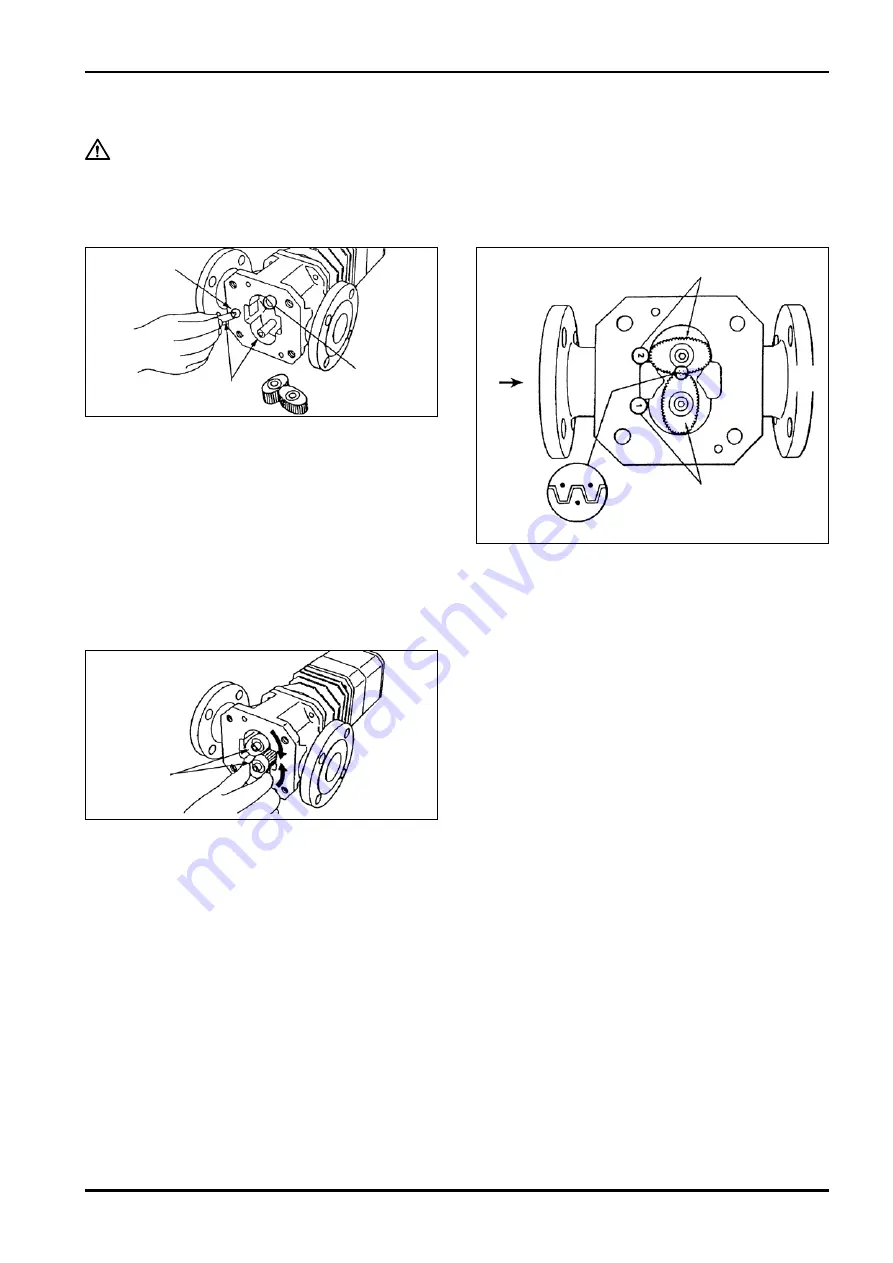
B-144-12-E
23
10.4 Sizes 52, 53, 55, 56, and 57 Meter Body Assembly Procedure
PRECAUTIONS BEFORE ASSEMBLY
Oval rotors, inner walls of the rotor shafts, inner wall of the measuring chamber, inlet
and outlet ports, and inner surface of the rear cover should be thoroughly washed clean,
completely removing dust, grime and other foreign matter.
①
Rotor Shaft Installation
The non-turn pin end of each rotor shaft faces
the register (bottom of the measuring chamber).
Install the shafts, pin end first, into their sockets
on the bottom of measuring chamber (bottom of
meter body), forcing downward while turning each
of them with hands until they are firmly installed in
position.
(Air in the socket may resist to be compressed by
the shafts. So good practice is to hold the shafts
pressed down by hand for some time.)
②
Rotor Installation
Rotor installation is correct if the sides where
signal generating magnets are embedded face
the register (bottom of the measuring chamber)
and the sides with match marks (
・
) (
・・
) face
the rear cover. Carefully install the rotors with the
1st rotor (match mark "
・
") on the shaft with "1"
stamped on the outside of measuring chamber
and the 2nd rotor (match mark "
・・
") on the shaft
with "2" stamped. Ensure that the match marks
are in alignment as shown in the inset.
③
Confirming the Rotor Gear Engagement
Hand rotate the rotors to make sure of correct
gear mesh. At this point, they may be shaky more
or less with the shafts not fixed firmly. Exercise
care not to damage the rotors and inner wall of the
measuring chamber by forcing them to rotate.
Rotors
Non-Turn Pin
Rotors
Shaft Soket
Rotor Shafts
1st Rotor
"1" Marks
Match Marks
IN
Flow
2nd Rotor
"2" Marks
OUT