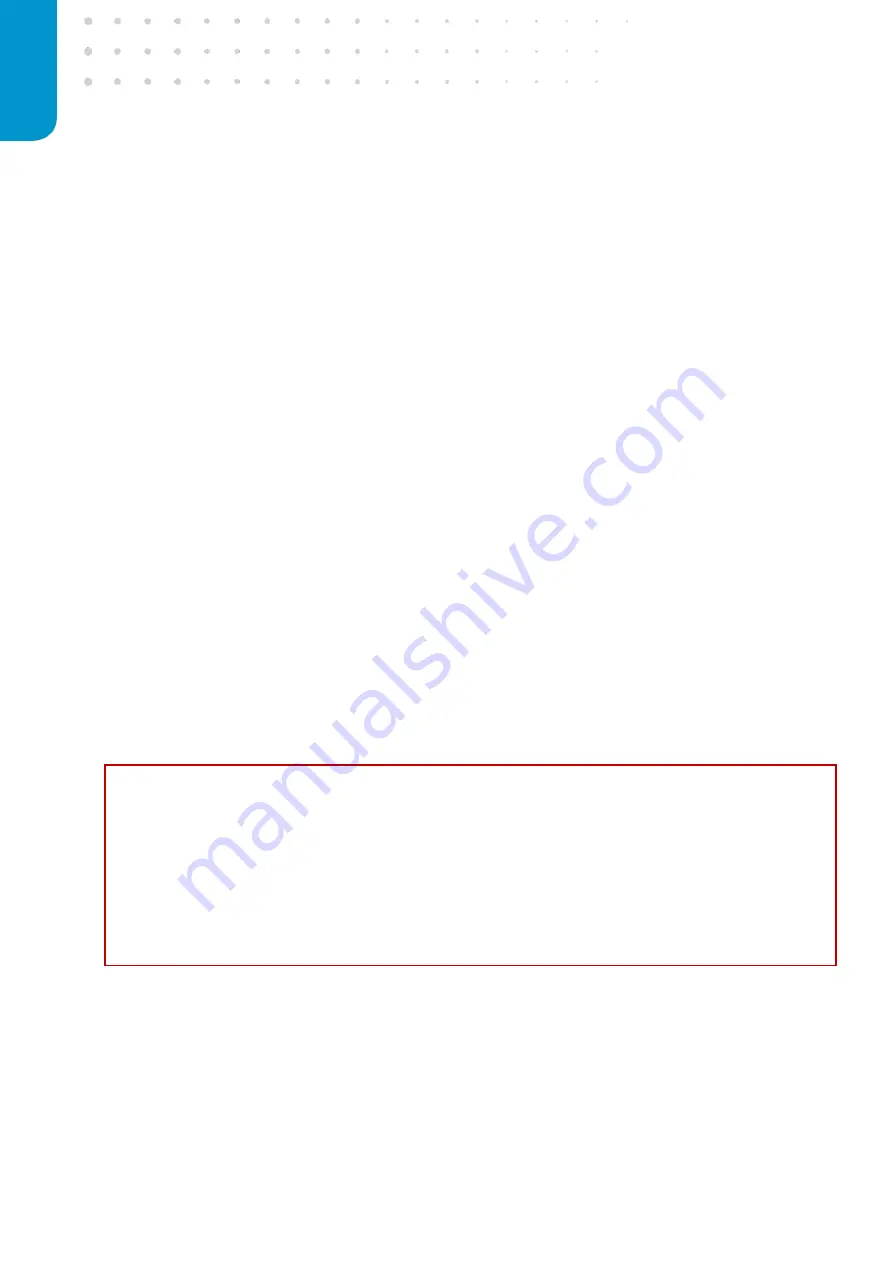
24
optics11life.com
9.
During the signal linearization, the interference signal measured at the detector (Volts over time)
is transformed into a linear signal of cantilever bending (µm over time), using the unit circle as a
linearization tool. You can find the unit circle or so-called demodulation circle in one of the tabs
of the LCD screen of the interferometer (see
-e). Sensitivity is already set in the
interferometer (µm/V) and used to translate Volts to µm.
10.
The geometrical factor called
‘calibration factor’
originates from the mismatch in the spherical tip
position and the readout fiber position (see
-a). By indenting on a stiff surface, the
distance is measured by the fiber can be compared with the distance that piezo displaced. Taking
the ratio between them gives a geometrical factor that is used to correct the cantilever signal by
multiplying it.
11.
During the calibration step, the piezo will move down twice by the amount set in the ‘Options’
menu ‘Calibration depth (nm)’. We recommend using the value between 5000 and 10000 nm. If
‘live calibration’ is used
(you can check it in maintenance)
, decrease ‘Calibration distance’ to 3000
nm (explained in Section 6.2). Check that in the live signal window both piezo and cantilever
signals move up at the same time as shown in
-b, left. If there is a mismatch in time
-b, right), it means that the probe is close to contact but not fully in contact when piezo
starts to move. Manually move down the probe with steps of 1um until you see that the baseline
of the cantilever signal has changed. If the cantilever signal does not change at all during
calibration, it means that the probe is far away from the sample. Repeat calibration procedure
from the wavelength scan step.
Caution:
During the calibration step, ensure the probe is in contact with a stiff surface.
12.
When calibration is completed, ‘New factor’ is given.
By pressing
‘U
se new factor
’
the software
automatically saves the
new ‘Calibration
factor
’
in the probe configuration menu (see
c). The calibration factor should be ~1.33 times lower in the medium than it is in the air which is
given on the box of the probe, e.g. if the number on the box is 3.2, then the geometrical factor in
the medium should be 3.2
÷
1.33
≈
2.4. When repeating geometrical factor calibration, only a small
variation is expected <5%. If calibration has failed, see below the possible reasons. You can also
check in Load-Indentation data that loading and unloading data overlap and are straight slopes
(see
-d). The small mismatch is expected due to drift and hysteresis in piezo movement.
Reasons for failed calibration:
•
The tip is not in contact with the surface during calibration (go to step 7).
•
Attractive forces between tip and surface
–
snap-on behavior results in the calibration of the over-
bended cantilever
–
clean probe and the surface or use Teflon surface for calibration (shite
substrate).
•
Dirty tip or surface
–
clean the probe with demi water & Isopropanol & water again.
•
Air bubble between the cantilever and tip fiber
–
Get rid of the air bubble (see Figure 18-d).
Cantilever stuck at the tip fiber
–
dry it and unstuck with a piece of paper (seeFigure 18-a to c).
•
Repeat wavelength scan before calibrating again.
13.
Next, check whether the demodulation circle was calibrated correctly. Either tap on the body of
Pavone to induce a sufficient amount of noise to see the whole white signal around the red
demodulation circle or move down the probe at small steps e.g. 1 µm. In both cases, the white
signal should overlap with the red circle.
Caution:
If during the operation of the instrument, you observe that the white signal
is not on the red demodulation circle or you get a warning from the system about it,
you need to recalibrate the demodulation circle. This can be done in two ways: 1)