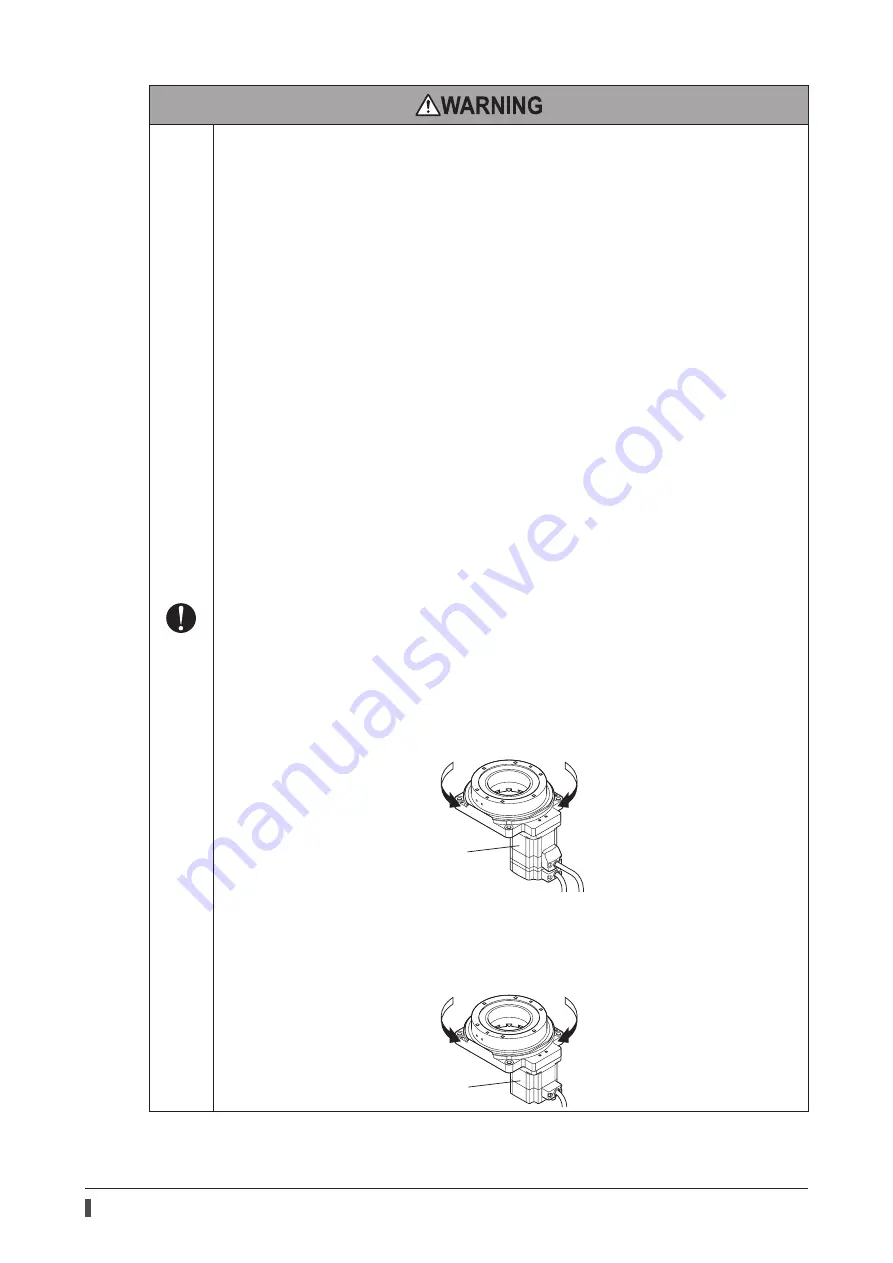
Safety precautions
10
•
Assign qualified personnel to the task of installing, wiring, operating/controlling, inspecting and
troubleshooting the product.
Failure to do so may result in fire, electric shock, injury or damage to equipment.
•
Take measures to keep the moving part in position if the product is used in vertical operations such as
elevating equipment.
Failure to do so may result in injury or damage to equipment.
•
Operate the data setter outside the safety fence.
Failure to do so may result in injury.
•
When an alarm is generated in the driver (any of the driver’s protective functions is triggered), take
measures to hold the moving part in a specific position since the actuator stops and loses its holding
torque.
Failure to do so may result in injury or damage to equipment.
•
Install the products inside an enclosure in order to prevent electric shock or injury.
•
When installing the product of Class I equipment defined in protection against electric shock, install so
that it is out of the direct reach of users, or ground if users can touch it.
Failure to do so may result in electric shock.
•
Provide an emergency stop device or emergency stop circuit external to the equipment so that the
entire equipment will operate safely in the event of a system failure or malfunction.
Failure to do so may result in injury.
•
Perform the return-to-home operation after the power is restored. When an actuator equipped with
the
AZ
Series is used, or when the absolute-position backup system is used in the built-in controller
type driver with an actuator equipped with the
AR
Series, execute positioning operation of the
absolute mode.
Failure to do so may result in injury or equipment damage.
•
Operate the actuator after setting the resolution, traveling direction and other parameters.
If the actuator is operated without setting parameters, the output table may move to unexpected
directions or run at unexpected speeds, causing injury or damage to equipment. (A variety of
parameters have been set to the actuator equipped with the
AZ
Series at the time of shipment.)
•
After replacing the driver, set the resolution, moving (rotating) direction or other parameters before
operating the actuator.
If the actuator is operated without setting parameters, the output table may move to unexpected
directions or run at unexpected speeds, causing injury or damage to equipment.
•
The output table of the actuator equipped with the
AZ
Series rotates in the same direction as the
driver input signal (CW input, CCW input).
CW and CCW indicate the rotation direction when viewed from the output table side.
Rotation direction
when inputting
the CW signal
Rotation direction
when inputting
the CCW signal
AZ
Series
•
The output table of the actuator equipped with the
AR
Series and the
RKII
Series rotates in the
opposite direction as the driver input signal (CW input, CCW input). When the CW signal is input, the
output table rotates in the counterclockwise direction. When the CCW signal is input, the output table
rotates in the clockwise direction.
CW and CCW indicate the rotation direction when viewed from the output table side.
AR
Series
RKII
Series
Rotation direction
when inputting
the CW signal
Rotation direction
when inputting
the CCW signal