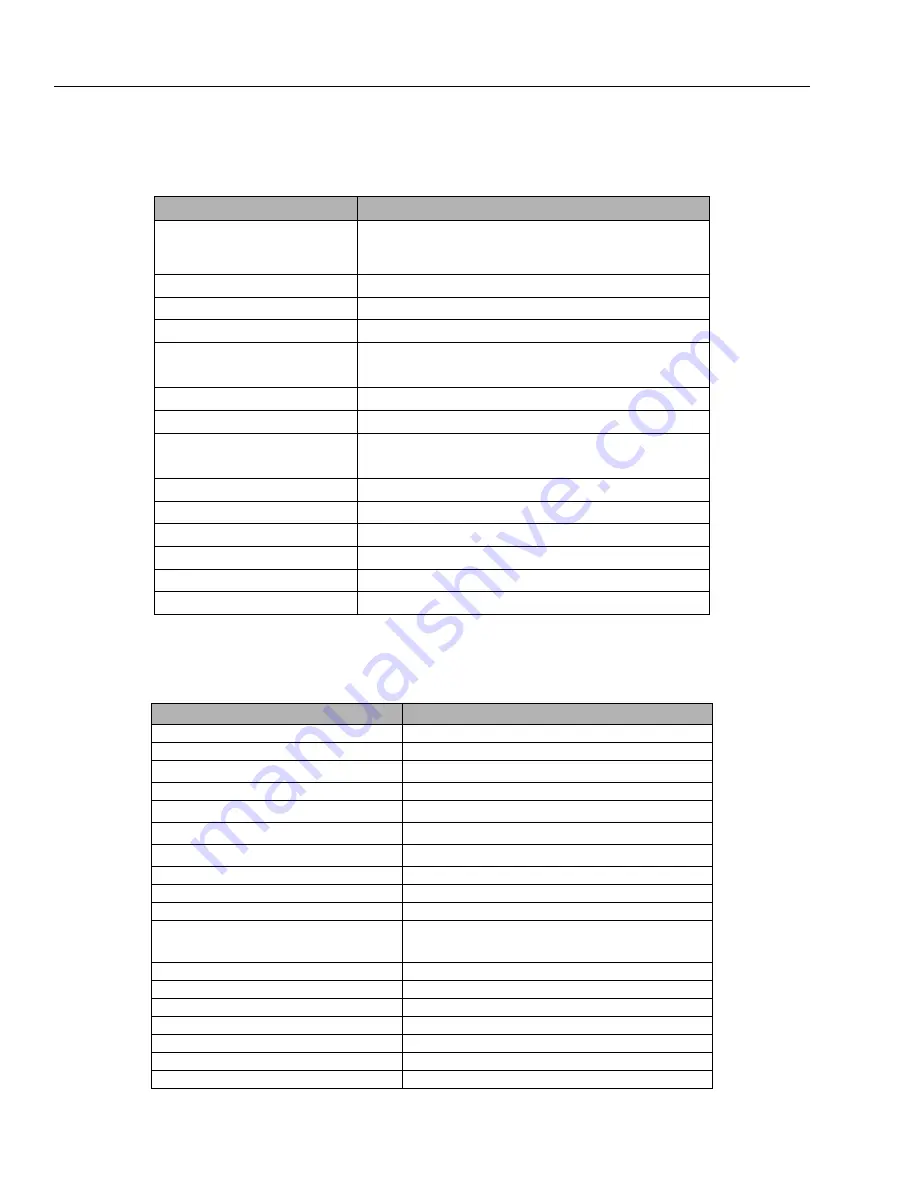
SECTION 1 - SPECIFICATIONS
1-4
– JLG Lift –
3121623
Honda Engine iGX390 Specifications
Honda Engine iGX440 Specifications
Table 1-6. Specifications Honda Engine iGX390
Model
iGX390
Engine type
Air cooled 4-stroke OHV petrol engine,
25° inclined cylinder, horizontal shaft, cast
iron sleeve
Bore x stroke
88 x 64 mm
Displacement
389 cm3
Compression ratio
8.2 : 1
Net power
6.4 kW (8,6 HP) / 3 000 rpm
7.0 kW (9.4 HP) / 3 600 rpm
Max. net torque
26.5 Nm / 2.7 kgfm / 2 500 rpm
Ignition system
Digital CDI with variable ignition timing
Starting system
Recoil starter,
Electric starter
Choke
Automatic
Fuel tank capacity
6.1 l
Fuel cons. at cont. rated power
3.5 L/hr - 3 600 rpm
Engine oil capacity
1.1 l
Dimensions (L x W x H)
409 x 484 x 448 mm
Dry weight
37,0 kg
Table 1-7.
Specifications Honda Engine iGX440
Model
iGX440U
Description code
GCAWK
Type
4-stroke, overhead camshaft, single cylinder, inclined by 15°
Displacement
438 cm
3
(26.7cu-in)
Bore x stroke
88.0 x 72.1 mm (3.46 x 2.84 in)
Maximum horsepower
11.2 kW (15.2 HP) / 3,600 min
-1
(rpm)
Recommended maximum operation bhp
8.0 kW (10.8 HP) / 3,600 min
-1
(rpm)
Maximum torque
29.8 N·m (3.0 kgf·m, 22 lbf·ft)/2,500 min
-1
(rpm)
Compression ratio
8.1 : 1
Minimum fuel consumption
328 g/kW·h (241 g/HP·h, 0.53 lb/HP·h)
Ignition system
CDI
Ignition timing (at no load)
10° B.T.D.C./1,400 min
-1
(rpm)
13° B.T.D.C./3,600 min
-1
(rpm)
Spark plug
BKR7E-E (NGK), K22PR-UR (DENSO)
Lubrication system
Forced splash type
Oil capacity
1.10 l (1.16 US qt, 0.97 lmp qt)
Cooling system
Forced air
Starting system
Recoil and starter motor
Stopping system
Ignition primary circuit open
Carburetor
Horizontal type batter fly valve
Go
to
Discount-Equipment.com
to
order
your
parts