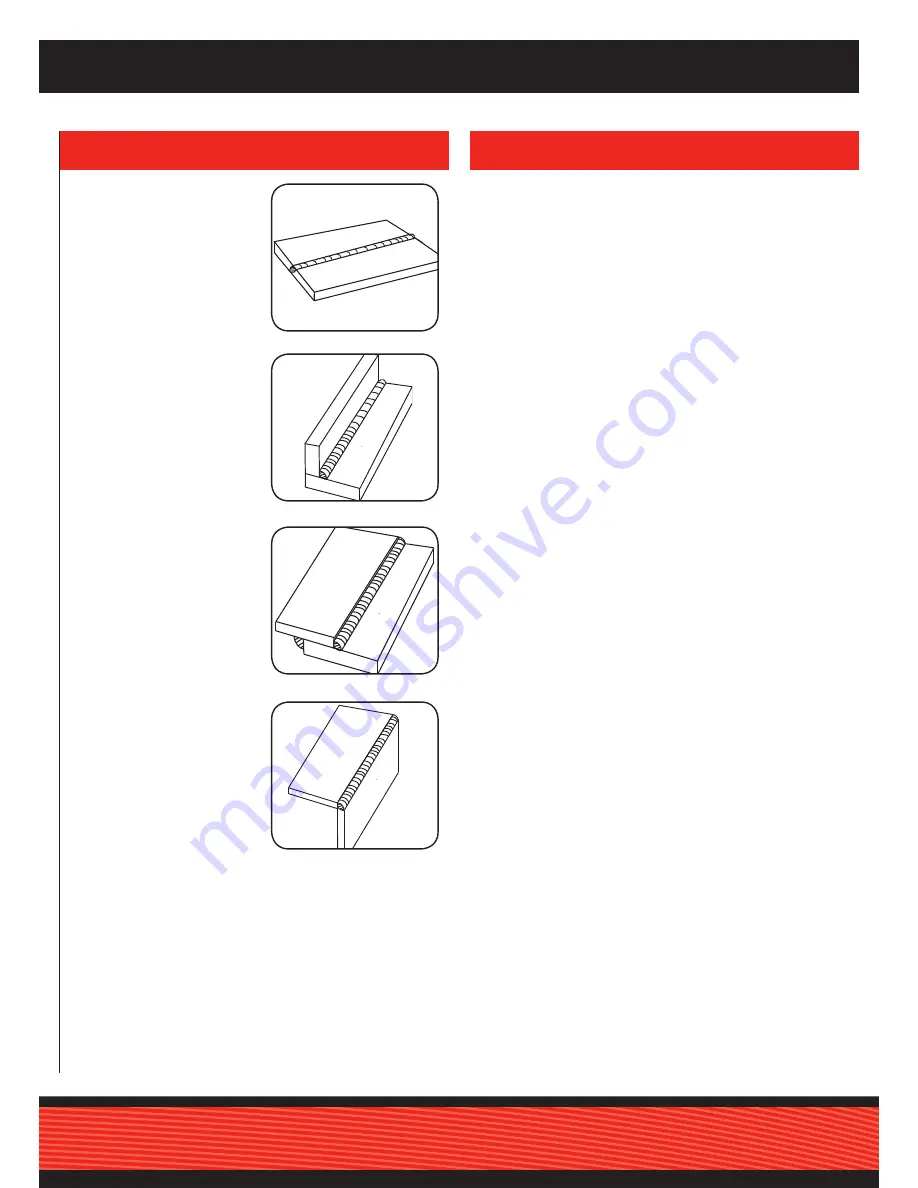
5. WELDING PROPERTIES
4. WELDED JOINTS
IWA-100
Arc Length
To strike the arc, the electrode should be gently scraped on the work until the arc
is established. A simple rule for the proper arc length; it should be the shortest
arc that gives a good surface to the weld. A very long arc produces a crackling
or spluttering noise and the weld metal comes across in large, irregular blobs
and gives a rough surface finish to the weld. A short arc is essential if a high
quality weld is to be obtained but a excessively short arc will cause sticking of the
electrode and result in poor quality welds.
Electrode Angle
The angle that the electrode makes with the work is important to ensure a
smooth, even transfer of metal. When welding in down hand, fillet, horizontal
or overhead the angle of the electrode is generally between 5 and 15 degrees
towards the direction of travel. When vertical up welding the angle of the
electrode should be between 70 and 80 degrees to the work piece.
Travel Speed
The electrode should be moved along in the direction of the joint being welded
at a speed that will give the size of run required. At the same time, the electrode
is fed downwards to keep the correct arc length at all times. Excessive travel
speeds lead to poor fusion and lack of penetration. While too slow a rate of
travel will frequently lead to arc instability, slag inclusions and poor mechanical
properties.
Electricity
The electricity flows through the electrode cable to the attached electrode. The
electricity will not leave the electrode unless it touches an earthed object.
Electricity always finds the fastest path to the earth. When the earth cable clamp
is connected to the metal work piece a direct earth connection is created back to
the welder. When the electrode makes contact with the earthed work piece an arc
is created. The electricity flows through the electrode, the metal work piece and
then through the earth cable straight back to the welder.
Earth Clamp
Prior to connecting the earth clamp it may be necessary to clean the surface of
the work piece using the metal brush. Attach the earth clamp firmly to the work
piece ensuring there is good metal to metal contact. Clamp it where it will not be
in the way. This clamp provides an earth connection back to the welder. Always
ensure the welder is disconnected from the power supply before attaching
electrodes into the holder.
Butt Joint
Is the joining of two pieces of
material together along a single
edge in a single plane. Two sheets
of metal are laid side-by-side and
joined together along a single joint.
Fillet Joint
Is a type of joint used for weld-
ing pieces or plates in which the
angle between them varies from
0
°
to 180
°
. The edge of one plate
is brought against the surface of
another not in the same plane. The
joint can be welded on one or both
sides.
Lap Joint
The edges of a plate are lapped
one over the other and the edge of
one is welded to the surface of the
other.
Corner Joint
A corner joint consists of two pieces
of material joined at their edges to
form an “L” shape.
ARC WELDING
Electrodes
Always store the electrodes in a dry place protecting them from moisture. Should
electrodes become damp or moist, bake them in an oven at 200 - 250˚C for 2
hours. Unless the electrodes are vacuum packed, basic coated electrodes will
always require such baking prior to use.
Metal arc welding electrodes consist of a core wire surrounded by a flux coating.
The flux coating is applied to the core wire by an extrusion process.
The coating on arc welding electrodes has a number of purposes:
•
To provide a gaseous shield for the weld metal, and preserve it from
contamination by the atmosphere whilst in a mol ten state.
•
To give a steady arc by having ‘arc stabilisers’ present, which provide a bridge
for current to flow across.
•
To remove oxygen from the weld metal with ‘deoxidised’.
•
To provide a cleansing action on the work piece and a protective slag cover
over the weld metal to prevent the formation of oxides while the metal is
solidifying. The slag also helps to produce a bead of the desired contour.
•
To introduce alloys into the weld deposits in special type electrodes.