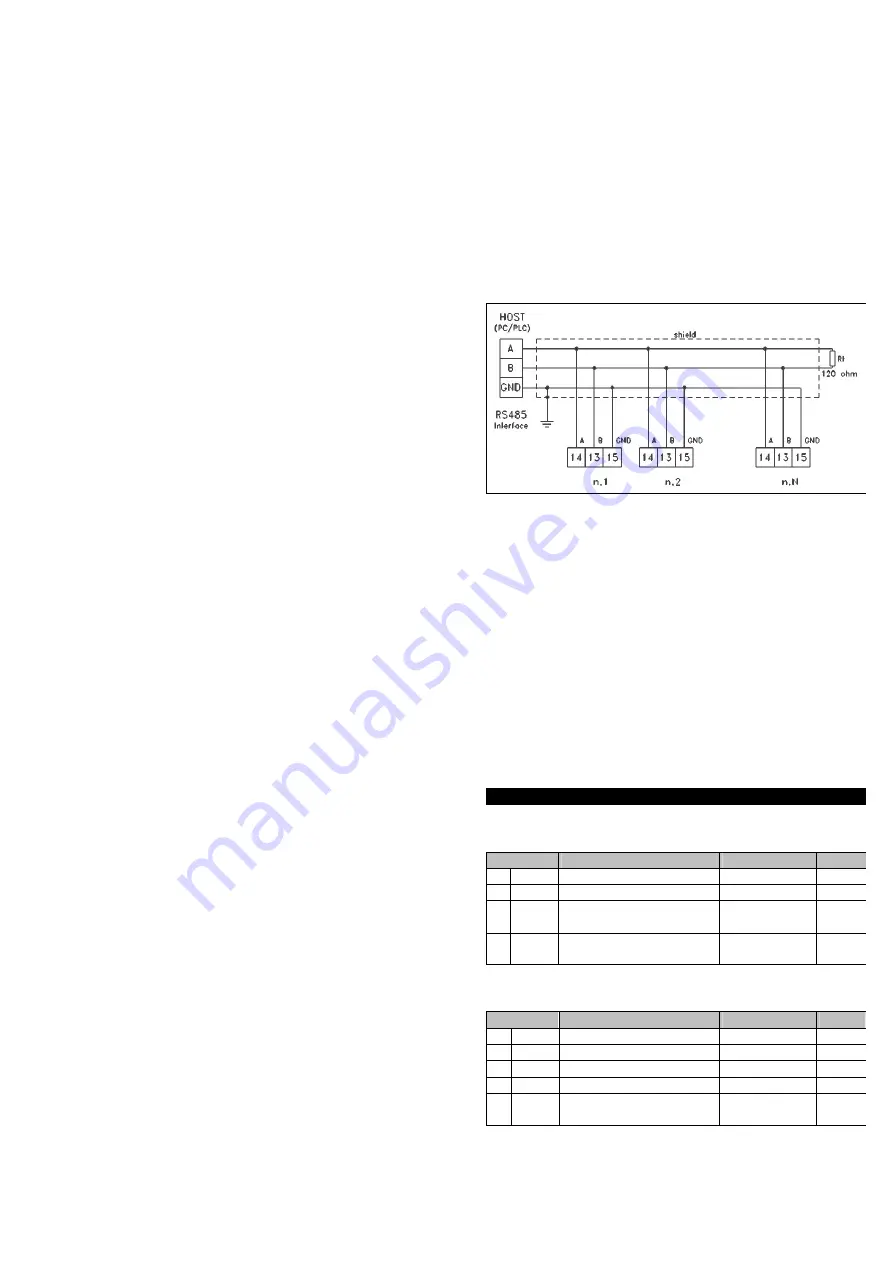
OSAKA OPERATING INSTRUCTIONS –COC 30- Page
8
These commands have a bistable function, which means that
at the first command the AUX output is activated whereas on
the second it is deactivated.
In this mode, the AUX output can also be switched off
automatically after a certain time that can be set under the “
AO
t” parameter.
With "AOt" = 0 the output is only activated and deactivated
manually, using the DOWN/AUX key or the digital input.
= 5 – mutable alarm: the AUX output is activated together with
the buzzer when alarm conditions exist and, like the buzzer, it
can be muted by pressing any key.
= 6 – non-mutable alarm: the AUX output is activated when
alarm conditions exist and remains activated for as long as
such conditions persist.
4.8 – DIGITAL INPUTS
The instrument has three settable digital inputs for free voltage
contacts.
