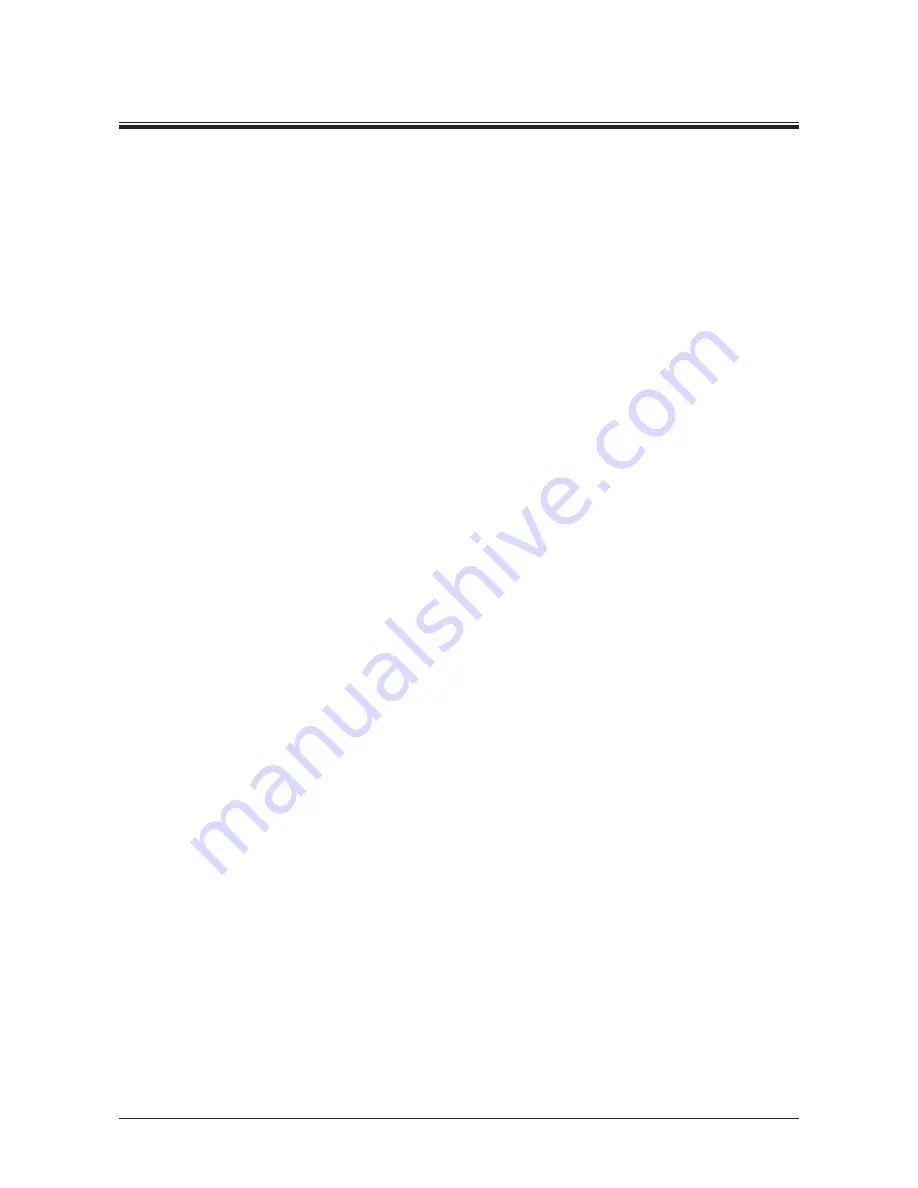
Precautions for use
−5−
2 Precautions for use
This chapter covers limitations and requirements the user should consider when using the product.
•
Connect protective devices to the power line
Connect a circuit breaker or earth leakage breaker to the driver’s power line to protect the primary circuit.
If an earth leakage breaker is to be installed, use one incorporating high-frequency noise elimination measures.
Refer to "Preventing leakage current" below for the selection of protective devices.
•
Do not perform vertical drive (gravitational operation).
The product will not be able to control the motor speed if an operation that the motor output shaft is externally rotated
is performed (vertical drive etc.). Also, if vertical drive is performed, since the inverter primary voltage of the circuit
may exceed the permissible range, the protective function may be activated. As a result, the motor may coast to a stop
and the load may fall.
•
Do not use a solid-state relay (SSR) to turn on/off the power
A circuit that turns on/off the power via a solid-state relay (SSR) may damage the motor and driver.
•
Conduct insulation resistance measurement or dielectric strength test separately on the motor
and the driver
Conducting the insulation resistance measurement or dielectric strength test with the motor and driver connected may
result in damage to the product.
•
Grease measures
On rare occasions, a small amount of grease may ooze out from the gearhead.
If there is a concern over possible environmental damage resulting from the leakage of grease, provide an oil tray or
similar oil catching mechanism in order not to cause a secondary damage.
Oil leakage may lead to problems in the customer’s equipment or products.
•
Caution when using under low temperature environment
When an ambient temperature is low, since the load torque may increase by the oil seal or viscosity increment of
grease used in the gearhead, the output torque may decrease or an overload alarm may generate. However, as time
passes, the oil seal or grease is warmed up, and the motor can be driven without generating an overload alarm.
•
Preventing leakage current
Stray capacitance exists between the driver’s current-carrying line and other current-carrying lines, the earth and the
motor, respectively. A high-frequency current may leak out through such capacitance, having a detrimental effect on
the surrounding equipment. The actual leakage current depends on the driver’s switching frequency, the length of
wiring between the driver and motor, and so on. When connecting an earth leakage breaker, use one of the following
products offering resistance against high frequency current:
Mitsubishi Electric Corporation: NV series
•
Noise elimination measures
Provide noise elimination measures to prevent a motor or driver malfunction caused by external noise.
For more effective elimination of noise, use a shielded I/O signal cable or attach ferrite cores if a non-shielded cable
is used. Refer to p.40 for the noise elimination measures.
•
Connecting the motor and driver
Use a connection cable (supplied or accessory) when extending the wiring distance between the motor and driver.
•
The driver uses semiconductor elements, so be extremely careful when handling them.
Electrostatic discharge can damage the driver.
•
Saving data to the non-volatile memory
The display blinks while pressing the setting dial to set the data or initializing the data (about 5 seconds). Do not turn
off the power supply while the display is blinking. Doing so may abort writing the data and cause an EEPROM error
alarm to generate.
The non-volatile memory can be rewritten approximately 100,000 times.
Summary of Contents for BMU5200A Series
Page 43: ...43...