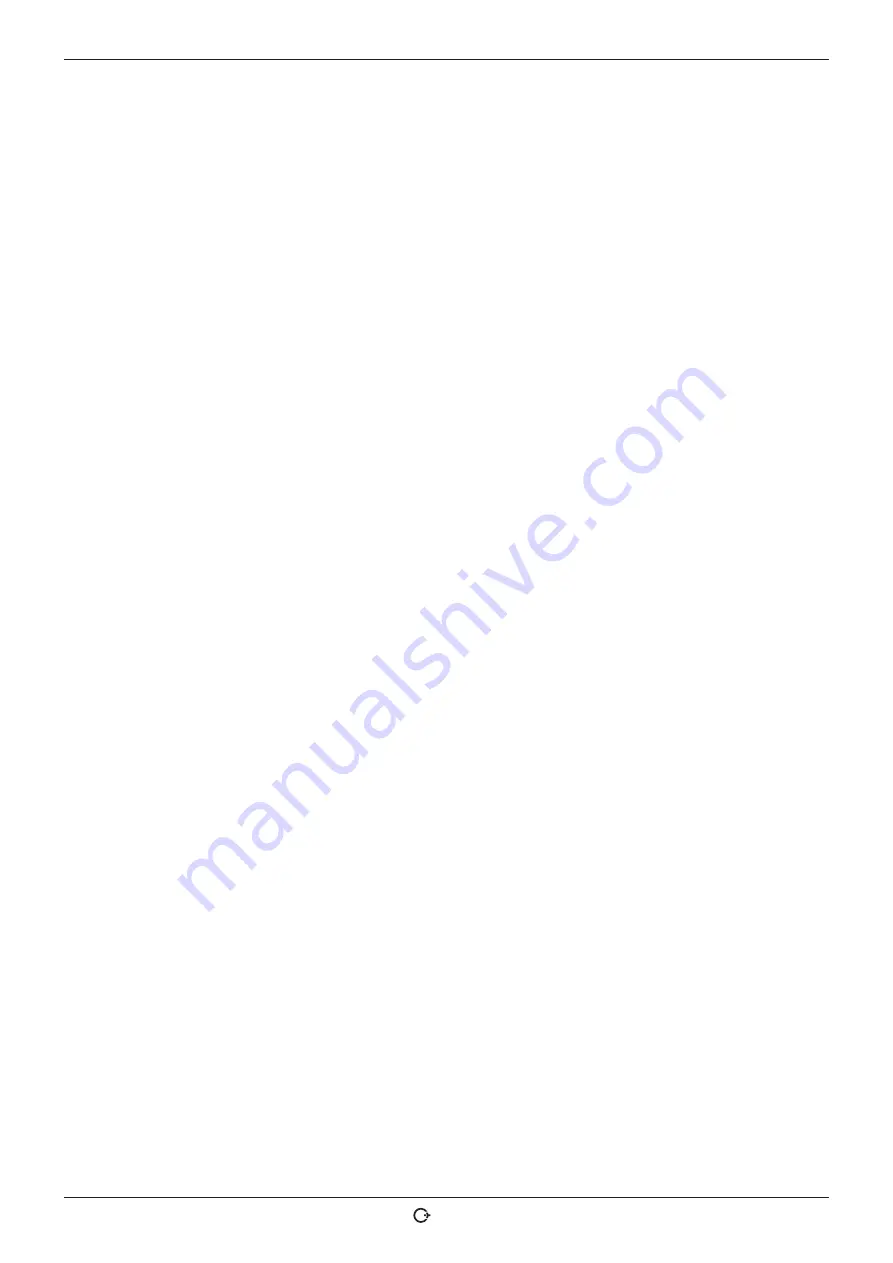
(12.03.18) OW_P16_P20_BA_831060202_03_EN
orbitalum tools
GmbH, D-78224 Singen, www.orbitalum.com, Tel. +49 (0) 77 31 792-0
11
P16, P16 AVC, P20
| Operating instructions
Technical specifications
On request can be supplied:
• Cage with support ring for welding of flush tubes.
• Internal bore welding torch (L= up to 400 mm), tube diam 9,5 to 80 mm.
• Front dual flow cage for second gas (for titanium welding e.g.), at request with three point support.
We would like to remind you that our staff is able to design special torches for special applications or welding geome-
tries as well as prolonged torches for welding in hardly accessible areas.
3.3.1
Main body and rotating coupling
This group is composed of the following main items or subassemblies:
• Connection block to the main cable for cooling water, welding current and protection gas.
• Electric socket for connection to the welding programmer.
• Rotation joint spindle and main distributor for cooling water, protection gas and welding current. The electrical
contact between the parts is obtained by means of a lamellar joint.
• Self-lubrificating bearings for supporting the rotation joint spindle.
• Standard rotation gear motor. (On request with tachometer feedback).
• Coupling between crown wheel-pinion for transmission of rotation from the gear-motor to the welding head.
• Electro mechanic pulse-counter for controlling the welding cycle with respect to the torch position. The microswitch
is actuated by a wheel with 20 cams which supplies 60 impulses during a 360° rotation of the torch.
• External body with hook. (Standard for welding in horizontal position).
• Mandrel support vessel machined out of stainless steel.
• Ball bearing which allows the rotation of the mandrel support vessel and the front group for external and internal
bore welding.
• Socket.
• Start/Stop button for starting the welding cycle or act the emergency stop (if pushed during the cycle).
3.3.2
Filler wire group
• Filler wire gear-motor.
• Pair of wire feed rollers. On the machine usually are mounted rollers for wire 0,6 - 0,9 mm.
• Wire spool support Standard spool has following dimensions:
- external diameter: 100 mm
- min. wire coiling diameter: 40 mm
• Elastic (spring loaded) blocking device which avoids by a clutch-disc system the unrolling of the spool.
• Filler wire arrival group which is composed of:
- guide nozzle
- wire exit guide
- wire entry guide and rear entry nipple
- rear wire guide hose
- front wire guide hose
- shaft with insulating bushing
- shaft support