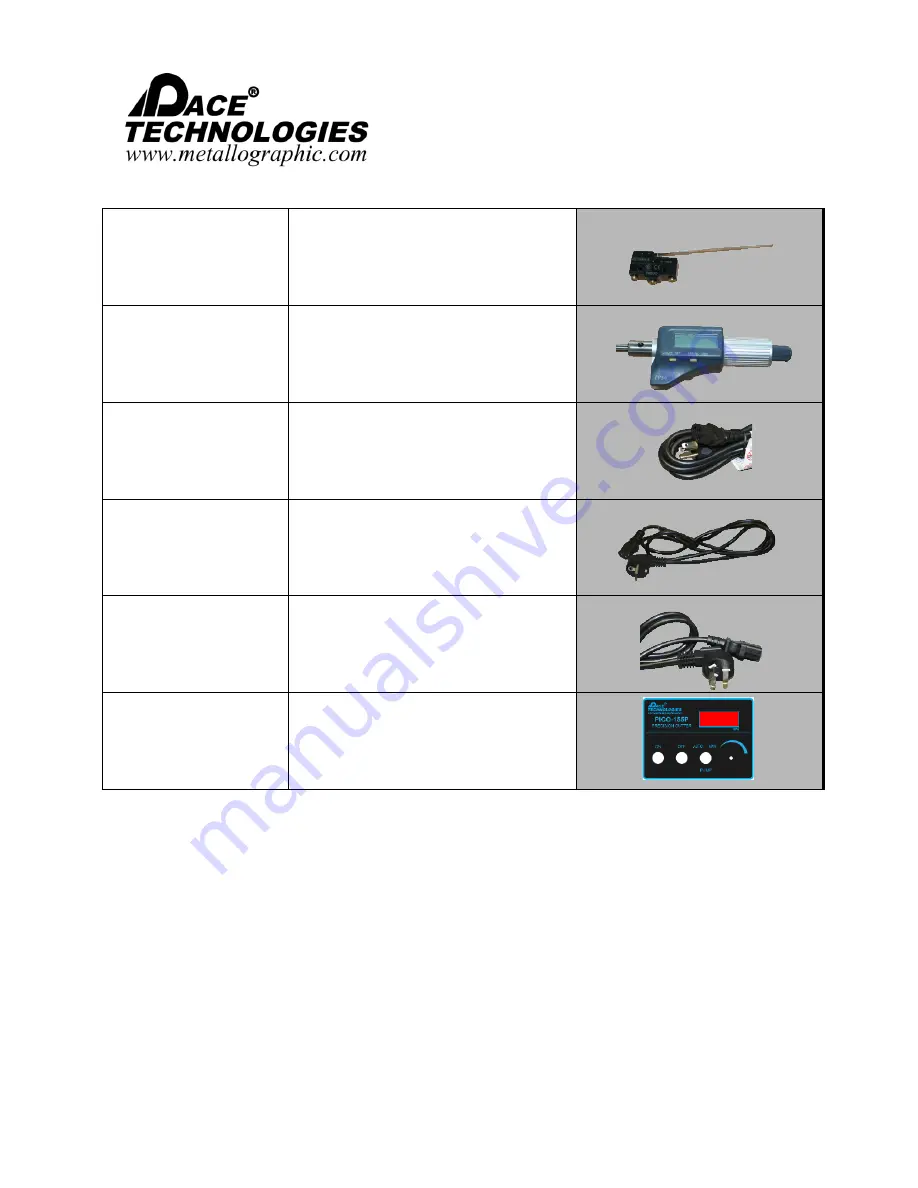
PICO 155P Precision Saw
I
NSTRUCTION
M
ANUAL
- - - - - - - - - - - - - - - - - - - - - - - - - - - - - - - - - - - - - - - - - - - - - - - - - - ▲
3601 E. 34th St. Tucson, AZ 85713 USA Tel. +1 520-882-6598 Fax +1 520-882-6599 email: [email protected] Web: http://www.metallographic.com
40
Please read this instruction manual carefully and follow all installation, operating and safety guidelines.
SWT-CUT-OFF
Contact Cut-Off Switch
P155-006
0’’-1’’ Micrometer
C-110V-001
Standard 110V USA Power Cable
C-220V-001
220V Round Pronged Cable
C-220V-002
220V Flat Pronged Cable
P155P-T
PICO 155P Template