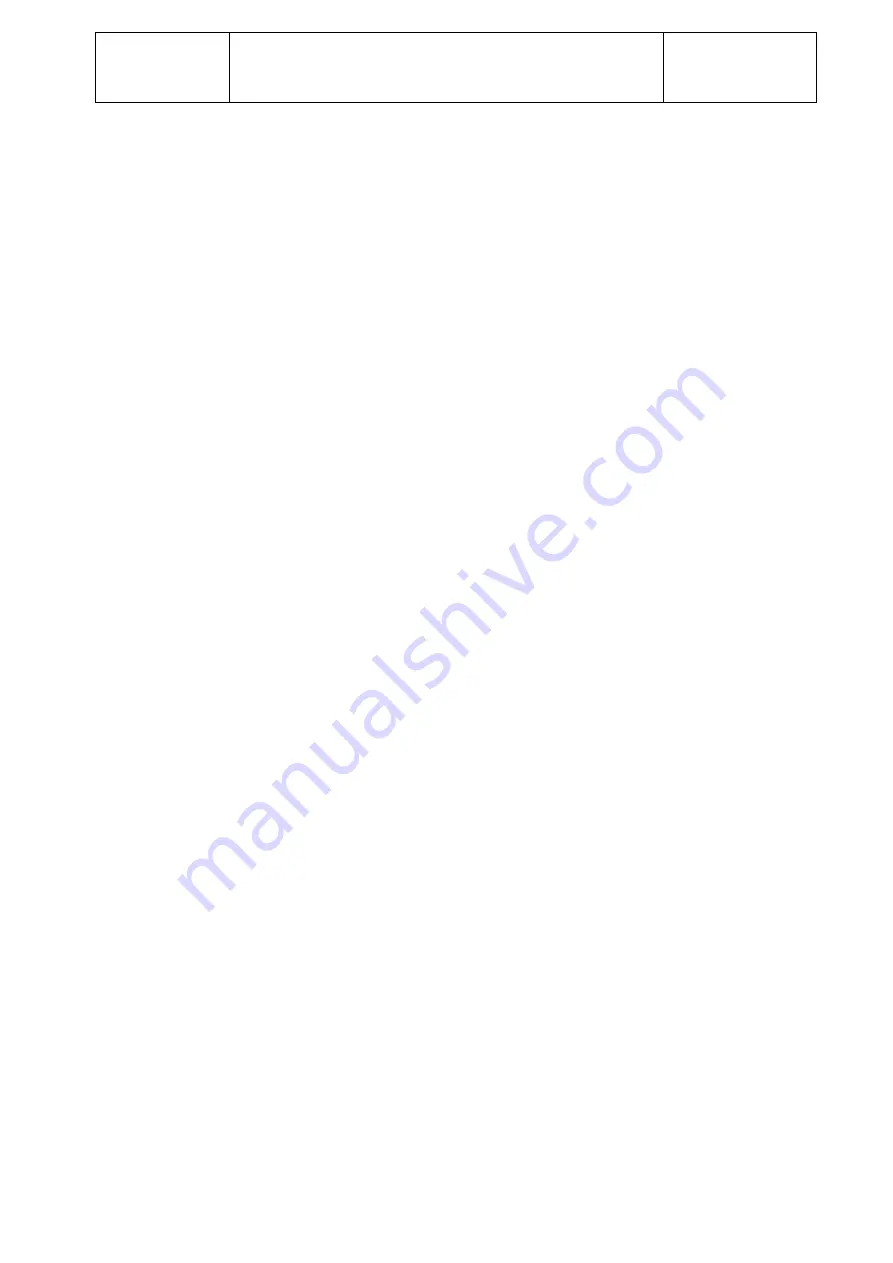
PA S.p.A.
USER MANUAL FOR WATER-DRIVEN ATEX TANK
CLEANERS
INGLESE
PQ02-A13
Revisione: 09
Del: 01/09/2016
Codice: PQ02-A13
Pagina 4 di 8
Each installation or reinstallation must be performed by qualified personnel, duly trained and informed on the
related risks, even concerning the instructions of this document.
When using the utensils do not apply excessive force rotation on the connections in the presence of a
potential explosive atmosphere.
The use of utensils in zone 0 and 20 is not permitted. The use of utensils in zone 1/21 and 2/22 is allowed
with particular instructions under the directive EN 1127-1
(2011)
and EN
13463-1:
2009
which have to be
known by the operator.
Installation errors can provoke deformation or structural collapse of the pipe connection, also a loss of fluid in
the ambient with all the consequences and risks of the case (emission of inflammable substances with
relative zoning in line with the standard
CEI
(Italian regulation)
– sealing loss.
Installation errors can compromise the regular movement with effective possibility of sparking
.
2.2. Nozzle Selection
The nozzles in numbers of 2 & 4 of High pressure washing type with straight jet, must be appropriate to the
flow & pressure in which they intend to operate (see Nozzles chart) bearing in mind that the pressure spec.
to consider in the choice is the one achieved by subtracting from the pressure value in the pump, the value
of the pressure loss determined by the delivery line and head. This last value can be obtained from the
diagram D3 of this manual. The nozzles must be made of material compatible with the directive
2014/34/UE
and category 1.
2.2.3. Filtering of Liquid
The fluid sent from the system to the head has to be filtered in order to prevent particles to slip through
causing malfunction and therefore frequent maintenance interventions. The recommended sealed filter has
to be at least 300 microns. The head is fitted with a filter of 550 microns which only has a safety function; we
recommend to clean it every 100/300 hours of functioning. In case of filter breakage, dismount the head,
clean it from any eventual internal residue and fit a new filter.
2.2.4. Connection & Setting
The head must be connected to a pressure application, usually fed by piston pumps, pressure washers and
similar; in order to prevent possible damage to persons and things, where such an application must be
equipped with all safety parts and control (like safety valves, regulating etc) foreseen by the directives in
force. Use a resistant and adequate sized tube for the connection, possibly avoiding narrow necks and
abrupt direction variations to restrain the pressure loss.
The head must be anchored firmly at the Tank opening or by an appropriate support. This type of head must
be held and fed by a fixed pipe that prevents any swinging.
The connecting tube to the head must be of such to help the fluid flow without any excessive pressure drop.
The assembler is compelled also to carry out the inspection of all the connection links.
The apparatus must be installed by the following procedure:
Assure that there is no obstacle placed between head and attachment; place a suitable gasket that
assures a seal age conform and a protection grade minimum IP54 for Gas and IP6X for powders.
Assure that the head is not under pressure and absolutely minus the Product to be contained should
it be either the origin of explosive atmosphere or the possibility of ignition by use of tools a/w sparks
from impacts or knocks. It is necessary to check the head condition either upon the first installation
and also the reinstallation phase, after inspection or maintenance and in any case after each time
the head has been dismounted from the Tank.
Insert the connection tubes (entry and exit) following a good technique and using acknowledged
components, adopting the foreseen clamping instructions.
During the insertment of the tubes, make an electrical earth link-up with a minimum cable size 4mm
observing the prescribed terms for equipotential connections.
Inspection after installation, to be carried out by the assembler or end user, in particular the perfect
coupling of usage at the various openings (keep to the limit levels of emission rated in the zoning
phase)