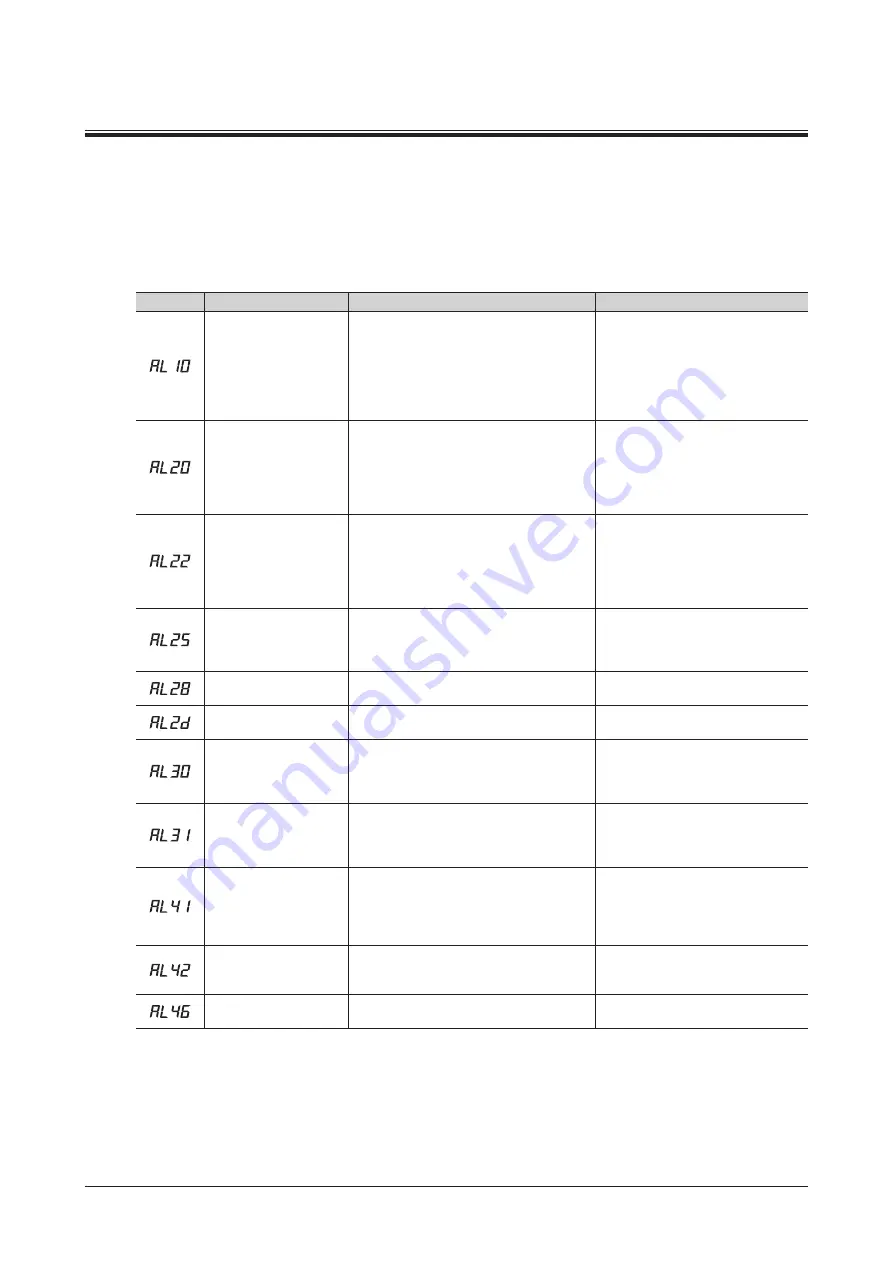
24
Protective function
10 Protective function
The driver provides alarms that are designed to protect the driver from overheating, poor connection, misoperation,
etc. (protective functions), as well as warnings that are output before the corresponding alarms are generated (warning
functions). Before resetting an alarm, always remove the cause of the alarm and ensure safety.
Refer to the USER MANUAL for how to reset an alarm.
10.1 Alarm list
Alarm code
Alarm type
Cause
Remedial action
Excessive position
deviation
•
When the motor was in an excitation state,
the deviation between the command position
and actual position at the motor output
shaft exceeded the value set in the “Excessive
position deviation alarm" parameter.
•
A load is large or the acceleration/deceleration
time is too short.
•
Decrease the load.
•
Reconsider the operating conditions
such as the acceleration/deceleration
time.
Overcurrent
Excessive current was flown through the driver
due to ground fault, etc.
•
Check whether the wiring between the
driver and motor is damaged.
•
If the alarm cannot be cleared even
when the power has been cycled,
contact your nearest Oriental Motor
sales office.
Overvoltage
•
The power supply voltage exceeded
approximately 120% of the rated voltage.
•
A load exceeding the allowable gravitational
capacity of the motor was driven or sudden
starting/stopping of a large inertia was
performed.
•
Check the voltage of the main power
supply.
•
If the alarm is generated during
operation, decrease a load or increase
the acceleration/deceleration time.
•
Connect the regeneration resistor.
Undervoltage
The power supply voltage dropped below
approximately 60% of the rated voltage.
•
Check the voltage of the main power
supply.
•
Check the wiring of the power supply
cable.
Sensor error
The encoder line of the motor was disconnected.
Or the encoder connector was come off.
Check the connection between the driver
and the motor.
Main circuit output error
∗1
The power line of the motor was disconnected.
Or the motor power connector was come off.
Check the connection between the driver
and the motor.
Overload
•
A load exceeding the rated torque was applied
to the motor for five seconds or more.
•
The motor was started in a state where the
motor temperature was low.
•
Decrease the load.
•
Reconsider the operating conditions
such as the acceleration/deceleration
time.
Overspeed
The rotation speed of the motor output shaft
exceeded approximately 5200 r/min.
•
Decrease the load.
•
Reconsider the operating conditions
such as the acceleration/deceleration
time.
EEPROM error
•
Stored data was damaged.
•
Data became no longer writable or readable.
•
Initialize all parameters.
•
If the alarm cannot be cleared even
when the power has been cycled,
contact your nearest Oriental Motor
sales office.
Initial sensor error
The encoder line of the motor was disconnected
before the main power supply was turned on.
Or the encoder connector was come off.
Check the connection between the driver
and the motor.
Alarm initial drive
∗2
The main power supply was turned on when
the operation input signal was being ON.
Turn the operation input signal OFF.
∗1
This alarm is not generated when the torque limiting value is set to less than 250%.
∗2
This alarm is generated when the “Alarm initial drive” function was set to enable.
Summary of Contents for BX2 Driver Edition Series
Page 7: ...7 Precautions for use...
Page 13: ...13 Installation...