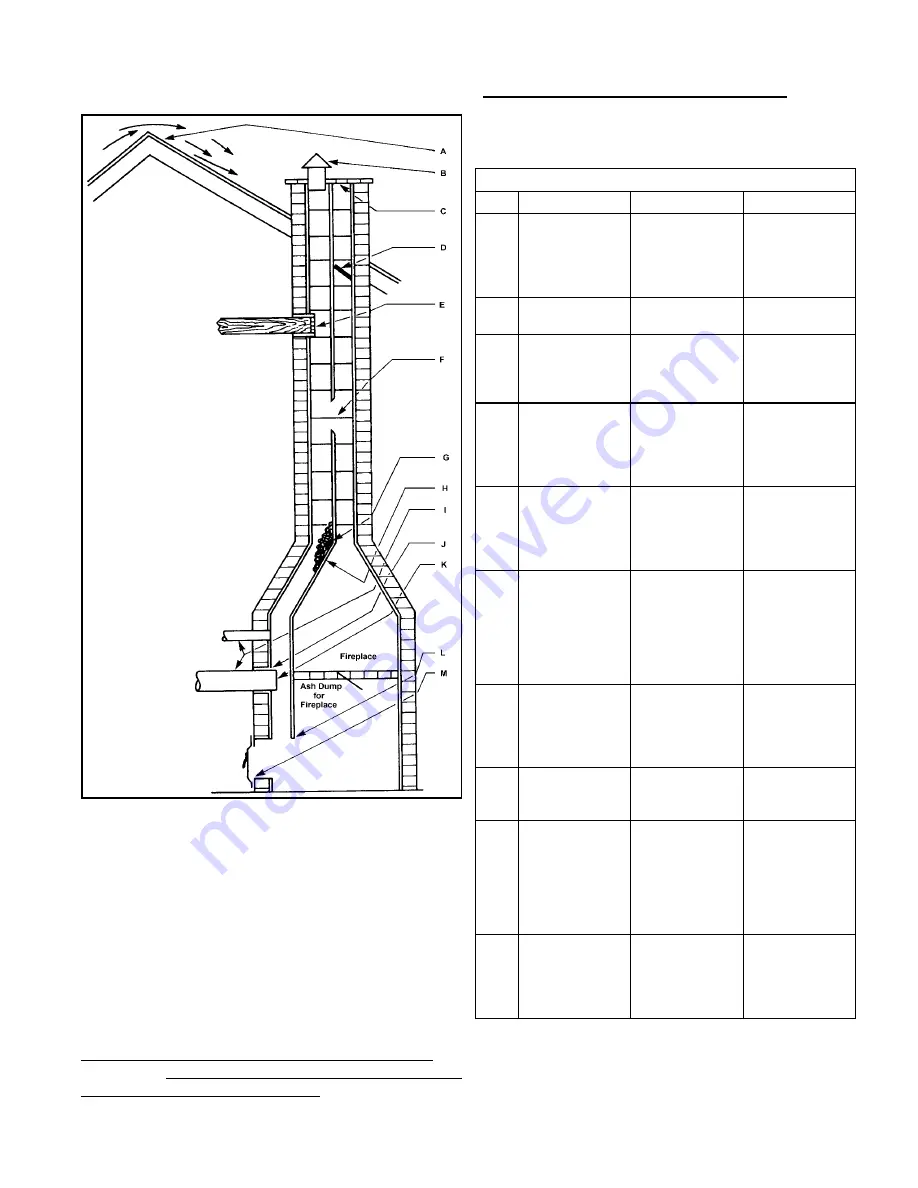
29733 R2 06/01/2003
7
Figure 2: Common Chimney Problems
6. CHIMNEY VENTING
The chimney must be sized correctly and be in good
repair. If the chimney is oversized, there is a high risk of
the flue gases condensing resulting in damage to the
chimney and other venting parts. This problem may be
corrected by the use of an appropriately sized chimney
liner.
If the chimney serves the furnace only, the vent should
be sized at 4 inch minimum, 5 inch maximum. The table
below is based on dedicated venting. If the furnace is to
be co-vented with other appliances, refer to
NFPA 31
,
Standard for the Installation of Oil Burning Equipment
and
NFPA 211
,
Standard for Chimneys, Fireplaces, Vents,
and Solid Fuel-Burning Appliances
or
CAN/CSA B139
,
Installation Code For Oil Burning Equipment
for correct
sizing information
Table 3: Common Chimney Problems
Refer to Figure 2
Key Trouble Diagnostic Remedy
A
Top of chimney
lower than
surrounding
objects
Observation
Extend
chimney above
all surrounding
objects within
30 feet.
B
Chimney Cap
or ventilator.
Observation Remove
C
Coping restricts
opening.
Observation
Make opening
as large as
inside of
chimney.
D
Obstruction in
chimney
Can be found
by light and
mirror reflecting
conditions in
chimney.
Use weight to
break and
dislodge.
E
Joist protruding
into chimney.
Lowering a light
on an extension
cord.
Must be
handled by
competent
masonry
contractor.
F
Break in
chimney lining.
Smoke test -
build smudge
fire blocking off
other opening,
watching for
smoke to
escape.
Must be
handled by
competent
masonry
contractor.
G
Collection of
soot at narrow
space in flue
opening.
Lower light on
extension cord.
Clean out with
weighted brush
or bag of loose
gravel on end
of line.
H Offset
Lower light on
extension cord.
Change to
straight or to
long offset.
I
Two or more
openings to the
same chimney.
Found by
inspection from
basement.
The least
important
opening must
be closed,
using some
other chimney
flue.
J
Loose-seated
pipe in flue
opening.
Smoke test.
Leaks should
be eliminated
by cementing
all pipe
openings.