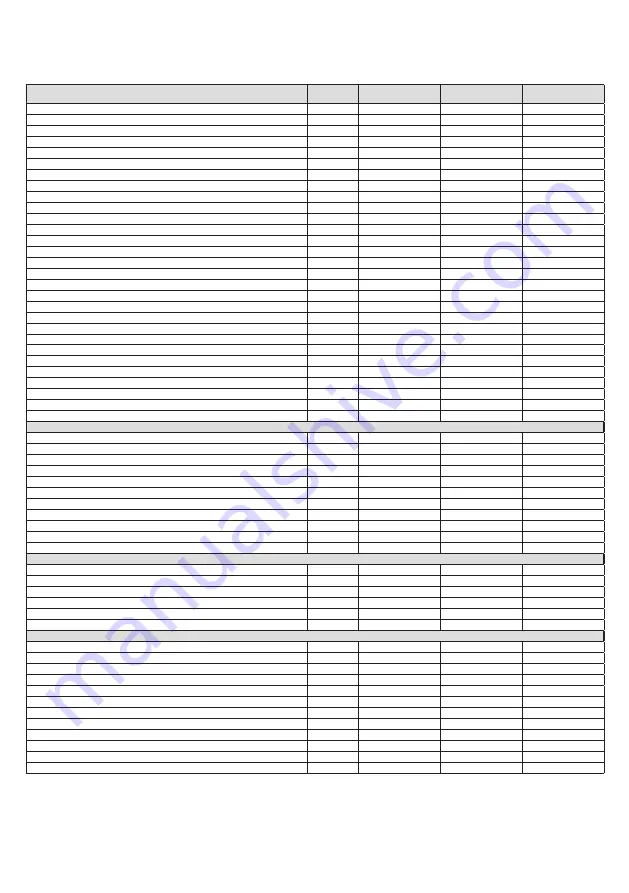
24
8. TECHNICAL DATA
Description
Unit
DTC 200
DTC 250
DTC 300
Part number
No.
10211600
10211700
10211800
Product number
GTIN
7070644004385 7070644004392 7070644004408
Actual capacity of the water tank at 20°C
L.
191
242
281
Outer diameter of the tank
mm
595
595
595
Height of the appliance
mm
1270
1540
1750
Gross weight of the appliance
kg
49
57
63
Net weight of appliance
kg
45.5
53
58
Net weight of appliance once filled with sanitary water
kg
237
298
340
Material of tank and integrated heat exchanger
-
1.4521 / 1.4521
1.4521 / 1.4521
1.4521 / 1.4521
Material of element
-
Incoloy 825
Incoloy 825
Incoloy 825
Thermal insulation material
-
PUR + VIP
PUR + VIP
PUR + VIP
Thermal insulation of the tank, average thickness
mm
50
50
50
IP classification
IP
21
21
21
Standby heat losses / 24 hour
kWh/24h
1.18
1.30
1.39
Standby heat losses
Watts
49.0
54.0
58.0
Hot water capacity - mixed to 40°C
L.
312
385
416
Heating time (upper coil)
min.
21.5
27.4
30.7
Reheat time (1) (70%) (upper coil)
min.
16.1
20.6
23.6
Primary Heating Power (1) (upper coil)
kW
17.9
17.0
16.3
Heating time /Lower/Solar coil)
min.
34.1
45.4
51.8
Reheat time (1) (70%) (Lower/Solar coil)
min.
23.9
31.8
36.3
Dedicated Solar volume
l.
94
104
104
Primary Heating Power (1) (Lower/Solar coil)
kW
16.9
16.0
15.2
Primary flowrate for Reheat time and primary heating power
l/h
900
900
900
Primary Heat exchanger pressure drop (1)
mBar
50
50
50
Solar Heat exchanger pressure drop (1)
mBar
50
50
50
Heat up time element
min.
138
196
246
Reheat time (1) (70%) 1 element
min.
97
137
172
ErP class
Rating
B
B
B
Pressure information
Maximum design pressure of cylinder (rated pressure)
MPa/Bar
1 / 10
1 / 10
1 / 10
Maximum design pressure of heating coil
MPa/Bar
1 / 10
1 / 10
1 / 10
Maximum design pressure of solar coil
MPa/Bar
1 / 10
1 / 10
1 / 10
Operating pressure of cylinder
MPa/Bar
3.0
3.0
3.0
Operating pressure of heating coil
MPa/Bar
2.5
2.5
2.5
Operating pressure of solar coil
MPa/Bar
2.5
2.5
2.5
Max. operating temperature of cylinder
°C
70
70
70
Max. operating temperature of heating coil
°C
99
99
99
Max. operating temperature of solar heating coil
°C
99
99
99
Expansion solution
-
Aquasystem 3 Bar Aquasystem 3 Bar Aquasystem 3 Bar
Expansion vessel capacity
l.
18
24
24
Heat Exchanger information
Primary heat exchanger volume
l.
3.8
3.8
3.8
Primary heat exchanger surface area
m²
0.69
0.69
0.69
Ø int. et Ø ext.
mm/mm
ø20.4 / ø22
ø20.4 / ø22
ø20.4 / ø22
Solar heat exchanger volume
l.
3.8
3.8
3.8
Solar heat exchanger surface area
m²
0.69
0.69
0.69
Ø int. et Ø ext.
mm/mm
ø20.4 / ø22
ø20.4 / ø22
ø20.4 / ø22
Hydraulic connections
Secondary return
mm
1/2”
1/2”
1/2”
Primary heat exchanger flow
Inch
3/4”
3/4”
3/4”
Primary heat exchanger return
Inch
3/4”
3/4”
3/4”
Solar heat exchanger flow
Inch
3/4”
3/4”
3/4”
Solar heat exchanger return
Inch
3/4”
3/4”
3/4”
Cold water
Inch
3/4”
3/4”
3/4”
Hot water
Inch
3/4”
3/4”
3/4”
Immersion heater
Inch
5/4”
5/4”
5/4”
Expansion Relief Valve
Inch
1/2”
1/2”
1/2”
T&P valve (factory fitted)
Inch
1/2”
1/2”
1/2”
Pressure reducing valve
Inch
3/4”
3/4”
3/4”
Temperature sensor sleeve diameter
mm
8
8
8
8.1 Data table Delta DTC
Summary of Contents for Delta Twincoil DTC 200
Page 26: ...26 NOTES ...