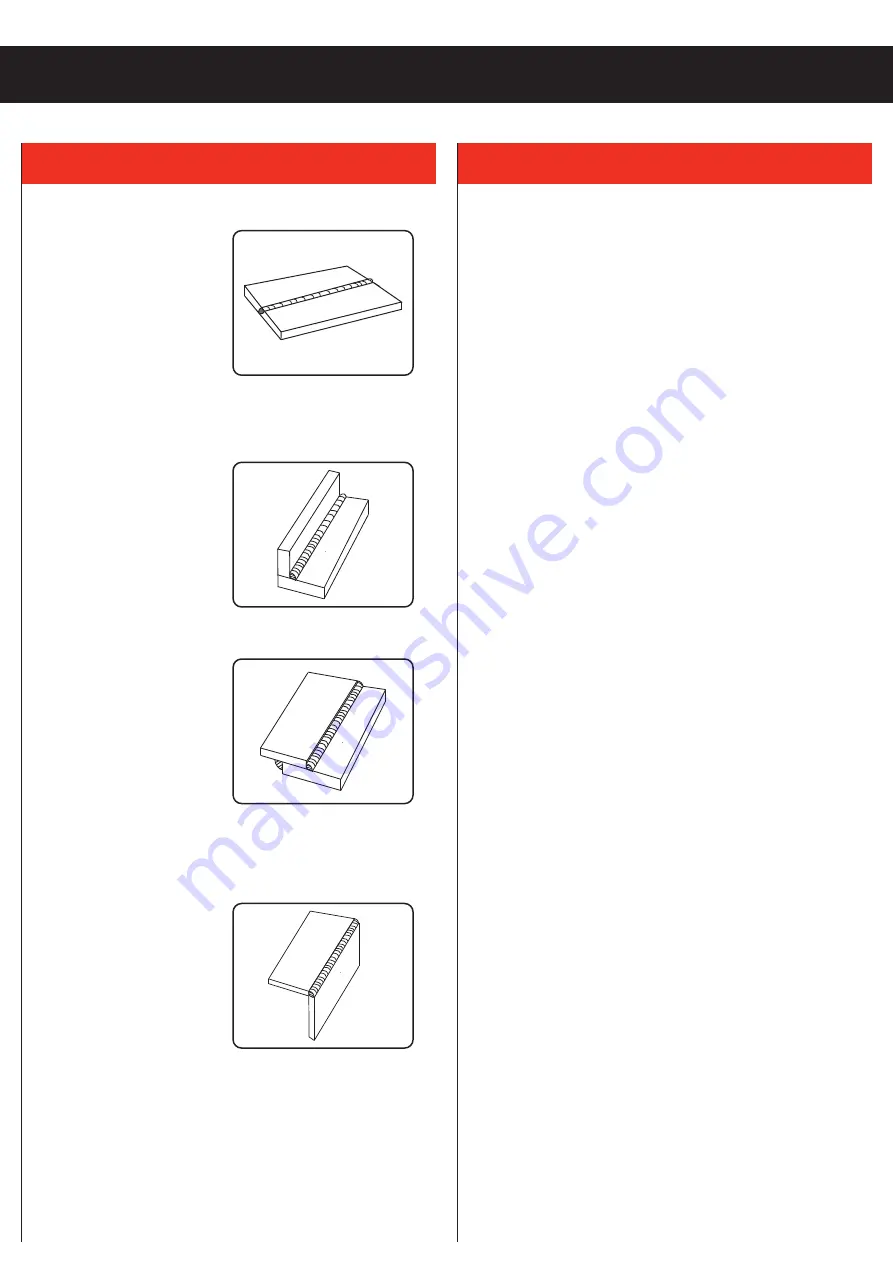
Electrodes
Always store the electrodes in a dry place protecting them from
moisture. Refer to the electrode manufacturer’s instructions for
proper storage and use.
Metal arc welding electrodes consist of a core wire surrounded by
a flux coating. The flux coating is applied to the core wire by an
extrusion process.
The coating on arc welding electrodes has a number of purposes:
• To provide a gaseous shield for the weld metal, and preserve it
from contamination by the atmosphere whilst in a mol ten state.
• To give a steady arc by having ‘arc stabilisers’ present, which
provide a bridge for current to flow across.
• To remove oxygen from the weld metal with ‘deoxidised’.
• To provide a cleansing action on the work piece and a
protective slag cover over the weld metal to prevent the
formation of oxides while the metal is solidifying. The slag also
helps to produce a bead of the desired contour.
• To introduce alloys into the weld deposits in special type
electrodes.
Arc Length
To strike the arc, the electrode should be gently scraped on the
work until the arc is established. A simple rule for the proper arc
length; it should be the shortest arc that gives a good surface to
the weld. A very long arc produces a crackling or spluttering noise
and the weld metal comes across in large, irregular blobs and
gives a rough surface finish to the weld. A short arc is essential
if a high quality weld is to be obtained but a excessively short arc
will cause sticking of the electrode and result in poor quality welds.
For down hand welding is to have an arc length no greater than
the diameter of the electrode.
Electrode Angle
The angle that the electrode makes with the work is important to
ensure a smooth, even transfer of metal. When welding in down
hand, fillet, horizontal or overhead the angle of the electrode is
generally between 5 and 15 degrees towards the direction of
travel. When vertical up welding the angle of the electrode should
be between 70 and 80 degrees to the work piece.
6. COMMON WELDS
7. WELDING TIPS
Butt Joint
Is the joining of two pieces of
material together along a single
edge in a single plane. Two
sheets of metal are laid side-by-
side and joined together along a
single joint
Fillet Joint
Is a type of joint used for welding
pieces or plates in which the
angle between them varies from
0° to 180°. The edge of one plate
is brought against the surface of
another not in the same plane.
The joint can be welded on one
or both sides.
Lap Joint
The edges of a plate are lapped
one over the other and the edge
of one is welded to the surface of
the other.
Corner Joint
A corner joint consists of two
pieces of material joined at their
edges to form an “L” shape.