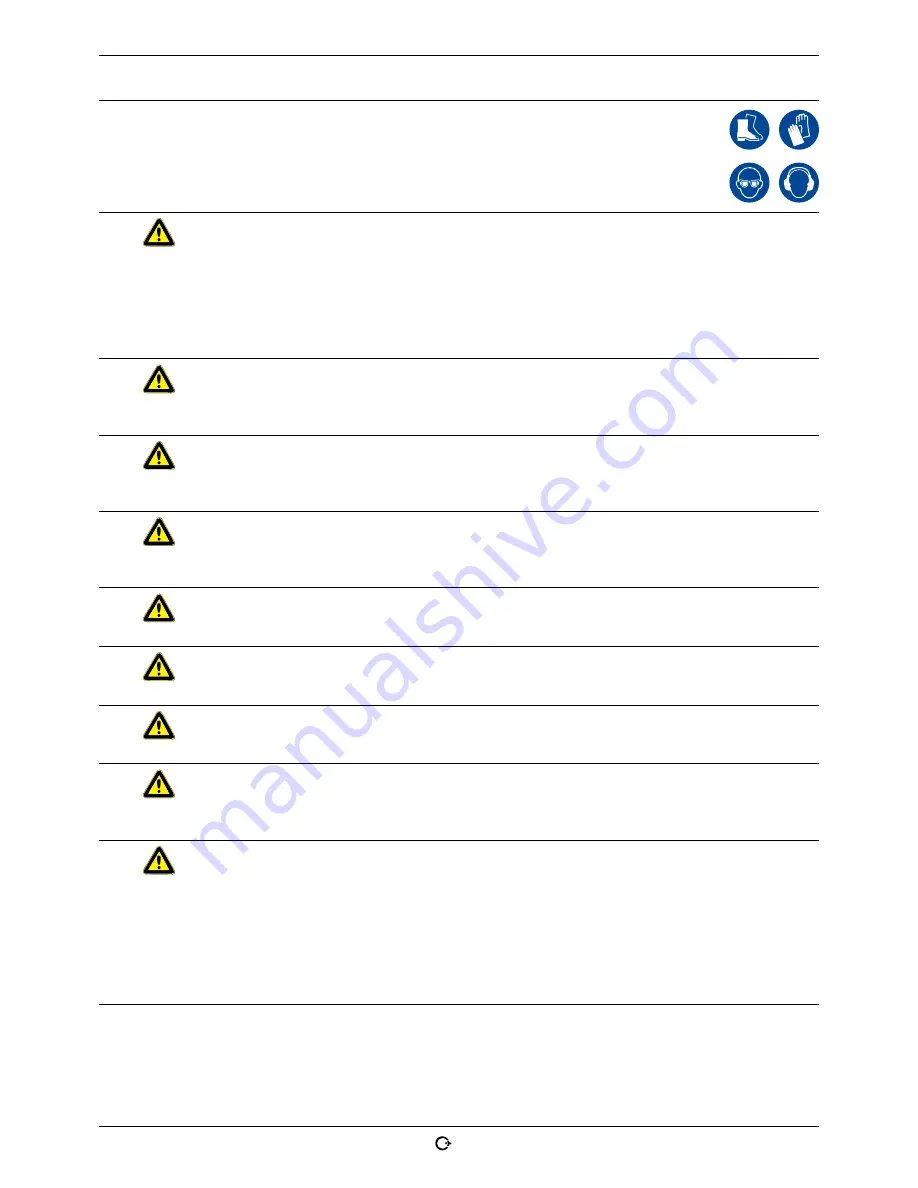
(18.12.17) OC_GFX_BA_790144762_00_EN
orbitalum tools
GmbH, D-78224 Singen, www.orbitalum.com, Tel. +49 (0) 77 31 792-0
9
GFX 3.0, GFX 6.6
| Operating instructions
Information and safety instructions for the responsible body
NOTE
The recommendations concerning "Personal protective equipment" only
apply to the product being described. Other requirements resulting from
the ambient conditions on-site or of other products, or from combining with
other products, are not taken into account. These recommendations do not
in any way release the responsible body (employer) from its statutory health
and safety at work obligations towards its employees.
DANGER
If the mains cable is damaged, live parts may cause death if touched directly!
Fatal electric shock.
[
Keep the mains cable of the tube saw motor away from the saw blade and/or bevel cutter.
[
Do
not
let the cut-off tube piece drop in an uncontrolled manner.
[
Do
not
run the machine unattended.
X
During processing, always keep an eye on the position of the mains cable.
X
Secure the falling tube piece.
X
Keep the machine clean. Always remove lubricant residues from the machine.
DANGER
Damaged insulation!
Fatal electric shock.
[
Do
not
screw any indicators or signs to the drive motor.
X
Use stickers.
DANGER
Metal dust can collect in the motor housing and cause loss of insulation!
Fatal electric shock.
X
Depending on the level of contamination, clean the machine at least once a day using the brush
supplied.
DANGER
Damaged plug!
Fatal electric shock.
[
Do
not
use adapter plugs with ground protected electrical tools.
X
The machine connector plug must fit the socket.
DANGER
Risk of danger through the use of the machine outdoors!
Fatal electric shock.
[
Do
not
use the machine outdoors.
DANGER
Danger! The electrical motor can overheat with operation of less than 230 V network!
Serious injury or death.
X
Only use the machine in the specified temperature range.
DANGER
Grounded body!
Fatal electric shock.
X
Avoid contact with grounded surfaces such as tubes, heating, cookers or refrigerators.
DANGER
Loose/baggy clothing, long hair or jewelry can get caught in rotating machine parts!
Serious injury or death.
X
Wear tight-fitting clothing when using the machine.
X
Tie up long hair to prevent it from being caught.
DANGER
Defective safety components due to soiling, breakage and wear!
The failure of safety components can cause physical injury.
[
Do
not
misuse the cable, e.g. such as using it to suspend or carry the machine.
X
Replace defective safety components immediately and check them daily to ensure proper operation.
X
Have an expert replace defective power cables immediately.
X
Clean and perform maintenance on the machine after each use.
X
Keep cables away from heat, oil, sharp edges and moving equipment parts.
X
Inspect the machine daily for visible signs of damage or defects, and have them repaired by a
specialist if necessary.