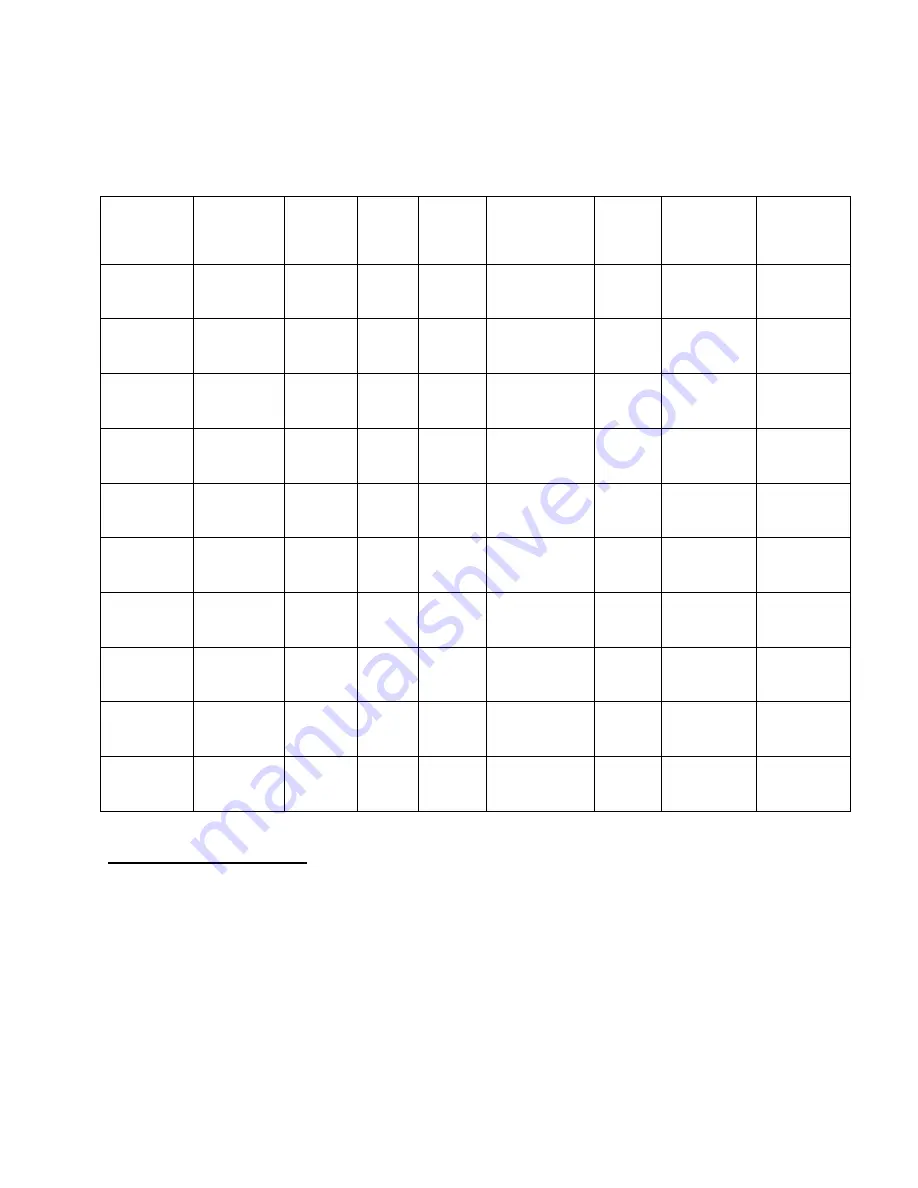
©2013 PACE Inc., Southern Pines, NC
Page 26 of 31
All Rights Reserved
Profile Log
Duplicate this page and complete the copied form.
DO NOT
fill out the copy in this manual.
PCB
Designation
Component
Process
(Remove
or
Install)
Mode
Profile
#
Set
Temperature
Blower
Speed
CycleTime
(sec.)
Preheating
Required
General Process Guidelines
Board Preparation
Prepare the land pattern as per your company specifications. The most widely used methods are as
follows:
1. Prefill - The PCB land pattern is prefilled using a soldering iron. Care must be taken to insure that
all lands are tinned with an equal deposition of solder (provides a uniform appearance).
2. Solder Paste - Apply an equal amount of solder paste on each land. Take care to insure that the
proper amount of paste is dispensed. If too much paste is applied, solder bridges will form
between the lands. If an insufficient amount of paste is applied, solder joint formation will be