EACH USE:
1.
Wipe the outside with a clean cloth
.
2.
Clean the collector tank
: Release the clamps on each side
of the tank and head assembly. Lift the head assembly off
and set aside. Lift the filter assembly out of the collector
tank and set aside. Then wipe the inside of the collector tank
with a clean cloth.
3.
Empty and check the filter assembly
: Empty the recovered
soilage into a suitable container and shake to remove clinging
dirt. Brush the outside of the filter bag to remove embedded
dirt. Check the filter assembly for tears or holes; repair or
replace if necessary. Install the clean filter assembly into the
clean collector tank.
ELECTRICAL CABLE:
Check the cord for any nicks, cuts or damage. Report these to
your supervisor for correction.
VACUUM HEAD ASSEMBLY:
1.
Gaskets
: Clean the vacuum head gasket and the float shut-off
gasket.
2.
Float Shut-Off Device
: This should move freely. Remove
any debris or strings from the float cage.
3.
Head Assembly
: Replace and leave ajar if the collector tank is
damp to prevent mildew.
WHEELS AND CASTERS:
Check these for cuts and nicks. Remove any strings or debris that
may restrict the free movement of the wheels. Wipe the treads
clean.
CARBON BRUSH INSPECTION:
Check for wear at six month intervals or every 600 hours of
operation. The carbon brushes must be replaced if worn shorter
than 3/8 inch.
OPERATING PROCEDURES
WARNING! For the safe operation of this machine follow
the instructions given in this booklet and the training given
by your supervisor. Failure to do so can result in personal
injury and/or damage to machine and property!
DO NOT OPERATE MACHINE IN AN EXPLOSIVE
ENVIRONMENT!
To prepare the machine for operation, make sure it is of the correct
voltage and properly assembled. If in doubt, ask your supervisor.
FOR DRY PICK-UP:
“Dry” refers to material such as dust, dirt, debris and dry foam
shampoo.
1.
Release the clamp on each side of the tank and head assembly.
Lift the head assembly off and set it aside.
2.
Then lift the cloth filter assembly out of the collector tank.
Clean the cloth filter if needed (reference the “Maintenance”
section).
3.
Empty the collector tank of all dust and debris. If the debris
is wet, empty and dry the inside of the tank thoroughly.
4.
Place the cloth filter assembly back into the collector tank.
Check for a good seal around the outer filter lip and tank rim.
5.
Replace the head assembly and fasten both clamps. Attach
the hose, wand and floor tool of choice (reference page 5).
6.
Plug the power cord into a 115-volt, 60 cycle grounded outlet.
7.
Turn the machine’s motor on by pressing the rocker switch
which is located on the head assembly.
WARNING! NEVER USE THIS MACHINE TO PICK UP
VOLATILE OR EXPLOSIVE MATERIALS.
FOR WET PICK-UP:
“Wet” refers to liquids such as water, scrub solutions and deter-
gents;
NOT
VOLATILE OR EXPLOSIVE MATERIALS
.
1.
Release the clamp on each side of the tank and head assembly.
Lift the head assembly off and set it aside.
2.
Then lift the cloth filter assembly out of the collector tank.
Store the filter assembly for future, dry pick-up use. DO
NOT REINSTALL.
3.
Empty the collector tank of all dust and debris. Also wipe
the inside of the collector tank to remove clinging dust.
4.
Check the float shut-off device on the lower portion of the
head assembly. The float should have free movement. When
the recovered liquid soilage reaches the collector tank capac-
ity, the float will rise to shut off the air flow, stopping the
liquid recovery. This prevents damaging overflow and signals
the operator when to empty the collector tank.
5.
Replace the head assembly and fasten both clamps. Attach
the hose, wand and floor tool of choice (reference page 5).
6.
Plug the power cord into a 115-volt, 60 cycle grounded outlet.
7.
Turn the machine’s motor on by pressing the rocker switch
which is located on the head assembly.