All the digital input setting parameters are contained in the
“
]
In”
group.
The function logic of the digital inputs is established by the
parameters
“i1L”, “i2L”, “i3L”
, which can be programmed as
follows:
= On – contact normally open: the programmed function occurs
on the closure of the contact connected to the input.
= OFF – contact normally closed: the programmed function
occurs on the opening of the contact connected to the digital
input.
The action of the digital inputs can be delayed using the
following parameters:
“i1d”, “i2d”, “i3d”
, which can be programmed in seconds.
With regards to operation, the digital input acts according to
the
"i1F", “i2F”, and “i3F”
parameters, which can be
programmed as:
= 0 – not operative
= 1 – external alarm signal: on input intervention, the alarm is
activated and the upper display alternately shows
"ALn"
(where n is the number of the digital input) and the temperature
measured.
= 2 – Remote control of auxiliary output AUX: the digital input
is used to command the auxiliary output AUX as described in
operation mode "AOF" = 4 of the auxiliary output
= 3 – Steam injection remote control: the digital input operates
as the instrument’s INJ key.
= 4 – Steam injection block: the intervention of the digital input
causes steam injection blockage. The function can be useful if
the instrument does not have the steamer probe and one
wishes to block injection by means of a steamer thermostat.
= 5 – Pulse command for switching on the extractor output for
multiple command. This can be used to facilitate the command
of the single extractor when more than one appliance is fitted
to an oven. If one desires to command a single extractor from
a number of instruments, it is possible to do so by
programming the former with “ECn”=OFF and all the others
with “ECn” =On, connecting the EXTR relay output of the
former in such a way that it commands the extractor,
connecting the EXTR relay outputs of all the others in parallel
and therefore at the digital input of the former, which will have
suitably programmed the digital input with this operation mode.
4.9 - RS 485 SERIAL INTERFACE
The instrument can be equipped with a RS 485 serial
communication interface, by means of which it is possible to
connect the regulator with a net to which other instruments
(regulators of PLC) are connected, all depending typically on a
personal computer used as plant supervisor. Using a personal
computer it is possible to acquire all the function information
and to program all the instrument’s configuration parameters.
The software protocol adopted for COC is a MODBUS RTU
type, widely used in several PLC and supervision programs
available on the market (COC series protocol manual is
available on request).
The interface circuit allows the connection of up to 32
instruments on the same line.
To maintain the line in rest conditions a 120 Ohm resistance
(Rt) must be connected to the end of the line.
The instrument is equipped with two terminals called A and B
which have to be connected with all the namesake terminals of
the net.
For the wiring operation they must be interlaced with a double
cable (telephonic type) and all the GND terminals must be
connected to the ground.
Nevertheless, particularly when the net results very long or
noised and being present potential differences between the
GND terminals, it is advisable to adopt a screened cable wired
as in the drawing.
if the instrument is equipped with a serial interface, the
parameters to be programmed are the following, all present in
the parameters group
“
]
SE”
:
"Add"
: Address of the station. Set a different number for each
station, from 1 to 255.
"bau"
: Transmission speed (baud-rate), programmable from
2400 to 38400 baud. 1 =2400 baud, 2 =4800 baud, 3 =9600
baud, 4= 19200 baud , 5 =38400 baud. All the stations have to
have the same transmission speed.
"PAC"
: Programming access. If programmed as "LoC" this
means that the instrument is only programmable from the
keyboard, if programmed as "Lor" it is programmable both from
the keyboards and serial line.
If an attempt is made to enter the programming from the
keyboard whilst a communication through the serial port is in
progress the instrument will visualise
"bSy"
to indicate the
busy state.
5 – PROGRAMMABLE PARÁMETER S
5.1 - PARAMETERS TABLE
“
]
SP” Group
(Set Point parameters)
Par.
Description
Range
Def.
1
SP1
TOP Set Point
SPL ÷ SPH
0
2
SP2
FLOOR Set Point
SPL ÷ SPH
0
3
SPL
(com)
Minimum Set Point
-99 ÷ SPH
0
4
SPH
(com)
Maximum Set Point
SPL ÷ 999
999
“
]
rG” Group
(temperature regulation and power control
parameters)
Par.
Description
Range
Def.
5
OP1
TOP power
0 ÷ 100 %
50
6
OP2
FLOOR power
0 ÷ 100 %
50
7
tCP
Power control Cycle time
1 ÷ 999 seg.
30
8
PSP
Power setting mode
1 - 2 – 3
1
9
HS1
Regulator differential 1
(TOP)
1 ÷ 999
2