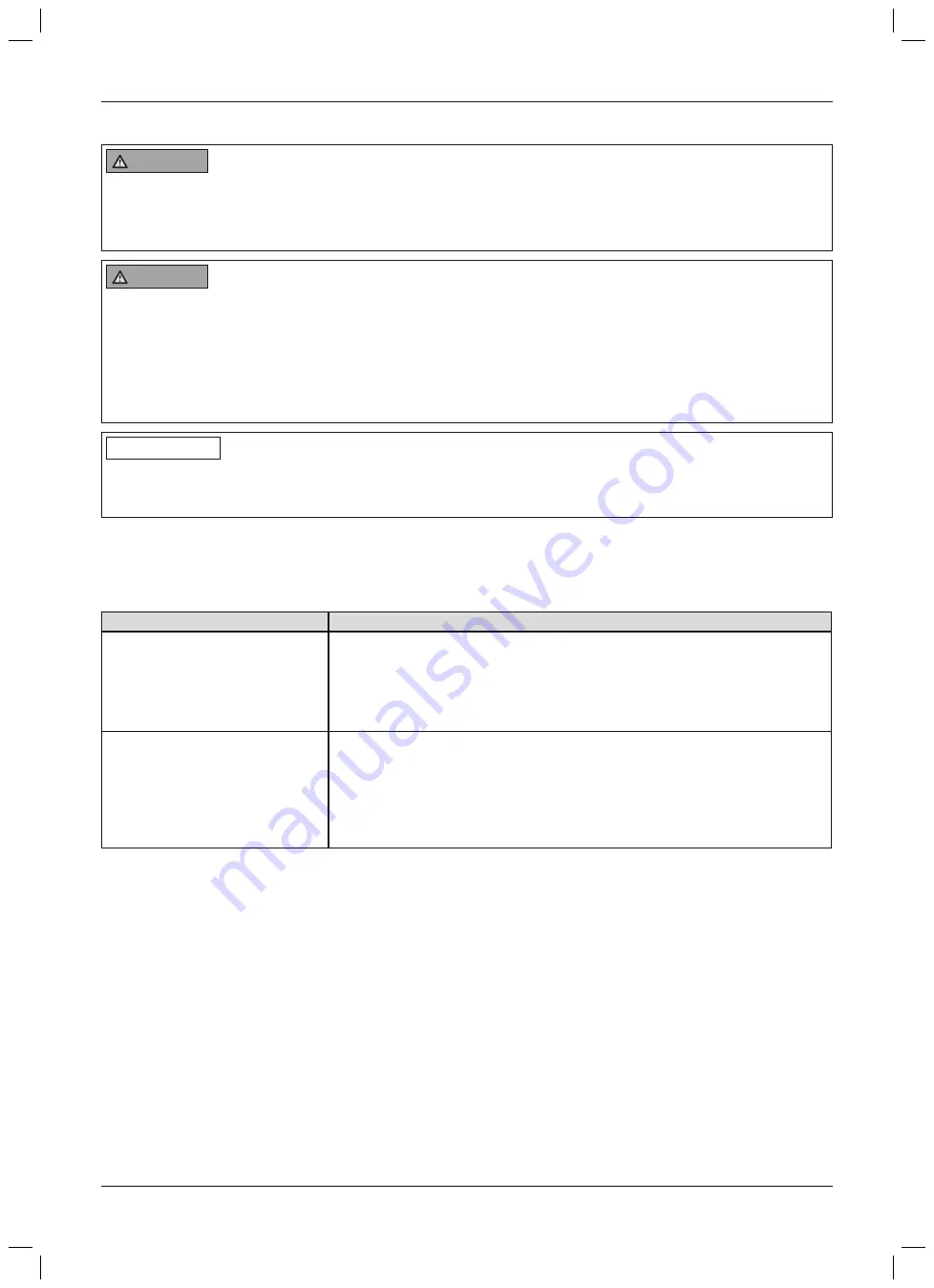
6.2 Adjusting the drive wheels
WARNING
Lack of fine adjustment of the drive wheels
Tipping over, falling of the user due to incorrect adjustment
►
Check the standard adjustments of the wheelchair for stability against tipping and function of the drive
wheels. Avoid any extreme settings.
WARNING
Incorrectly adjusted wheelbase
Tipping over, falling of the user due to unstable settings
►
Please note that with the drive wheel in a more forward mounting position and with an unfavourable body pos
ition, the user may tip backwards even on level ground.
►
Use an anti-tipper for inexperienced users and with extreme settings of the drive wheel.
►
Be sure to position the drive wheels towards the rear for transfemoral amputees. This improves the stability of
the wheelchair.
INFORMATION
Changing the drive wheel position can also change the angle between the caster wheel journal and the ground.
However, this must always be
approx. 90°
and thus readjusted accordingly. The knee lever wheel lock also has
to be readjusted.
6.2.1 Setting the drive wheels horizontally
The horizontal position of the drive wheels can be changed by horizontally moving the drive wheel adapter in the
frame.
Changing the drive wheel position has the following effects:
Position of drive wheel
Effects
Move backwards (passive setting) •
Larger wheelbase
•
Larger turning circle
•
Greater stability of the wheelchair
•
Wheelchair is harder to tip backwards when crossing obstacles
•
Position recommended for inexperienced users
Move forwards (active setting)
•
Smaller wheelbase
•
Less load on caster wheels = greater manoeuvrability
•
Less stability of the wheelchair
•
Wheelchair is easier to tip backwards when crossing obstacles
INFORMATION: An anti-tipper should be installed if necessary.
•
Setting recommended only for experienced users
The drive wheel can be installed at 6 depth positions in the drive wheel adapter (see fig. 36, item A–F).
1) Remove the wheels.
2) Loosen the Allen head screws on the drive wheel adapter (see fig. 1, item 1).
3) Move the drive wheel adapter to the desired bore hole (see fig. 1, item 2).
4) Check the depth setting. Both sides must be positioned exactly the same. Readjust if necessary.
5) Tighten the Allen head screws on the drive wheel adapter to
10 Nm
(see fig. 1, item 1). Put on the protective
cap.
6)
If necessary:
Readjust the height and alignment of the caster attachment device as well as the wheel locks
(see information at the start of the section).
9
Avantgarde XXL 2
Settings
Summary of Contents for Avantgarde XXL 2
Page 1: ...Avantgarde XXL 2 Instructions for use qualified personnel 3 ...
Page 2: ...2 Avantgarde XXL 2 ...
Page 28: ...Avantgarde XXL 2 28 ...
Page 29: ...29 Avantgarde XXL 2 ...
Page 30: ...Avantgarde XXL 2 30 ...