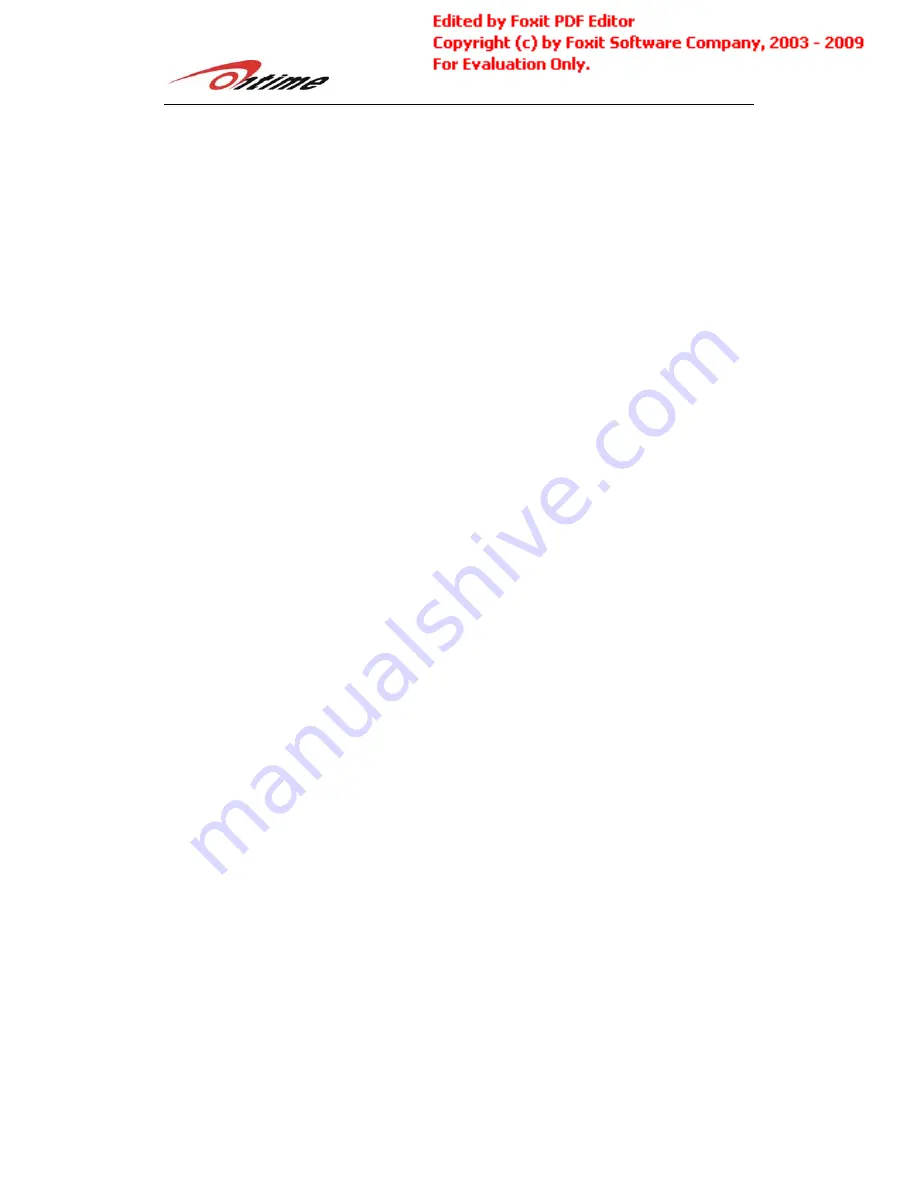
SHENZHEN ONTIME TECHNOLOGY CO.LTD
3
IHS (Initial Height Setup) mode:
Inductive proximity switch mode.
Torch tip ohmic contact mode, only be suited for the
plasma power which has less HF and HV interferences
and working in dry cutting condition.
Arc voltage divider ratio: 1:100.
Accuracy: ±1V to ±5V adjustable.
Outline: 240mm/210mm/60mm(L/W/H).
Summary of Contents for AVC118
Page 4: ...SHENZHEN ONTIME TECHNOLOGY CO LTD 4 Pictures...
Page 27: ...27...