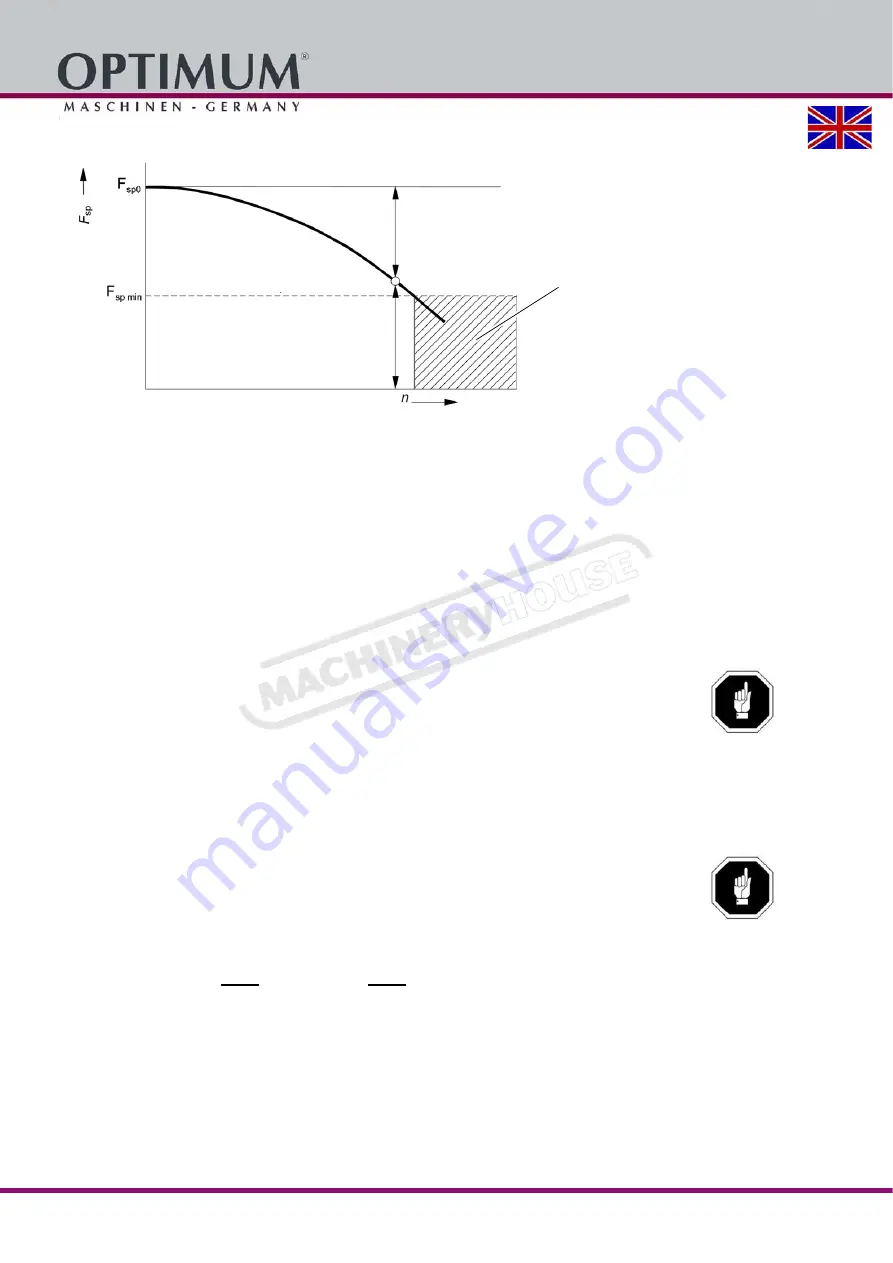
Version 1.1.6 - 2021-09-17
64
Translation of original instruction
3442761
GB
K11-
160_I
SO
-702
-2_3
4427
61_b
a-int
egr
at
ed_G
B.
fm
The required effective clamping force for machining F
sp
is calculated from the product of the
machining force F
spz
with the safety factor S
z
. This factor takes into account uncertainties in the
calculation of the clamping force.
According to VDI 3106, the following also applies here:
From this we can derive the calculation of the initial clamping force during shutdown:
ATTENTION!
This calculated force must not be larger than the maximum clamping force
∑
S
( 24 KN )
engraved on the chuck.
From the above formula it is evident that the sum of the effective clamping force F
sp
and the
total centrifugal force F
c
is multiplied by the safety factor for the clamping force S
sp
.
According to VDI 3106, the following also applies here:
The total centrifugal force F
c
is dependent both on the sum of the masses of all jaws and on the
center of gravity radius and the RPM.
ATTENTION!
For safety reasons, in accordance with DIN EN 1550, the centrifugal force may be a
maximum of 67% of the initial clamping force.
The formula for the calculation of the total centrifugal force F
c
is:
n is the given speed in r.p.m.. The product
m
B
· r
s
is described as the centrifugal
force torque
M
c
.
Base tensioning force
Required minimum tensioning force
C
lam
p
ing
fo
rc
e
Cen
trifugal force
Speed
Ef
fec
tive
tensio
ning f
orce
Workpiece is
released uncontrollably
F
sp
= F
spz
·
S
z
[ N ]
F
sp0
= S
sp
·
(F
sp
± F
c
) [ N ]
- for gripping from the outside in
+ for gripping from the inside out
S
sp
≥
1.5
F
c
=
∑
(m
b
·
r
s
)
·
π
·
n
30
(
)
2
=
∑
M
c
·
π
·
n
30
(
)
2
[N]
M
c
= m
B
·
r
s
[ kgm ]